Upholstery Welding for Different Types of Fabrics
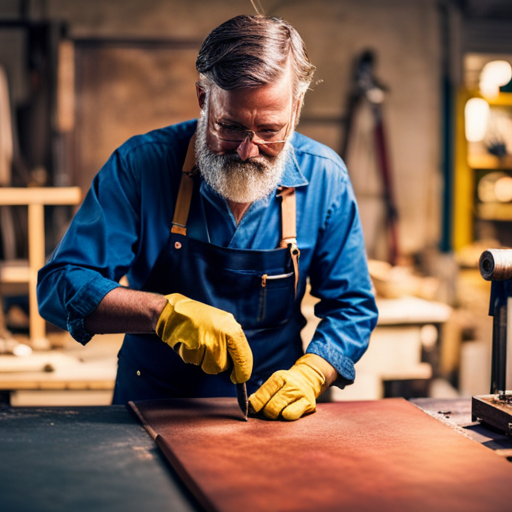
Did you know that upholstery welding can significantly extend the lifespan of furniture, with some welds lasting up to 15 years?
In our comprehensive guide on ‘Upholstery Welding for Different Types of Fabrics,’ we explore specialized techniques for leather, vinyl, woven, synthetic, natural fiber, and specialty fabrics.
Whether you’re a professional welder or a DIY enthusiast, this article will provide valuable insights into the best practices for welding various upholstery fabrics.
Leather Upholstery Welding Techniques
One of the key techniques for welding leather upholstery is to carefully select the appropriate temperature and pressure settings for the specific type of leather being worked with. Leather welding presents unique challenges due to the varying thickness and density of different types of leather. It is crucial to use specialized leather welding equipment designed to handle the specific demands of working with leather. The equipment should offer precise control over temperature and pressure to ensure a strong and durable weld without damaging the leather.
When welding leather, maintaining the right temperature is essential to avoid scorching or burning the material. Additionally, the pressure applied during the welding process must be carefully regulated to achieve a seamless bond without causing any distortion to the leather. Leather welding challenges often stem from the need to balance these factors while working with a material that is sensitive to heat and pressure.
Transitioning to the subsequent section about ‘vinyl upholstery welding methods’, it is important to note that while leather presents its own set of challenges, vinyl upholstery welding involves a different set of considerations and techniques.
Vinyl Upholstery Welding Methods
Vinyl upholstery welding methods involve specific techniques for heat sealing vinyl and welding delicate vinyl materials. These methods are essential for creating strong and seamless seams in vinyl upholstery, ensuring durability and a professional finish.
Understanding the nuances of vinyl welding is crucial for achieving high-quality results in upholstery projects.
Vinyl Welding Techniques
When working with vinyl upholstery, it is essential to employ precise welding techniques to ensure a durable and seamless finish. Vinyl welding tools, such as hot air guns and handheld welders, are commonly used to fuse heat resistant vinyl together. These tools allow for precise control over temperature and airflow, ensuring that the vinyl is welded together without causing damage or warping.
Additionally, heat resistant vinyl is crucial for achieving strong and long-lasting welds. By using the appropriate welding tools and materials, upholsterers can create seamless seams and strong bonds in vinyl upholstery, ensuring high-quality and durable finished products.
Transitioning into the subsequent section about ‘heat sealing vinyl’, understanding the intricacies of vinyl welding techniques is fundamental for mastering the art of upholstery.
Heat Sealing Vinyl
The heat sealing of vinyl upholstery involves precise welding methods to ensure a durable and seamless finish. Vinyl welding temperature and the heat sealing process are crucial elements in achieving a high-quality weld. Proper temperature control and process execution are essential to prevent damage to the material and ensure a strong bond. The table below provides an overview of recommended vinyl welding temperatures for common types of vinyl, as well as key considerations for the heat sealing process.
Type of Vinyl | Recommended Welding Temperature | Heat Sealing Process |
---|---|---|
PVC Vinyl | 250-300°F | Use a hot wedge welder for best results |
TPO Vinyl | 300-350°F | Ensure consistent pressure during welding |
PU Vinyl | 200-250°F | Use a silicone-coated roller for smooth seams |
Marine Vinyl | 275-325°F | Allow sufficient cooling time after welding |
Understanding the specific requirements for each type of vinyl and following proper heat sealing techniques are essential for achieving optimal results.
Next, let’s delve into the intricacies of welding delicate vinyl.
Welding Delicate Vinyl
Delicate vinyl upholstery demands meticulous welding methods to ensure a refined and enduring finish, requiring precise temperature control and specialized techniques. When welding delicate vinyl, it is crucial to adhere to specific guidelines to achieve optimal results. Here are essential considerations for welding delicate vinyl:
-
Temperature Control:
Utilize precise temperature settings to prevent damage to the delicate vinyl and ensure a strong weld without compromising the material’s integrity. -
Specialized Welding Tools:
Use specialized welding tools designed for delicate vinyl to maintain seam strength and prevent distortion of the material. -
Careful Pressure Application:
Apply consistent and careful pressure during the welding process to create seamless, durable seams without causing damage to the delicate vinyl. -
Testing and Quality Assurance:
Conduct thorough testing and quality assurance checks to guarantee the integrity and longevity of the welded delicate vinyl upholstery.
Woven Fabric Welding Considerations
Upholstery welding for different types of fabrics requires specific considerations when working with woven fabrics to ensure a strong and durable bond. When it comes to woven fabric bonding, heat settings play a crucial role. The heat settings need to be carefully adjusted to accommodate the specific type of woven fabric being welded.
Different woven fabrics have varying heat resistance, and improper heat settings can lead to weak seam strength or even damage the fabric. It’s important to conduct thorough testing on scrap fabric pieces to determine the optimal heat settings for each type of woven fabric before proceeding with the actual welding process.
Additionally, the direction of the weave and the density of the fabric may also impact the welding process. Understanding these factors and making necessary adjustments to the welding technique can ensure that the seams on woven fabric upholstery are strong and durable.
Proper heat settings and attention to fabric welding techniques are essential for achieving high seam strength and ensuring the longevity of the upholstered piece.
Synthetic Fabric Welding Tips
For synthetic fabric welding, precise heat settings are crucial for achieving strong and durable seams. When working with synthetic fabrics such as those used in automotive upholstery, it’s essential to follow specific guidelines to ensure successful welding.
Here are some tips for welding synthetic fabrics:
-
Heat Settings: Adjust the welding equipment to the appropriate heat setting for the specific type of synthetic fabric being used. Different synthetic fibers may require different heat levels for effective welding.
-
Pressure Control: Maintain consistent pressure during the welding process to ensure proper fusion of the synthetic fibers. This helps in creating a seamless and durable bond.
-
Plastic Welding Techniques: Employ plastic welding techniques suitable for synthetic fabrics, such as hot gas welding or speed welding. These techniques are commonly used in industrial applications for welding synthetic materials.
-
Quality Assurance: After welding, conduct thorough quality checks to ensure the strength and integrity of the seams. This is especially important in automotive upholstery to guarantee the durability of the welded synthetic fabric.
Following these tips will help achieve high-quality synthetic fabric welding, ensuring the longevity and reliability of the welded seams, particularly in industrial applications and automotive upholstery.
Natural Fiber Fabric Welding Insights
As we shift our focus to natural fiber fabric welding, it’s important to consider the unique characteristics of materials like cotton and silk.
Understanding the specific welding techniques for cotton and the delicate nature of silk fabric will be essential for achieving durable and visually appealing upholstery.
Let’s explore the nuanced insights and considerations for welding natural fiber fabrics to ensure successful outcomes in upholstery projects.
Cotton Welding Techniques
Welding cotton fabric requires specialized techniques to ensure durability and strength in the seams. When working with cotton fabric, it’s essential to consider its heat resistance and the impact of heat on the fabric’s integrity.
To ensure strong and durable seams when welding cotton fabric, the following techniques are crucial:
-
Appropriate Heat Settings: Adjust the welding machine to the precise heat settings suitable for cotton fabric to prevent scorching or weakening of the material.
-
Use of Reinforcement Strips: Incorporate reinforcement strips along the seams to enhance strength and prevent fraying, especially in high-stress areas.
-
Careful Stitch Placement: Ensure proper spacing and depth of stitches to maintain the fabric’s integrity while creating sturdy seams.
-
Testing and Evaluation: Conduct thorough testing and evaluation of the welded seams to guarantee optimal seam strength and overall fabric integrity.
Silk Fabric Considerations
Silk fabric welding demands meticulous attention to the fabric’s delicate nature and heat sensitivity, requiring precise heat management and specialized techniques for optimal seam strength. When heat sealing silk fabric, it’s crucial to use lower temperatures and shorter welding times to prevent damage to the delicate fibers. Additionally, the use of a Teflon-coated welding foot helps to minimize direct heat contact with the silk fabric, reducing the risk of scorching or discoloration. It’s important to note that silk fabric has a lower melting point compared to synthetic fabrics, necessitating delicate welding techniques. The table below outlines key considerations for welding silk fabric:
Consideration | Description |
---|---|
Temperature | Lower temperatures to prevent damage |
Welding Time | Shorter welding times for delicate fibers |
Welding Foot | Teflon-coated foot to minimize direct heat contact |
Specialty Fabrics Welding Approaches
When working with specialty fabrics, it is important to employ specific welding approaches tailored to the unique characteristics of each material. Different types of specialty fabrics require different welding techniques to ensure a strong and durable bond.
Here are some specialized welding approaches for various specialty fabrics:
-
Heat Sealing Leather: Leather welding requires precision and control of temperature to avoid scorching or damaging the material. High-frequency welding or hot air welding can be used to seal and bond leather pieces effectively.
-
Delicate Silk Welding: Silk is a delicate fabric that requires a gentle welding approach. Ultrasonic welding is a suitable method for joining silk fabrics as it uses high-frequency ultrasonic acoustic vibrations to create a strong bond without causing damage to the delicate fibers.
-
Waterproof Fabric Welding: Welding waterproof fabrics, such as vinyl or polyester, requires the use of hot wedge welding or radio frequency (RF) welding to create a watertight seal without compromising the fabric’s integrity.
-
Fire-Resistant Fabric Welding: Fabrics with fire-resistant properties, like Nomex or Kevlar, can be effectively welded using hot air or hot wedge welding techniques designed to maintain the fabric’s fire-resistant qualities while creating a strong seam.
Frequently Asked Questions
Can Upholstery Welding Be Used on Delicate Fabrics Such as Silk or Lace?
Upholstery welding can be challenging on delicate fabrics like silk or lace due to their susceptibility to heat damage. Environmental concerns, regulations, and safety precautions must be considered. Alternative fabric welding methods may be more suitable for durability and seam repair.
Are There Any Environmental Concerns or Regulations to Consider When Using Upholstery Welding Techniques?
When considering upholstery welding techniques, it’s essential to prioritize environmental regulations and safety precautions. Upholstery welding processes may produce emissions and require proper ventilation and waste disposal methods to comply with environmental standards and ensure workplace safety.
How Do Different Types of Fabric Welding Methods Impact the Overall Durability and Lifespan of the Upholstery?
Different types of fabric welding methods can impact the overall durability and lifespan of upholstery. Understanding fabric compatibility and the impact on longevity is crucial in ensuring the quality and longevity of upholstered furniture.
Are There Any Specific Safety Precautions to Be Aware of When Using Upholstery Welding on Certain Fabrics?
Understanding the intricacies of upholstery welding on various fabrics is crucial for ensuring safety. It’s imperative to consider fabric compatibility, fabric strength, and environmental impact when implementing safety precautions. Upholstery welding demands meticulous attention to detail and adherence to safety protocols.
Can Upholstery Welding Be Used to Repair or Reinforce Seams and Stitching on Upholstery Fabric?
Repairing seams and reinforcing stitching on upholstery fabric can be effectively achieved through upholstery welding. This technique provides a durable and seamless bond, ensuring the longevity and structural integrity of the upholstery.
Conclusion
In conclusion, upholstery welding techniques vary depending on the type of fabric being used. Whether it’s leather, vinyl, woven fabric, synthetic fabric, natural fiber, or specialty fabrics, there are specific methods and considerations to keep in mind.
By understanding the unique characteristics of each fabric type and applying the appropriate welding approaches, quality and durable upholstery can be achieved.
Through a harmonious blend of technique and material, upholstery welding can produce seamless and visually appealing results.
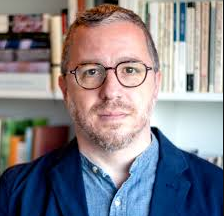
Dillon Hince, an expert in the realm of upholstery welding, brings a wealth of knowledge and experience to the craft. As the driving force behind nodpu.com, Dillon combines a passion for precision and creativity, offering unique insights into the art of seamlessly melding fabrics and materials. With a commitment to excellence, Dillon Hince is your go-to resource for innovative upholstery welding techniques, transforming ordinary pieces into extraordinary works of functional art.