The Evolution of Upholstery Welding Techniques

Like the intricate stitching of a tapestry, the evolution of upholstery welding techniques weaves a story of innovation and precision.
From the traditional hand stitching methods to the integration of advanced hot air welding technology, this article explores the journey of upholstery welding.
Delving into the introduction of heat sealing methods and the advancements in ultrasonic welding, it offers a glimpse into the future trends shaping the art of upholstery welding.
Traditional Hand Stitching Techniques
An indefinite pronoun such as ‘One’ can be used to begin the first sentence of the subtopic ‘Traditional Hand Stitching Techniques’.
One of the earliest and enduring methods in upholstery work, traditional hand stitching techniques have played a crucial role in shaping the evolution of upholstery welding. Hand stitching has been an integral part of upholstery for centuries, deeply rooted in needlework traditions. Upholsterers meticulously employ hand stitching to create durable and visually appealing seams, ensuring the longevity and aesthetic appeal of upholstered furniture.
The art of hand stitching involves a skilled hand guiding a needle and thread through layers of fabric and padding, creating strong and secure connections. This meticulous process not only ensures the structural integrity of the upholstery but also allows for intricate detailing and customization. The tradition of hand stitching has been passed down through generations, preserving time-honored techniques that contribute to the artistry and craftsmanship of upholstered furniture.
As the demand for more efficient and streamlined welding techniques increased, the introduction of heat sealing methods revolutionized the upholstery industry, marking a significant shift from traditional hand stitching techniques.
Introduction of Heat Sealing Methods
The introduction of heat sealing methods marked a significant shift in the upholstery industry, revolutionizing the way seams and connections were created, and meeting the increasing demand for more efficient and streamlined welding techniques. This innovative approach brought several advancements to the field, including:
-
Seam Strength: Heat sealing methods significantly enhanced the strength and durability of seams, ensuring that upholstered products could withstand the rigors of everyday use.
-
Enhanced Efficiency: The use of heat sealing allowed for a quicker and more precise welding process, leading to improved productivity and reduced production time.
-
Versatility: Heat sealing methods offered greater versatility in welding various materials, providing a wider range of options for upholstery designs and applications.
-
Consistent Results: By employing heat sealing techniques, upholstery manufacturers achieved more consistent and reliable welds, minimizing the risk of defective products.
-
Seamless Finish: Heat sealing methods facilitated the creation of seamless finishes, enhancing the overall aesthetics of upholstered products.
The introduction of heat sealing methods not only elevated the seam strength and efficiency of upholstery welding but also paved the way for further advancements in the industry, particularly in the form of ultrasonic welding techniques.
Advancements in Ultrasonic Welding
Advancements in ultrasonic welding have further refined the efficiency and seam strength of upholstery techniques, continuing the trajectory set by the introduction of heat sealing methods. Ultrasonic bonding, a key component of this advancement, involves the use of high-frequency ultrasonic vibrations to create solid-state welds. This technique offers several advantages, including faster processing times, reduced energy consumption, and improved seam quality. Furthermore, ultrasonic welding has proven to be highly effective in joining a wide array of materials, including fabrics, plastics, and synthetic fibers, thereby enhancing material compatibility and versatility in upholstery manufacturing.
One of the most significant benefits of ultrasonic welding is its ability to produce strong, reliable seams without the need for additional adhesives or consumables, making it a cost-effective and environmentally friendly option. Additionally, the precise control and focused application of ultrasonic energy result in minimal material distortion and a clean, aesthetically pleasing finish.
As the technology continues to evolve, advancements in ultrasonic welding are expected to further elevate the efficiency and quality standards of upholstery manufacturing, solidifying its position as a preferred welding technique in the industry.
Integration of Hot Air Welding Technology
Integration of hot air welding technology further enhances the efficiency and seam quality of upholstery techniques, offering precise control and versatility in joining various materials. Hot air welding benefits include:
- Precision: Hot air welding provides precise temperature and speed control, ensuring consistent and high-quality seams.
- Versatility: It can be applied to a wide range of materials, including thermoplastics, synthetic fabrics, and vinyl, making it suitable for diverse upholstery applications.
- Seam Strength: The technique creates strong, durable seams that withstand the rigors of everyday use, enhancing the longevity of upholstered products.
- Aesthetics: Hot air welding produces aesthetically pleasing seams with minimal distortion, contributing to the overall visual appeal of upholstered items.
- Seam Waterproofing: It enables the creation of waterproof seams, enhancing the functionality of upholstery in outdoor and marine settings.
Hot air welding applications extend to automotive upholstery, furniture manufacturing, and marine upholstery, among others. The integration of this technology represents a significant advancement in the evolution of upholstery welding techniques, with its ability to improve seam quality, durability, and aesthetics.
As the industry continues to evolve, future trends in upholstery welding techniques are poised to further revolutionize the manufacturing processes.
Future Trends in Upholstery Welding Techniques
Emerging technologies are set to revolutionize upholstery welding techniques in the near future, offering enhanced efficiency and seam quality. Robotic automation is expected to play a pivotal role in transforming the upholstery welding process. Robots can be programmed to precisely control the welding parameters, resulting in consistently high-quality seams. This automation not only increases efficiency but also reduces the margin of error, leading to a more reliable and durable end product.
Additionally, the future of upholstery welding techniques will see a significant shift towards the use of sustainable materials. As environmental consciousness continues to gain momentum, manufacturers are increasingly turning to eco-friendly materials for upholstery. Welding techniques will need to adapt to accommodate these sustainable materials, ensuring that the welding process is compatible with the unique properties of these alternatives. This shift not only aligns with the broader sustainability initiatives but also presents an opportunity for innovation in welding processes to cater to the specific requirements of these materials.
Frequently Asked Questions
What Are the Environmental Impacts of Different Upholstery Welding Techniques?
The environmental impact of upholstery welding techniques varies with material compatibility. Certain techniques emit fewer pollutants, reducing environmental harm. Understanding these impacts is crucial for sustainable upholstery production and minimizing the industry’s ecological footprint.
How Have Upholstery Welding Techniques Evolved to Accommodate Different Types of Materials, Such as Leather, Vinyl, and Fabric?
Upholstery welding techniques have evolved to accommodate various materials such as leather, vinyl, and fabric. Leather welding involves specialized methods to ensure durability and aesthetics, while vinyl welding requires precise heat control and material compatibility.
Are There Any Safety Considerations or Regulations Associated With Upholstery Welding Techniques?
Safety regulations play a crucial role in upholstery welding techniques. Compliance with established standards ensures the protection of workers and the quality of finished products. Regular equipment maintenance is also essential to uphold safety and operational efficiency.
Can Upholstery Welding Techniques Be Used in Combination With Other Joining Methods, Such as Adhesives or Mechanical Fasteners?
Upholstery welding techniques can be used in combination with other joining methods like adhesives or mechanical fasteners. This offers versatility and allows for customization based on specific project requirements, enhancing welding efficiency and reducing costs.
How Do Upholstery Welding Techniques Vary in Terms of Cost and Efficiency?
Cost efficiency and material compatibility are key factors in evaluating upholstery welding techniques. Variations in cost can arise from equipment, labor, and material expenses. Efficiency depends on the welding method’s speed, quality, and energy consumption.
Conclusion
In conclusion, the evolution of upholstery welding techniques has revolutionized the industry. From traditional hand stitching to advanced heat sealing, ultrasonic welding, and hot air welding technologies, these advancements have significantly improved the efficiency, durability, and aesthetics of upholstered products. They have set a new standard for quality and precision in the field.
The future of upholstery welding techniques holds the promise of even more groundbreaking innovations. This ensures that the industry continues to push the boundaries of excellence.
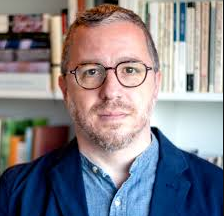
Dillon Hince, an expert in the realm of upholstery welding, brings a wealth of knowledge and experience to the craft. As the driving force behind nodpu.com, Dillon combines a passion for precision and creativity, offering unique insights into the art of seamlessly melding fabrics and materials. With a commitment to excellence, Dillon Hince is your go-to resource for innovative upholstery welding techniques, transforming ordinary pieces into extraordinary works of functional art.