Adhesive Choices in Upholstery Welding
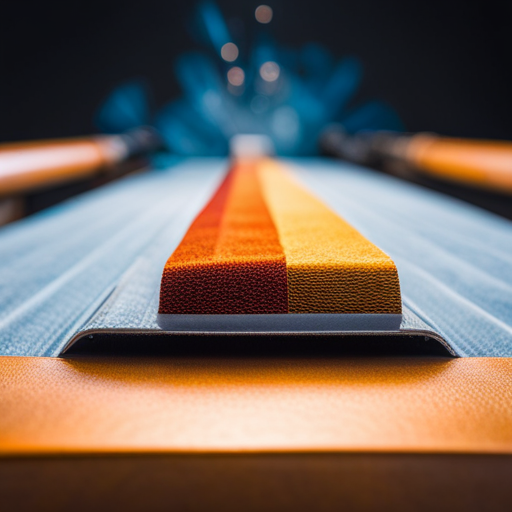
As the art of upholstery welding continues to evolve, the selection of adhesive plays a vital role in achieving durable and aesthetically pleasing results. From traditional options to advanced formulations, the adhesive choices available can greatly impact the overall quality of the weld.
Understanding the factors that influence adhesive selection, application techniques, and compatibility with upholstery materials is essential for achieving optimal bond strength and durability.
This article delves into the critical considerations for choosing the right adhesive in upholstery welding.
Types of Adhesive Options
When selecting adhesive options for upholstery welding, it is essential to consider the specific materials being joined and the intended application. Adhesive bonding plays a crucial role in ensuring the longevity and durability of the upholstery weld. Different materials, such as leather, fabric, vinyl, and foam, require specific adhesives to ensure a strong and lasting bond. Material compatibility is a key factor to consider when choosing the right adhesive for upholstery welding. Adhesives that are compatible with a wide range of materials offer versatility and reliability in various upholstery applications.
In upholstery welding, the adhesive must be able to withstand the stresses and strains to which the materials will be subjected. Factors such as flexibility, heat resistance, and moisture resistance are essential considerations when selecting the appropriate adhesive. Additionally, the intended application, whether it be automotive, furniture, or marine upholstery, will dictate the specific requirements for the adhesive. Understanding the diverse adhesive options available and their suitability for different materials and applications is crucial for achieving high-quality and durable upholstery welds.
Factors Affecting Adhesive Selection
In selecting adhesives for upholstery welding, it is essential to consider the adhesive properties and performance. These aspects play a crucial role in determining the most suitable adhesive for a particular application. Understanding these factors is essential for making informed decisions when selecting adhesives for upholstery welding.
Additionally, environmental factors should be taken into account. Adhesives that are environmentally friendly and have low VOC emissions are preferable as they reduce the impact on the environment and improve air quality. Considering the environmental impact of adhesives is important for sustainable upholstery welding practices.
Furthermore, material factors should also be considered when selecting adhesives for upholstery welding. Different materials require different types of adhesives for optimal bonding. Factors such as the type of fabric, foam, or leather being used should be taken into account to ensure proper adhesion and long-lasting results.
Adhesive Properties and Performance
One crucial factor in selecting adhesives for upholstery welding is understanding the properties and performance characteristics that impact their suitability for specific applications. When considering adhesive bonding for upholstery welding, several factors come into play, including material compatibility, surface preparation, and bond strength testing.
The following are key points to consider:
-
Material Compatibility: Ensuring the adhesive is compatible with the materials being bonded is essential for a strong and durable weld.
-
Surface Preparation: Proper surface preparation, such as cleaning and roughening, is crucial to promote adhesion and enhance bond strength.
-
Bond Strength Testing: Conducting tests to assess the strength and durability of the adhesive bond under anticipated usage conditions is vital.
-
Environmental Considerations: Understanding the impact of environmental factors, such as temperature and humidity, on adhesive performance.
-
Application Method: Selecting the appropriate application method based on the specific requirements of the upholstery welding project.
These factors play a significant role in determining the effectiveness of adhesives in upholstery welding applications.
Environmental and Material Factors
The selection of adhesives for upholstery welding is intricately influenced by environmental and material factors that significantly affect their suitability and performance in specific applications.
Environmental regulations play a crucial role in determining the type of adhesive that can be used in upholstery welding. Adhesives must comply with environmental standards to minimize their impact on the environment during manufacturing, application, and disposal.
Material compatibility is another vital consideration. Adhesives need to be compatible with a wide range of upholstery materials to ensure strong and durable bonds. Factors such as the porosity, flexibility, and chemical composition of the materials must be taken into account when selecting adhesives for upholstery welding.
Understanding these environmental and material factors is essential for making informed decisions in adhesive selection for upholstery welding.
Moving forward, it is critical to delve into considerations for upholstery material.
Considerations for Upholstery Material
Considerations for upholstery material should include factors such as durability, texture, and colorfastness. When selecting upholstery fabric, it is crucial to consider the maintenance tips to ensure longevity and aesthetics.
Here are some important factors to consider:
-
Durability: Choose upholstery fabric that can withstand the expected level of wear and tear. Factors such as the fabric’s double rub count and thread count can indicate its durability.
-
Texture: Consider the tactile feel of the fabric, as it contributes to the overall comfort and appearance of the furniture. Textures range from smooth and sleek to rough and nubby, offering different aesthetic and sensory experiences.
-
Colorfastness: Upholstery fabric should be resistant to fading, especially if it will be exposed to sunlight. Look for fabrics that are labeled as colorfast or solution-dyed to ensure long-lasting vibrancy.
-
Maintenance: Consider the ease of cleaning and maintaining the upholstery fabric. Some fabrics may require special cleaning methods or professional care, while others are more forgiving and easy to spot-clean.
-
Style and Design: Upholstery fabric should complement the overall design scheme of the space. Consider the color, pattern, and scale of the fabric to ensure it aligns with the desired aesthetic.
Application Techniques and Best Practices
When selecting adhesive choices in upholstery welding, it is essential to consider the specific application techniques and best practices for ensuring a durable and visually appealing outcome. Proper application techniques are crucial to achieving a strong and lasting bond between the upholstery materials. It is important to follow the manufacturer’s guidelines for the application of the adhesive, including the appropriate temperature, pressure, and curing time.
Additionally, surface preparation is a critical step in ensuring the effectiveness of the adhesive. The surfaces to be bonded must be clean, dry, and free from any contaminants that could hinder adhesion. Proper surface preparation may involve cleaning, sanding, or using a primer to promote better adhesion.
Adhering to best practices in application techniques and surface preparation will ultimately result in a high-quality and long-lasting upholstered product.
Considering the importance of application techniques and surface preparation, the next crucial aspect to address is the compatibility of the selected adhesive with welding equipment.
Compatibility With Welding Equipment
Compatibility of the selected adhesive with welding equipment is crucial to ensure a seamless and efficient upholstery welding process, especially when adhering to best practices in application techniques and surface preparation. Adhesive bonding and welding equipment work hand in hand to achieve strong and durable welds.
Here are five key considerations for ensuring compatibility with welding equipment:
-
Temperature Range: The adhesive should be compatible with the operating temperature range of the welding equipment to prevent premature curing or degradation during the welding process.
-
Chemical Compatibility: It is essential to ensure that the adhesive does not react adversely with any chemicals or cleaning agents used to maintain the welding equipment, as this could affect the adhesive’s performance.
-
Nozzle Compatibility: The adhesive should be compatible with the welding equipment’s nozzles and applicators to ensure smooth and consistent application without clogging or uneven dispensing.
-
Curing Time: The adhesive’s curing time should align with the welding process to allow for proper bonding and integration with the welded materials.
-
Equipment Maintenance: Regular maintenance of welding equipment is vital to ensure that it does not contaminate or interfere with the adhesive bonding process. Proper equipment maintenance can prevent issues such as nozzle blockages, uneven heat distribution, or adhesive contamination, all of which can impact the overall welding process.
Evaluating Bond Strength and Durability
In evaluating bond strength and durability in upholstery welding, it is crucial to consider the importance of achieving a strong and long-lasting bond between materials.
Factors such as environmental conditions, stress, and material compatibility play a significant role in determining the durability of the adhesive bond.
Understanding these points is essential for selecting the most suitable adhesive for upholstery welding applications.
Bond Strength Importance
Assessing the bond strength and durability of adhesives is essential in determining their suitability for upholstery welding applications. Bond strength directly affects the longevity and performance of upholstery welds, making it a crucial factor in adhesive selection.
Evaluating bond strength involves considering several key aspects:
-
Material Compatibility: Ensuring that the adhesive is compatible with the upholstery material is vital for achieving a strong bond.
-
Environmental Factors: Assessing how well the adhesive withstands environmental conditions such as temperature fluctuations and humidity is essential for durability.
-
Long-Term Performance: Understanding how the bond strength holds up over time is critical for evaluating the adhesive’s long-term effectiveness.
-
Stress Resistance: Determining the adhesive’s ability to withstand stress and strain is crucial for ensuring the weld’s durability.
-
Testing Methods: Utilizing standardized testing methods to accurately measure bond strength and durability is imperative for reliable results.
Factors Affecting Durability
The evaluation of bond strength and durability in upholstery adhesive choices is crucial for ensuring longevity and performance in welding applications. Factors such as material compatibility and adhesion performance play a significant role in determining the durability of the bond. Evaluating these factors helps in selecting the most suitable adhesive for the specific upholstery material and welding requirements. The table below outlines key factors affecting the durability of upholstery adhesive bonds.
Factors | Description |
---|---|
Material Compatibility | Compatibility of the adhesive with upholstery material is essential for long-term bonding. |
Adhesion Performance | The ability of the adhesive to create a strong and lasting bond with the upholstery material. |
Environmental Factors | Consideration of environmental conditions like temperature and humidity that may affect bond durability. |
Application Method | The method of application can impact the overall strength and longevity of the bond. |
Maintenance Practices | Proper maintenance and care can influence the longevity of the adhesive bond. |
Frequently Asked Questions
Can Adhesives Be Used to Repair Upholstery Welding on Outdoor Furniture?
Yes, adhesives can be used to repair upholstery welding on outdoor furniture. When selecting an adhesive, it is essential to consider adhesive durability and outdoor exposure to ensure the repair withstands harsh weather conditions and maintains longevity.
Are There Any Environmental or Safety Considerations When Using Adhesives in Upholstery Welding?
When using adhesives in upholstery welding, it’s essential to consider the environmental impact and safety precautions. Environmental factors include the adhesive’s chemical composition, while safety considerations involve proper ventilation and protective equipment for handling adhesives.
What Are the Best Practices for Removing Old Adhesive Before Applying a New One in Upholstery Welding?
When considering surface preparation in upholstery welding, it’s crucial to prioritize the removal of old adhesive residue. Utilizing best practices for this step ensures a clean, smooth surface for the application of new adhesives, promoting optimal results.
Are There Any Special Considerations for Using Adhesives on Leather Upholstery Compared to Other Materials?
When considering leather compatibility, special bonding techniques must be employed for adhesives on leather upholstery compared to other materials. The unique nature of leather requires careful selection and application of adhesives for optimal results.
Can Adhesives Be Used to Repair Upholstery Welding on High-Temperature Applications, Such as Automotive Interiors?
When considering heat resistance in adhesives for automotive interiors, it’s crucial to select products designed for high-temperature applications. When repairing upholstery welding in such settings, opt for specialized heat-resistant adhesives to ensure durability and performance.
Conclusion
In conclusion, the selection of adhesive for upholstery welding is a critical decision influenced by various factors. These factors include material type, application technique, and compatibility with welding equipment. It is essential to evaluate bond strength and durability to ensure long-lasting and reliable results.
By making informed adhesive choices, upholsterers can create high-quality and durable products. This, in turn, provides a sense of pride and satisfaction in their work.
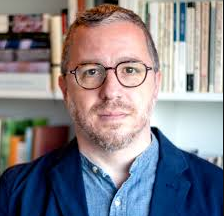
Dillon Hince, an expert in the realm of upholstery welding, brings a wealth of knowledge and experience to the craft. As the driving force behind nodpu.com, Dillon combines a passion for precision and creativity, offering unique insights into the art of seamlessly melding fabrics and materials. With a commitment to excellence, Dillon Hince is your go-to resource for innovative upholstery welding techniques, transforming ordinary pieces into extraordinary works of functional art.