The Role of Temperature in Upholstery Welding

Embarking on the delicate art of upholstery welding is akin to navigating a symphony of heat and precision. Temperature, a maestro in this symphony, dictates the harmony of materials melding seamlessly or succumbing to a discordant union.
Understanding the nuances of temperature control is paramount in achieving durable and aesthetically pleasing welds. This article delves into the pivotal role of temperature in upholstery welding, offering insights into its effects on materials, optimal ranges, and considerations for different fabrics.
Importance of Temperature Control
Why is temperature control crucial in upholstery welding?
Temperature consistency is vital in upholstery welding because it directly impacts the welding performance. Upholstery welding involves binding thermoplastic materials together using heat, making temperature control a critical factor in achieving strong and durable welds. Consistent temperature ensures that the material reaches the appropriate melting point, allowing for proper fusion and adhesion. Fluctuations in temperature can lead to inconsistent welds, weakening the bond between materials and potentially compromising the overall quality of the upholstery.
Maintaining precise temperature control also contributes to the overall efficiency of the welding process. It allows for smoother and more predictable welds, reducing the likelihood of defects or rework. Additionally, consistent temperature control helps to minimize the risk of damaging the materials being welded, ensuring that they retain their structural integrity throughout the welding process.
The significance of temperature control in upholstery welding becomes evident in its direct correlation to welding performance and the quality of the end product. The next section will delve into the effects of temperature variations on welding materials, further highlighting the critical role of temperature in upholstery welding.
Effects on Welding Materials
Temperature consistency plays a crucial role in the welding process by directly influencing the behavior and characteristics of the materials being welded. The effects on welding materials due to temperature variations are significant and can impact the overall quality of the weld. Some of the key effects include:
-
Material Strength: Inconsistent heat distribution during the welding process can lead to variations in material strength, affecting the integrity of the weld joint.
-
Residual Stress: Fluctuations in temperature can result in uneven cooling, leading to residual stress within the welded materials, potentially causing distortion or cracking.
-
Microstructural Changes: The welding process, if not conducted at the right temperature, can alter the microstructure of the materials, affecting their mechanical properties.
-
Material Durability: Improper heat distribution can compromise the durability of the welded materials, making them susceptible to premature wear or failure.
Understanding the effects of temperature on welding materials is crucial for maintaining the quality and reliability of welded components. It emphasizes the significance of precise temperature control throughout the welding process to ensure optimal heat distribution and consistent material properties.
Optimal Temperature Range
Achieving an optimal temperature range is essential for ensuring the successful execution of upholstery welding, as it directly impacts the quality and consistency of the weld. Temperature uniformity and heat distribution play crucial roles in achieving this optimal range. Upholstery welding processes require a consistent temperature across the welding area to ensure uniform melting and bonding of materials. Inconsistent temperatures can lead to weak welds and compromise the overall integrity of the upholstery.
Moreover, the optimal temperature range is also pivotal for welding speed and productivity efficiency. When the temperature is within the ideal range, the welding process can be carried out at an efficient speed, enhancing productivity. It allows for the seamless joining of materials without unnecessary delays due to temperature adjustments or cooling periods. This, in turn, contributes to overall productivity and cost-effectiveness in upholstery welding operations.
Impact on Weld Strength
The temperature significantly influences the strength of upholstery welds, directly impacting the integrity and durability of the final product. The impact on weld strength is a critical aspect to consider in the welding process. Several key factors play a role in determining how temperature affects weld strength:
-
Welding Process: Different welding processes, such as hot air, hot wedge, or radio frequency welding, respond differently to temperature variations. Each process requires precise temperature control to achieve optimal weld strength.
-
Heat Distribution: Proper heat distribution is essential for ensuring uniform weld strength. Variations in temperature across the welding area can result in weak spots or inconsistent welds, compromising the overall strength of the upholstery.
-
Material Compatibility: Temperature variations can affect the compatibility of materials being welded. Some materials may require higher temperatures to achieve strong welds, while others may degrade or weaken if exposed to excessive heat.
-
Cooling Rate: The rate at which the welded material cools after the welding process can also impact weld strength. Rapid cooling or uneven cooling can lead to internal stresses and diminished strength.
Understanding the interplay between temperature and these factors is crucial for achieving consistently strong upholstery welds.
Considerations for Different Fabrics
When considering the role of temperature in upholstery welding, it is crucial to take into account the heat sensitivity of different fabrics and the variations in welding temperatures.
The type of fabric being welded can greatly impact the welding process, as some fabrics may be more sensitive to heat than others.
Additionally, understanding the optimal welding temperature for each fabric type is essential for achieving strong and durable welds.
Fabric Heat Sensitivity
Considerations for different fabrics’ heat sensitivity play a crucial role in upholstery welding techniques. When working with various fabrics, it’s essential to understand their individual heat resistance and reaction to temperature variations. Here are key considerations for different fabrics:
-
Natural Fibers: Fabrics such as cotton, linen, and wool are generally more heat-sensitive and may require lower welding temperatures to prevent damage.
-
Synthetic Fabrics: Materials like polyester, nylon, and acrylic have higher heat resistance and can withstand higher welding temperatures without compromising their integrity.
-
Blended Fabrics: Blends of natural and synthetic fibers can exhibit varying heat sensitivity, requiring careful testing and adjustment of welding parameters.
-
Specialty Fabrics: Unique textiles like leather, suede, or vinyl demand specialized welding techniques due to their distinct heat-reactive properties.
Understanding these fabric-specific considerations is vital for achieving high-quality and durable upholstery welds.
Welding Temperature Variations
Different fabrics require careful consideration for welding temperature variations in upholstery welding techniques.
Temperature uniformity and material compatibility are crucial factors in ensuring successful welds across different fabric types.
Heat input must be adjusted based on the specific fabric’s heat sensitivity to prevent damage or discoloration.
Fabrics with different melting points and heat tolerances require precise control of welding temperatures to achieve optimal joint quality.
For example, synthetic fabrics such as nylon or polyester may require lower welding temperatures to avoid scorching or melting, while natural fabrics like cotton or wool may tolerate higher temperatures.
Understanding the heat response of each fabric is essential for maintaining the integrity of the material and achieving durable, high-quality welds in upholstery applications.
Temperature Monitoring and Adjustment
In upholstery welding, achieving the optimal welding temperature is crucial for ensuring strong and durable seams.
To achieve this, precision temperature control is essential to accommodate the different fabric types and thicknesses commonly encountered in upholstery work.
Optimal Welding Temperature
Maintaining the optimal welding temperature is crucial for ensuring the quality and durability of upholstery welds. Achieving this requires careful monitoring and adjustment of the temperature throughout the welding process. To ensure the optimal welding temperature, consider the following:
-
Heat distribution: Proper heat distribution across the welding area is essential to prevent weak spots and ensure a strong, uniform bond.
-
Welding speed: Controlling the welding speed is vital to prevent overheating or underheating, which can compromise the integrity of the weld.
-
Material compatibility: Different upholstery materials may require specific temperature ranges for optimal welding, so it’s important to consider material properties when setting the welding temperature.
-
Environmental factors: Variations in ambient temperature and humidity can affect the welding temperature, so it’s crucial to account for these factors during the welding process.
As we delve into precision temperature control, it becomes apparent that maintaining the optimal welding temperature is a multifaceted task.
Precision Temperature Control
Achieving precision temperature control in upholstery welding is essential for ensuring consistent heat distribution and avoiding weak spots in the weld. Temperature uniformity is crucial to prevent overheating or underheating, which can compromise the strength and integrity of the weld.
To achieve this, it’s important to monitor and adjust the temperature throughout the welding process. Understanding the thermal conductivity and material compatibility is also vital for maintaining precise temperature control. Different upholstery materials have varying heat sensitivity and require specific temperature ranges for successful welding.
Therefore, welders must carefully adjust the temperature according to the specific requirements of the materials being welded. By implementing precision temperature control measures, upholstery welders can ensure high-quality, durable welds that meet the stringent standards of the industry.
Frequently Asked Questions
How Does Temperature Control in Upholstery Welding Affect the Overall Appearance of the Finished Product?
Temperature control in upholstery welding significantly impacts the appearance enhancement of the finished product. It affects the welding techniques, ensuring proper material bonding and seam integrity. Precise temperature regulation is crucial for achieving high-quality, visually appealing upholstery welding results.
Are There Any Special Considerations for Temperature Control When Working With Leather Upholstery Compared to Other Fabrics?
When working with leather upholstery, special considerations must be made for temperature control during the welding process. Unlike other fabrics, leather type and its reaction to temperature impact the welding process, requiring precise control for optimal results.
Can Extreme Temperature Fluctuations During the Welding Process Cause Damage to the Welding Materials or Weaken the Weld Strength?
Extreme temperature fluctuations during the welding process can indeed damage welding materials and weaken weld strength. It’s crucial to carefully control temperature to ensure optimal welding conditions and prevent any detrimental effects on the materials and weld quality.
Are There Any Specific Temperature Monitoring Tools or Equipment That Are Recommended for Achieving Optimal Welding Results?
When striving for optimal welding results, temperature monitoring tools and welding equipment play a crucial role. Proper temperature control is essential to achieve desired appearance impact, maintain material durability, and ensure longevity, especially in leather upholstery and fabric considerations. Extreme fluctuations can lead to material damage and weaken weld strength.
How Does Temperature Control in Upholstery Welding Impact the Durability and Longevity of the Finished Product?
Temperature control in upholstery welding significantly impacts the durability and appearance of the finished product. Proper temperature regulation enhances the structural integrity of the weld, ensuring a longer-lasting and aesthetically pleasing result, particularly in leather upholstery.
Conclusion
In conclusion, the role of temperature in upholstery welding is a critical factor that cannot be overlooked. Proper temperature control is essential for achieving strong and durable welds, and different materials require different temperature ranges.
Monitoring and adjusting temperature throughout the welding process is crucial for ensuring the quality and integrity of the final product. Neglecting the importance of temperature in upholstery welding could result in weak and unreliable welds, compromising the overall quality of the upholstery work.
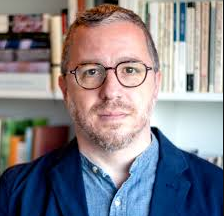
Dillon Hince, an expert in the realm of upholstery welding, brings a wealth of knowledge and experience to the craft. As the driving force behind nodpu.com, Dillon combines a passion for precision and creativity, offering unique insights into the art of seamlessly melding fabrics and materials. With a commitment to excellence, Dillon Hince is your go-to resource for innovative upholstery welding techniques, transforming ordinary pieces into extraordinary works of functional art.