Advanced Upholstery Welding Methods for Professionals
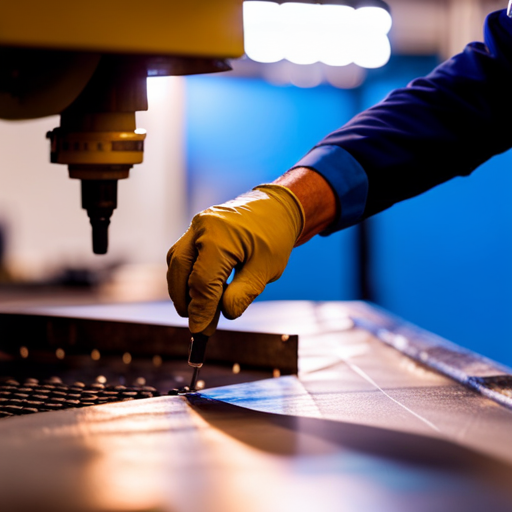
Did you know that advanced upholstery welding methods can improve production efficiency by up to 30%?
In this article, we explore the latest advancements in high-frequency, hot air, hot wedge, ultrasonic, and laser welding techniques for upholstery professionals.
From innovative bonding agents to cutting-edge adhesives, this comprehensive guide provides insights into the most effective methods for achieving durable and aesthetically pleasing upholstery welds.
High-Frequency Welding Techniques
High-frequency welding techniques utilize electromagnetic energy to bond upholstery materials with precision and efficiency, meeting the high standards of professional upholstery work. The benefits of high-frequency welding in upholstery are numerous.
It offers a clean and precise bond, ensuring a seamless finish that meets the aesthetic and functional requirements of various applications. This technique also provides a strong and durable bond, enhancing the longevity and performance of upholstered products. Additionally, high-frequency welding allows for increased productivity as it enables rapid assembly and production processes, making it ideal for industrial applications.
In the industrial sector, high-frequency welding is extensively used for manufacturing upholstery products such as automotive interiors, furniture, medical equipment, and more. Its ability to create strong and seamless bonds makes it particularly suitable for producing items that require enhanced structural integrity and durability. Furthermore, the efficiency and precision of high-frequency welding make it a cost-effective solution for industrial upholstery production, reducing material waste and labor costs.
Hot Air Welding Methods
In the realm of upholstery welding methods, hot air welding stands as a prominent technique offering unique advantages.
This method allows for precise control over welding temperature, ensuring optimal results in various upholstery projects.
Additionally, understanding the compatibility of different materials is crucial for successful hot air welding, making it essential to consider material-specific tips for achieving high-quality welds.
Hot Air Advantages
The hot air welding method offers professionals a precise and efficient technique for joining upholstery materials. This method has several advantages that make it a preferred choice for professionals in the industry.
Some of the key benefits of hot air welding include:
-
Welding Equipment: Hot air welding requires minimal equipment, making it a cost-effective option for professionals.
-
Seam Sealing: This method provides a strong and durable seam seal, ensuring the longevity and quality of the upholstery.
-
Precision: Hot air welding allows for precise control, ensuring accurate and clean joins between upholstery materials.
-
Efficiency: Professionals can complete projects in a timely manner due to the efficiency of hot air welding, resulting in increased productivity and cost savings.
Welding Temperature Control
Temperature control is a critical aspect of hot air welding methods for upholstery professionals. Proper temperature regulation is essential for achieving high welding seam quality. The temperature must be carefully controlled to ensure the welding process creates strong, durable seams. Excessive heat can lead to material damage, while insufficient heat may result in weak seams.
Additionally, welding speed is interconnected with temperature control. The ideal welding speed must be maintained to correspond with the controlled temperature. A balanced combination of welding speed and temperature control is crucial for achieving optimal results in hot air welding.
Upholstery professionals must meticulously monitor and adjust these factors to ensure the integrity and longevity of the welded seams.
Material Compatibility Tips
To ensure optimal results in hot air welding methods, upholstery professionals must carefully consider the compatibility of materials. This involves assessing the specific characteristics of the materials to be joined, using a quantifier determiner.
Here are four essential material compatibility tips to enhance the hot air welding process:
-
Material Adhesion: Prioritize materials with similar melting points and adhesive properties to ensure a strong and durable weld.
-
Stitching Alternatives: Explore materials that may not be suitable for traditional stitching but can be effectively welded together using hot air methods.
-
Heat Resistance: Select materials that can withstand the heat generated during the welding process without compromising their structural integrity.
-
Chemical Compatibility: Consider the chemical composition of the materials to prevent adverse reactions during the welding process.
Hot Wedge Welding Innovations
An essential technique for professionals in the upholstery industry, hot wedge welding innovations have revolutionized the precision and efficiency of seam sealing in fabric applications. Welding equipment advancements have played a crucial role in enhancing the hot wedge welding process efficiency. The introduction of advanced hot wedge welding machines with precise temperature control and automatic pressure adjustment features has significantly improved the quality and speed of seam sealing.
These welding equipment advancements allow professionals to achieve consistent and durable seams, even when working with challenging fabrics such as coated materials or heavy textiles.
Furthermore, the welding process efficiency has been optimized through the integration of cutting-edge technologies that enable faster heating and cooling cycles. This not only reduces production time but also minimizes the risk of material distortion or damage during the welding process. As a result, professionals can confidently work on a wide range of upholstery projects with the assurance of achieving impeccable seam sealing results.
Ultrasonic Welding Applications
One of the most efficient methods for seam sealing in the upholstery industry is ultrasonic welding, offering precise and rapid bonding of fabric components. With ultrasonic bonding, high-frequency ultrasonic acoustic vibrations are used to create heat through friction, melting the materials and forming a strong bond without the need for additional adhesives or stitching.
The applications of ultrasonic welding in upholstery are numerous and include:
-
Seam Sealing: Ultrasonic welding allows for precise and secure seam sealing, ensuring that the fabric components are seamlessly bonded together.
-
Decorative Stitching: This method enables intricate decorative stitching patterns to be achieved with exceptional welding precision, enhancing the visual appeal of upholstered products.
-
Quilting and Embossing: Ultrasonic welding can be employed for quilting and embossing fabric layers, providing texture and dimension to upholstery materials.
-
Customized Designs: The flexibility of ultrasonic welding allows for the creation of custom-designed patterns and textures, catering to diverse upholstery requirements.
As ultrasonic welding continues to revolutionize the upholstery industry, its efficiency and precision make it a highly sought-after method for professionals.
Transitioning from ultrasonic welding, the subsequent section will delve into the innovative applications of laser welding for upholstery.
Laser Welding for Upholstery
Continuing the exploration of advanced welding methods in the upholstery industry, laser welding presents a cutting-edge approach for achieving precise and durable seam bonding without the need for traditional adhesives or stitching. Laser welding precision ensures that the seams are seamless, providing a clean and aesthetically pleasing finish to upholstered products. This method offers several advantages, including reduced material waste, increased production efficiency, and improved seam strength.
Advantages of Laser Welding for Upholstery | |
---|---|
Precision | Laser welding enables precise control over the heat input, resulting in accurate and consistent seam bonding. |
Seamlessness | The seamless finish achieved through laser welding enhances the overall appearance of upholstered products. |
Efficiency | Laser welding reduces production time and labor costs by eliminating the need for additional adhesives or stitching. |
Strength | The seams created through laser welding exhibit exceptional strength and durability, ensuring the longevity of upholstered items. |
Incorporating laser welding into upholstery manufacturing processes can lead to enhanced product quality and cost savings, making it a valuable technique for professionals in the industry.
Advanced Bonding Agents and Adhesives
How can advanced bonding agents and adhesives complement laser welding in achieving superior seam bonding for upholstered products?
Advanced bonding agents and adhesives play a crucial role in achieving durable and aesthetically pleasing upholstery seams. When combined with laser welding, they enhance the overall strength and longevity of the seams, ensuring high-quality upholstered products.
Here are four ways advanced bonding agents and adhesives contribute to superior seam bonding:
-
Enhanced Durability: Advanced bonding agents are formulated to withstand the rigors of daily use, ensuring that the seams remain strong and intact over time.
-
Improved Aesthetics: Adhesive properties such as transparency and precise application allow for seamless bonding, resulting in visually appealing upholstery seams.
-
Flexibility and Comfort: Utilizing bonding techniques that maintain the flexibility of the materials, adhesive properties contribute to the overall comfort and usability of upholstered products.
-
Resistance to Environmental Factors: Advanced adhesives are designed to resist moisture, heat, and other environmental factors, ensuring that the seams remain robust in various conditions.
Frequently Asked Questions
What Are the Most Common Challenges Professionals Face When Using Advanced Upholstery Welding Methods?
Professionals often encounter challenges when utilizing advanced upholstery welding methods, requiring troubleshooting techniques for optimal performance. Technological advancements play a key role in addressing these challenges, paving the way for future developments in the field.
Are There Any Safety Considerations or Precautions That Professionals Should Be Aware of When Using These Advanced Welding Techniques?
When using advanced upholstery welding methods, professionals must prioritize safety precautions and equipment maintenance. It’s essential to conduct thorough risk assessments and ensure the use of appropriate protective gear to mitigate potential hazards in the workplace.
How Do These Advanced Welding Methods Compare in Terms of Cost and Efficiency?
When comparing advanced welding methods in terms of cost and efficiency, it is important to consider factors such as initial investment, operating expenses, and productivity gains. Conducting a comprehensive analysis will provide valuable insights for decision-making.
Can These Advanced Welding Methods Be Used on a Variety of Upholstery Materials, or Are They Limited to Specific Types?
When considering material compatibility for welding techniques, it’s essential to assess the specific requirements of each material. While some advanced welding methods may be suitable for a variety of upholstery materials, others may be limited to specific types.
Are There Any Special Training or Certification Requirements for Professionals Looking to Use These Advanced Upholstery Welding Methods?
Professionals seeking to use advanced upholstery welding methods may need specialized training and certification. These requirements ensure proficiency in handling the equipment, understanding safety protocols, and delivering high-quality results. A comprehensive certification process may be necessary.
Conclusion
In conclusion, advanced upholstery welding methods offer professionals a range of innovative techniques to achieve superior results.
From high-frequency and hot air welding to hot wedge and ultrasonic welding, as well as laser welding and advanced bonding agents, the possibilities are endless.
These methods not only provide efficiency and precision but also elevate the craft of upholstery to new heights, inspiring creativity and excellence in the industry.
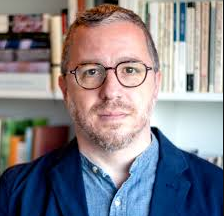
Dillon Hince, an expert in the realm of upholstery welding, brings a wealth of knowledge and experience to the craft. As the driving force behind nodpu.com, Dillon combines a passion for precision and creativity, offering unique insights into the art of seamlessly melding fabrics and materials. With a commitment to excellence, Dillon Hince is your go-to resource for innovative upholstery welding techniques, transforming ordinary pieces into extraordinary works of functional art.