Innovative Tools in Upholstery Welding
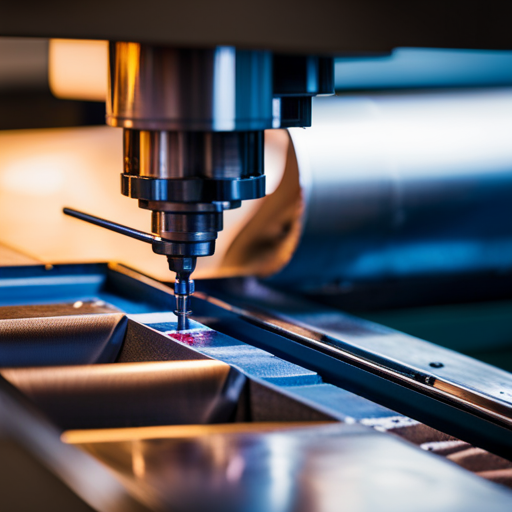
Did you know that the upholstery industry has seen a 20% increase in demand for innovative welding tools in the past year?
As the demand for high-quality upholstery continues to rise, the need for advanced welding solutions has become essential.
From heat guns to handheld welders and welding machines, the market is evolving with cutting-edge technology.
In this article, we will explore the latest advancements in upholstery welding tools and their impact on the industry.
Heat Guns
Heat guns are widely used in upholstery welding for their efficient heat application and precise control. When it comes to precision welding, heat guns play a crucial role in ensuring the seamless joining of upholstery materials. One of the key advantages of heat guns is their ability to provide uniform heat distribution, which is essential for achieving high-quality welds. This even distribution of heat helps prevent overheating in certain areas, reducing the risk of damage to the materials being welded.
The precise control offered by heat guns allows upholsterers to accurately target specific areas, ensuring that the welding process is carried out with the utmost accuracy. This level of control is particularly important when working with delicate or intricate upholstery designs, where precision is paramount. Upholsterers rely on the consistent and reliable heat output of these tools to create strong and durable welds without compromising the integrity of the materials.
Handheld Welders
Handheld welders are a valuable tool in upholstery welding due to their versatility, allowing for various welding options. These tools provide precision in small spaces, enabling upholstery professionals to work with intricate designs and tight corners.
Additionally, handheld welders are portable and efficient, making them a practical choice for upholstery welding projects of all sizes.
Versatile Welding Options
One notable option for upholstery welding is the handheld welder. It offers versatility and precision for various welding applications. Handheld welders provide customized solutions tailored to meet industry standards. They enable innovative applications and facilitate the creation of creative designs.
The versatility of handheld welders allows for seamless welding across different materials, including fabrics, plastics, and leather. Their precision makes them suitable for delicate upholstery work, ensuring clean and durable welds.
Furthermore, these handheld welders are portable, allowing for flexibility in welding operations, whether in a workshop or on-site. With their ergonomic design and user-friendly interface, handheld welders are an essential tool for upholstery professionals seeking efficient and high-quality welding solutions.
Precision in Small Spaces
The precision of a handheld welder makes it an indispensable tool for upholstery professionals working in confined spaces. Precision welding techniques are crucial for creating seamless upholstery, and compact welding solutions enable professionals to achieve this level of precision even in small, hard-to-reach areas.
Handheld welders provide the accuracy and control necessary to produce clean and durable welds in tight spaces, ensuring the quality and integrity of the upholstered pieces. These tools are designed to deliver precise heat and pressure, allowing for meticulous welding without compromising the surrounding materials.
Portable and Efficient
Achieving precision in small spaces necessitates the use of portable and efficient welding tools, which are indispensable for maintaining high standards of craftsmanship in upholstery work across various settings.
Handheld welders offer a lightweight design, combining portability with powerful performance, enabling upholsterers to work with ease and efficiency. The mobility provided by these handheld welders allows for intricate and precise welding in tight or hard-to-reach areas, ensuring a seamless finish.
Upholsterers can rely on the precision offered by these tools to achieve clean and durable welds, even in challenging positions. The combination of portability, lightweight design, powerful performance, and precision in upholstery welding makes handheld welders essential for professionals seeking to elevate the quality of their work.
Welding Machines
Welding machines are at the forefront of advanced welding technologies, offering precision and speed in upholstery welding processes. These versatile pieces of equipment provide the capability to work with a variety of materials and perform intricate welding tasks.
In the upcoming discussion, we will explore the significant impact of welding machines on the efficiency and quality of upholstery welding.
Advanced Welding Technologies
Several modern upholstery workshops have adopted advanced welding technologies to enhance efficiency and precision in fabricating furniture pieces. These advanced welding technologies include:
-
Laser welding: Utilizes a focused beam of light to join upholstery materials with high precision.
-
Robotic welding: Employs automated robotic arms to weld upholstery components consistently and accurately.
-
Ultrasonic welding: Uses high-frequency ultrasonic vibrations to create strong molecular bonds between upholstery materials.
-
Friction stir welding: Involves a non-melting process where frictional heat softens the upholstery materials, allowing them to be forged together seamlessly.
These advanced welding technologies not only improve the quality of upholstered furniture but also contribute to increased productivity and cost-effectiveness in upholstery workshops.
Welding Precision and Speed
The implementation of state-of-the-art welding machines greatly enhances the precision and speed of upholstery welding processes in modern workshops. Welding automation and efficiency are achieved through the utilization of digital welding technologies, ensuring accuracy in the fabrication of upholstered products.
These advanced machines are equipped with precise controls and automated features that allow for the rapid and consistent welding of upholstery materials, resulting in increased productivity and high-quality output. Digital welding systems contribute to the efficiency of the welding process by enabling quick adjustments and precise parameter settings, thereby reducing the time required for each welding operation.
As we delve further into the discussion of versatile welding equipment, it becomes evident that these innovations are revolutionizing the upholstery welding industry, offering unprecedented levels of precision and speed.
Versatile Welding Equipment
The implementation of state-of-the-art welding machines greatly enhances the precision and speed of upholstery welding processes in modern workshops. These advanced machines are equipped with precise controls and automated features that allow for the rapid and consistent welding of upholstery materials, resulting in increased productivity and high-quality output.
-
Customized Solutions: Modern welding machines offer the flexibility to adapt to various upholstery materials and designs, providing customized solutions for different welding needs.
-
Industry Standards: These machines meet the stringent industry standards for welding, ensuring that the upholstery products meet the required quality and durability benchmarks.
-
Efficiency: The versatility of welding machines enables efficient handling of different welding tasks, streamlining the overall upholstery production process.
-
Advanced Technology: Incorporating cutting-edge technology, these machines bring innovation to upholstery welding, enabling precise and reliable welds.
The seamless integration of these welding machines into upholstery workshops sets the stage for exploring the impact of hot air tools on welding processes.
Hot Air Tools
Hot air tools have revolutionized the upholstery welding process, allowing for precise and efficient seam sealing and material bonding. Temperature control is a crucial feature of hot air tools, as it ensures the optimal welding conditions for different materials. By allowing operators to adjust the temperature according to specific requirements, these tools provide greater control over the welding process, leading to high-quality and durable seams.
Additionally, material compatibility is a key consideration when using hot air tools for upholstery welding. These tools are designed to work with various upholstery materials such as vinyl, leather, and fabric, ensuring that the welding process is effective without causing damage to the materials. This compatibility not only expands the versatility of hot air tools but also enhances their efficiency in upholstery welding.
With precise temperature control and broad material compatibility, hot air tools have become indispensable for achieving strong and seamless welds in upholstery applications. The advancements in hot air tool technology continue to elevate the standards of upholstery welding, making them an essential part of the modern upholsterer’s toolkit.
Seam Testers
Utilizing seam testers is essential for ensuring the quality and durability of upholstery welds. These tools allow operators to verify the integrity of seams and identify any potential weaknesses in the welding process.
Seam testers measure seam strength, ensuring that the welds can withstand the stresses of everyday use. They also help in evaluating the durability of the weld, ensuring that it will maintain its integrity over time.
In addition, seam testers contribute to the efficiency of the welding process by providing immediate feedback on the quality of the weld. This allows operators to make any necessary adjustments in real time, improving productivity and reducing the need for rework.
These tools also aid in maintaining a high standard of quality control. By using seam testers, operators can identify and rectify any defects in the welds before the upholstery leaves the production line. This helps to prevent customer complaints and costly returns.
Ultimately, seam testers play a crucial role in upholding the quality, durability, and efficiency of upholstery welding processes. They provide valuable information to operators, enabling them to produce high-quality welds that meet the standards of the industry.
Edgebanders
Evaluating the durability of the welds, edgebanders play a critical role in enhancing the precision and efficiency of upholstery welding processes. Edgebanders are essential tools for applying edge banding to cover the exposed sides of materials such as plywood, particleboard, or MDF, giving a seamless and refined appearance to the edges. These machines are designed to deliver precise and uniform edge banding, contributing to the overall quality of the upholstered furniture.
To further understand the significance of edgebanders, let’s look at the following comparison table:
Edgebanders Features | Description |
---|---|
Precision | Utilizes advanced technology for accurate application of edge banding, ensuring a seamless finish. |
Efficiency | Equipped with automated functions for rapid and consistent edge banding, optimizing the production process. |
Versatility | Capable of handling various edge banding materials and thicknesses, accommodating diverse upholstery requirements. |
Durability | Constructed with robust materials and components, ensuring long-term reliability and performance. |
User-Friendly | Incorporates intuitive controls and ergonomic design for ease of operation, promoting productivity and reducing errors. |
Edgebanders contribute significantly to the precision and efficiency of upholstery welding, making them indispensable tools in the manufacturing of high-quality upholstered furniture.
Welding Accessories
Welding accessories are essential for enhancing precision and efficiency in upholstery welding processes. These accessories not only ensure welding safety but also enable welders to have better control over their welding techniques.
Here are some crucial welding accessories that play a significant role in upholstery welding:
-
Protective Gear: Welding involves exposure to intense heat, harmful UV rays, and spattering sparks. Therefore, protective gear such as welding helmets, gloves, and flame-resistant clothing are indispensable for ensuring the safety of welders.
-
Precision Control Tools: Accessories like welding clamps, magnetic welding squares, and welding jigs aid in holding the upholstery pieces firmly in place, allowing for precise welding without any slippage or misalignment.
-
Welding Curtains and Screens: These accessories create a safe welding environment by containing sparks, UV light, and fumes, thereby protecting the surrounding area and individuals from potential hazards.
-
Welding Carts and Tables: These accessories provide a stable and organized workspace for welders, allowing them to maneuver their welding equipment with ease and efficiency.
Frequently Asked Questions
What Are the Best Materials to Use for Upholstery Welding?
When considering the best techniques for upholstery welding, it’s essential to prioritize durable materials. Materials such as leather, vinyl, and polyester blends are often preferred for their strength, flexibility, and heat resistance, ensuring a high-quality and long-lasting result.
Can Upholstery Welding Be Used for Outdoor Furniture?
When considering welding techniques for outdoor durability, upholstery welding can be utilized for outdoor furniture. The process ensures weather resistance and is suitable for various welding applications, making it a viable option for outdoor furniture construction.
How Do I Know if My Upholstery Welding Is Strong Enough for Heavy-Duty Use?
To ensure the strength of upholstery welding for heavy-duty use, conduct thorough strength testing and ensure durability. Assess load capacity and consider heavy duty applications. Employ appropriate techniques and materials to guarantee resilience and long-lasting performance.
Are There Any Special Safety Considerations for Using Upholstery Welding Tools?
Special safety considerations for using upholstery welding tools involve awareness of hot temperatures and the need for protective equipment. Proper ventilation, fire prevention, and adherence to safety guidelines are essential for injury prevention.
Can Upholstery Welding Be Used to Repair Leather Furniture?
Upholstery welding techniques can effectively repair leather furniture, restoring its appearance and functionality. These methods allow for precise and durable repairs, ensuring the longevity of the furniture. The use of advanced welding tools ensures high-quality results.
Conclusion
In conclusion, the innovative tools in upholstery welding offer a wide range of options for professionals in the industry. From heat guns to handheld welders, welding machines, hot air tools, seam testers, and edgebanders, there are numerous tools available to meet the needs of upholstery welding projects.
Additionally, the variety of welding accessories provides further support for achieving high-quality results. Overall, these tools are essential for achieving impeccable and flawless upholstery welding, making them a must-have for professionals in the field.
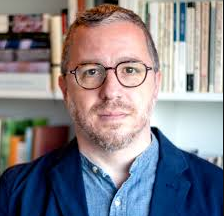
Dillon Hince, an expert in the realm of upholstery welding, brings a wealth of knowledge and experience to the craft. As the driving force behind nodpu.com, Dillon combines a passion for precision and creativity, offering unique insights into the art of seamlessly melding fabrics and materials. With a commitment to excellence, Dillon Hince is your go-to resource for innovative upholstery welding techniques, transforming ordinary pieces into extraordinary works of functional art.
This article highlights the latest innovative tools in upholstery welding, showcasing how technology is enhancing efficiency and precision in the field.Visit usTelkom University Jakarta