Comparing Different Welding Techniques for Various Materials
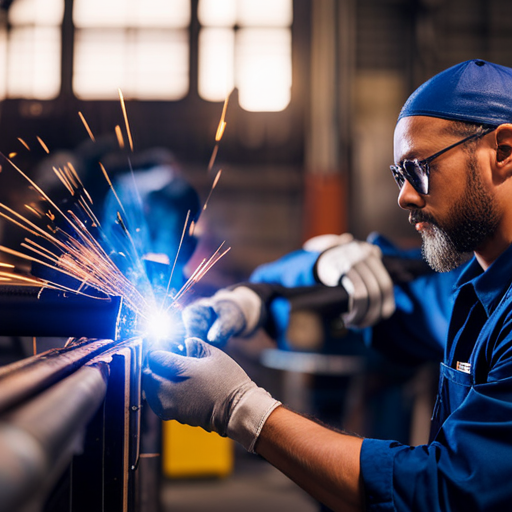
Amidst the diverse array of welding techniques available, the choice of method is critical in ensuring optimal results when working with different materials.
This article meticulously examines the advantages, limitations, and best practices of MIG, TIG, and Stick welding across steel, aluminum, and titanium.
By delving into the intricacies of each process, readers will gain a comprehensive understanding of the most effective welding techniques for various materials.
Welding Techniques for Steel
Frequently, welding professionals employ a variety of techniques to join steel, each method tailored to the specific properties and requirements of the material. The welding process for steel involves the application of heat to melt and fuse the edges of the metal being joined. Heat input is a critical factor in the welding process for steel, as it affects the microstructure, mechanical properties, and overall quality of the weld. Various welding techniques, such as shielded metal arc welding (SMAW), gas metal arc welding (GMAW), and flux-cored arc welding (FCAW), are commonly used for steel due to their ability to provide the necessary heat input while ensuring the integrity of the material.
SMAW, also known as stick welding, is a versatile and portable welding process suitable for welding steel. GMAW, commonly referred to as MIG welding, utilizes a continuous solid wire electrode and a shielding gas to protect the weld pool. FCAW, on the other hand, is well-suited for welding thick steel plates and can deliver high heat input, making it suitable for various steel welding applications.
Understanding the specific heat input requirements and selecting the most suitable welding process is crucial to achieving strong and durable welds in steel fabrication.
Welding Techniques for Aluminum
When considering welding techniques for aluminum, TIG welding is often preferred due to its ability to provide precise control over the welding process, producing clean and aesthetically pleasing welds.
However, MIG welding also has its considerations, requiring the use of specialized equipment and gas mixtures to ensure proper penetration and weld quality.
Additionally, aluminum welding presents unique challenges such as its high thermal conductivity and susceptibility to distortion, making it essential to employ proper techniques and equipment to achieve successful welds.
TIG Welding for Aluminum
TIG welding is a highly effective method for joining aluminum, known for its precise and clean welds. When TIG welding aluminum, there are several benefits to consider, such as the ability to weld thin materials, high-quality welds with no spatter, and the capability to weld in all positions. However, welding aluminum requires certain tips to ensure optimal results. It is crucial to clean the aluminum thoroughly to remove any oxide layer before welding. Additionally, using the correct filler rod is essential for achieving strong and crack-free welds. Below is a table summarizing the key tips for TIG welding aluminum.
Aluminum Welding Tips |
---|
Clean the aluminum surface thoroughly |
Use the correct filler rod for aluminum |
Maintain a consistent travel speed |
Use the right shielding gas, typically pure argon |
Adjust the TIG welding machine settings for aluminum |
This table serves as a quick reference for welders to achieve successful TIG welding results with aluminum.
MIG Welding Considerations
MIG welding offers distinct advantages when welding aluminum due to its higher deposition rates and increased efficiency compared to TIG welding. The higher deposition rates of MIG welding result in faster welding speeds, making it a more efficient process for aluminum.
MIG welding equipment requirements for aluminum include a constant voltage power source, a wire feeder, a welding gun, and a shielding gas system. The wire feeder is crucial for accurately and continuously feeding the aluminum wire into the welding arc. Additionally, a shielding gas system with 100% argon or a helium-argon mixture is used to protect the weld pool from atmospheric contamination.
Proper selection and setup of MIG welding equipment are essential for achieving high-quality aluminum welds with optimal efficiency.
Aluminum Welding Challenges
Aluminum welding presents unique challenges that require careful consideration of the welding techniques and equipment needed to achieve high-quality results and optimal efficiency.
When it comes to welding aluminum, several key factors have to be taken into account:
-
Aluminum Welding Processes: The selection of appropriate welding processes such as TIG (Tungsten Inert Gas) welding or MIG (Metal Inert Gas) welding is crucial due to the material’s high thermal conductivity and low melting point.
-
Filler Metal Selection: Choosing the right filler metal is essential to ensure proper joint strength and integrity, considering the differences in thermal expansion between aluminum and other metals.
-
Shielding Gas: Proper selection of shielding gas is vital to prevent porosity and ensure a clean weld, given aluminum’s susceptibility to atmospheric contamination.
-
Equipment Considerations: Specialized welding equipment and wire feed systems are often necessary for aluminum welding due to the material’s unique properties.
Careful attention to these factors is essential for successful aluminum welding.
Welding Techniques for Titanium
When welding titanium, it is important to carefully consider the specific properties of the metal in order to select the most suitable welding technique. Titanium is known for its high strength, corrosion resistance, and low thermal conductivity, which pose unique challenges during the welding process. The selection of welding equipment and proper gas shielding are crucial factors to ensure a successful titanium welding operation.
Welding Technique | Advantages | Disadvantages |
---|---|---|
Tungsten Inert Gas (TIG) | Precise control, high-quality welds | Slower process, sensitive to contaminants |
Plasma Arc Welding | High welding speeds, deep penetration | Specialized equipment required, high initial cost |
Electron Beam Welding | High welding speed, minimal distortion | Vacuum chamber needed, limited joint access |
Laser Beam Welding | Narrow heat-affected zone, high energy density | High sensitivity to joint fit-up, reflective materials are challenging |
Each technique has its own set of advantages and disadvantages. TIG welding is commonly used for its precise control, while plasma arc welding offers high speeds. Electron beam welding is suitable for high-speed, minimal distortion welding, and laser beam welding is known for its narrow heat-affected zone. Understanding the specific requirements of the titanium application is essential in determining the most appropriate welding technique.
Advantages and Limitations of MIG Welding
One of the widely used welding techniques in various industries, MIG welding offers distinct advantages and limitations that are essential to understand for effective application.
Advantages:
- High Efficiency: MIG welding is known for its high welding speed, making it a productive choice for large-scale projects.
- Versatile Application: It can be used on a wide range of materials including stainless steel, aluminum, and mild steel, providing flexibility in welding various components.
- Minimal Post-Weld Cleanup: MIG welding produces fewer slag and flux, resulting in a cleaner weld that requires less post-welding cleaning.
- Reduced Weld Defects: The precise control over the welding parameters in MIG welding leads to fewer weld defects, enhancing the overall quality of the weld.
Limitations:
- Spatter: MIG welding can produce spatter, which are droplets of molten metal that can cause weld defects and require additional cleanup.
- Equipment Complexity: The equipment for MIG welding can be complex, requiring proper setup and maintenance for optimal performance.
- Wind Sensitivity: MIG welding is sensitive to wind, making it less suitable for outdoor applications without appropriate shielding.
- Welding Position: MIG welding is less suitable for welding in vertical or overhead positions, limiting its application in certain scenarios.
Advantages and Limitations of TIG Welding
When it comes to TIG welding, its advantage lies in its ability to produce precise and clean welds, making it suitable for applications where aesthetics and quality are crucial.
However, TIG welding can be challenging in tight spaces due to the nature of the process, which requires a significant amount of space to maneuver the torch and filler rod.
These factors should be considered when evaluating the suitability of TIG welding for specific welding projects.
Precision and Clean Welds
The precision and cleanliness of welds achieved through TIG welding make it a highly desirable technique for joining various materials. This method offers several advantages, including:
- Precise control over the welding arc, resulting in clean and accurate welds.
- Suitable for a wide range of materials, including stainless steel, aluminum, and exotic alloys.
- Minimal spatter and fumes, leading to a cleaner work environment.
- High-quality, aesthetically pleasing welds, making it ideal for applications where appearance is important.
However, TIG welding also has limitations, such as slower welding speed and higher skill requirements. Moreover, material thickness can impact the welding process, and it may not be suitable for thicker or heavier materials. Understanding the advantages and limitations of TIG welding is crucial for determining its suitability for specific welding applications.
Difficult in Tight Spaces
Transitioning from the discussion on precision and cleanliness in welding, it is important to acknowledge the specific challenge posed by tight spaces when considering the advantages and limitations of TIG welding. Welding in confined spaces requires careful safety considerations and equipment adaptations. The table below outlines the key considerations for TIG welding in tight spaces.
Consideration | Description | Solution |
---|---|---|
Limited Access | Difficulty in reaching the weld area due to space constraints | Use of specialized TIG torches and accessories |
Heat Management | Challenges in heat dissipation and control in enclosed spaces | Utilization of heat sinks and cooling devices |
Fume Extraction | Limited ventilation in tight spaces leading to fume buildup | Integration of portable or built-in fume extractors |
As we delve into the advantages and limitations of stick welding, it is essential to understand the nuances of working in confined spaces.
Advantages and Limitations of Stick Welding
One key advantage of stick welding lies in its versatility for welding various materials with different thicknesses. This makes it a suitable choice for outdoor applications, where other welding techniques may not be as effective. Additionally, stick welding is particularly well-suited for vertical welding, making it ideal for projects that require welding on upright surfaces.
Some of the key advantages and limitations of stick welding include:
- Versatility in welding various materials and thicknesses
- Suitable for outdoor applications
- Ideal for vertical welding
- Minimal equipment setup required
Despite these advantages, stick welding does have limitations. It tends to produce more spatter compared to other welding techniques, which can lead to a messier work environment. Additionally, the process may require frequent rod changes, resulting in interruptions to the welding process.
While stick welding is a versatile and effective welding technique, it is essential to consider its limitations when determining its suitability for a specific welding project.
Frequently Asked Questions
What Are the Environmental Considerations and Impact of Each Welding Technique?
When evaluating welding techniques, it is crucial to consider their environmental impact and safety considerations. Each technique has distinct effects on air quality, energy consumption, and material emissions, requiring careful assessment for sustainable and safe practices.
Are There Any Specific Safety Considerations or Precautions That Need to Be Taken When Using Each Welding Technique?
When using different welding techniques, safety measures are paramount. Protective gear and proper training are essential for minimizing risks. Each technique has specific safety precautions. Certification requirements and environmental impact also play a significant role.
How Do the Costs of Each Welding Technique Compare in Terms of Equipment, Materials, and Labor?
In analyzing the cost comparison and efficiency analysis of welding techniques, it is crucial to consider equipment, materials, and labor expenses. Accurate evaluation of these factors is essential to determine the most cost-effective method for a specific application.
Can These Welding Techniques Be Used for Specialized Applications, Such as in the Aerospace or Automotive Industries?
Material compatibility, efficiency, precision, and durability are critical in specialized applications like aerospace or automotive industries. Welding techniques must meet stringent requirements for joining dissimilar materials, ensuring structural integrity, and maintaining performance under extreme conditions.
Are There Any Specific Training or Certification Requirements for Welders Using Each Welding Technique?
Welding techniques demand specialized training and certification standards. Welders must undergo comprehensive training to master each technique, ensuring expertise in handling various materials. Certifications validate their skill and understanding, crucial for safety and quality in industrial applications.
Conclusion
In conclusion, the comparison of welding techniques for different materials provides valuable insights into the advantages and limitations of each method.
Like different instruments in an orchestra, each welding technique plays a unique role in achieving strong and durable welds.
Understanding the specific requirements for steel, aluminum, and titanium welding is crucial for ensuring the quality and integrity of the final product.
It is through this understanding that welders can effectively choose the most suitable technique for the job at hand.
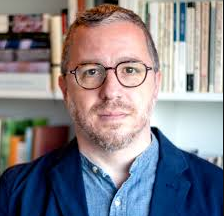
Dillon Hince, an expert in the realm of upholstery welding, brings a wealth of knowledge and experience to the craft. As the driving force behind nodpu.com, Dillon combines a passion for precision and creativity, offering unique insights into the art of seamlessly melding fabrics and materials. With a commitment to excellence, Dillon Hince is your go-to resource for innovative upholstery welding techniques, transforming ordinary pieces into extraordinary works of functional art.