Cost-Benefit Analysis of Upholstery Welding Equipment
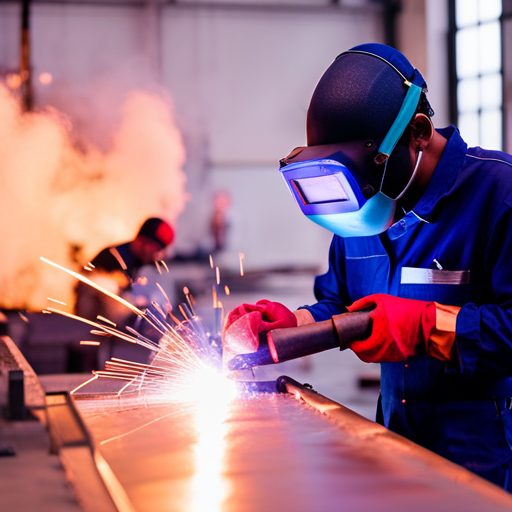
Discover the strategic financial assessment of upholstery welding equipment in this insightful analysis.
Uncover the meticulous evaluation of upfront costs against long-term financial benefits and productivity enhancements.
Delve into the comprehensive examination of the overall return on investment to make informed decisions about integrating this equipment into your operations.
Upholstery Welding Equipment: An Overview
The upholstery welding equipment’s overview provides insight into the necessary tools and techniques required for efficient and high-quality upholstery welding. When considering the types of materials used in upholstery, it is essential to select welding equipment that can accommodate a wide range of materials, including leather, vinyl, and fabric. Different welding techniques such as hot air, hot wedge, and radio frequency welding may be required based on the specific material being worked with. Each technique has its advantages and is suited to different types of materials. Understanding the nuances of these techniques is crucial for achieving strong and durable welds in upholstery applications.
Moreover, the choice of welding equipment can significantly impact the quality and efficiency of the welding process. Investing in high-quality equipment that aligns with the specific material and technique requirements is essential for achieving optimal results. Therefore, understanding the intricacies of materials and welding techniques is fundamental when selecting upholstery welding equipment.
This understanding forms the basis for calculating the upfront costs associated with acquiring the necessary tools and equipment for upholstery welding.
Calculating the Upfront Costs
To accurately determine the upfront costs of upholstery welding equipment, a comprehensive assessment of the specific material and technique requirements is essential. Calculating the upfront investment in upholstery welding equipment involves considering various budget considerations.
Here’s a breakdown of the key aspects to consider:
-
Equipment Cost: The initial investment includes the cost of the welding machine, welding tools, and any additional accessories needed for the specific upholstery welding technique.
-
Training and Certification: Budgeting for training and certification programs for the upholstery welding equipment is crucial to ensure that the workforce is proficient in its operation, maintenance, and safety protocols.
-
Facility Modifications: Assessing and budgeting for any necessary modifications to the facility to accommodate the upholstery welding equipment is vital, including electrical requirements, ventilation, and space allocation.
Long-Term Financial Benefits
Assessing the long-term financial benefits of integrating upholstery welding equipment requires a thorough evaluation of the equipment’s potential cost savings and increased production efficiency.
The upfront investment in upholstery welding equipment can yield substantial long-term financial benefits, thereby increasing profitability for upholstery manufacturers. By strategically investing in this equipment, businesses can significantly reduce labor costs, material wastage, and production time. The efficient and precise welding provided by the equipment ensures that the upholstery pieces are of high quality, reducing the need for rework and enhancing the overall product quality.
Additionally, the increased production efficiency enables manufacturers to fulfill orders more quickly, potentially leading to increased sales and customer satisfaction. This strategic investment in upholstery welding equipment not only contributes to long-term cost savings but also positions businesses to meet the growing demand for high-quality upholstered products.
Consequently, it is essential to consider the long-term financial benefits when evaluating the integration of upholstery welding equipment.
Transitioning into the subsequent section, it is crucial to delve into the productivity enhancements and efficiency achieved through the utilization of this equipment.
Productivity Enhancements and Efficiency
An upholstery manufacturer can achieve significant productivity enhancements and improved efficiency through the integration of welding equipment into their production processes. This integration leads to various benefits, including:
-
Increased Production Speed: Welding equipment enables faster assembly and joining of upholstery components, reducing production cycle times and increasing overall output.
-
Enhanced Quality Control: Utilizing welding equipment ensures precise and consistent bonding, leading to higher quality and more durable upholstery products.
-
Streamlined Equipment Maintenance: Modern welding equipment often comes with advanced maintenance features, such as self-diagnostic systems and predictive maintenance capabilities, reducing downtime and enhancing overall equipment reliability.
By leveraging these productivity improvements and prioritizing equipment maintenance, upholstery manufacturers can optimize their operations, reduce costs, and meet the growing demands of the market.
It is essential for manufacturers to carefully consider the long-term benefits of incorporating welding equipment into their production processes, as it not only enhances productivity but also contributes to sustaining a competitive edge in the industry.
Evaluating the Overall ROI
The integration of welding equipment into upholstery manufacturing processes not only enhances productivity and efficiency but also prompts a careful evaluation of the overall return on investment (ROI).
When evaluating the overall ROI of upholstery welding equipment, it is essential to employ robust evaluation techniques and conduct a comprehensive cost analysis. One evaluation technique commonly used is the cost-benefit analysis, which involves comparing the total costs of implementing the welding equipment with the expected benefits, such as increased production output and reduced labor costs.
Additionally, conducting a thorough cost analysis involves identifying all the costs associated with the equipment, including the initial purchase cost, installation expenses, training costs, and ongoing maintenance and operational expenses. It is crucial to measure these costs against the anticipated financial gains and savings resulting from the equipment’s implementation.
Frequently Asked Questions
What Are the Safety Considerations and Potential Risks Associated With Using Upholstery Welding Equipment?
Safety precautions and potential hazards associated with upholstery welding equipment include the risk of burns, exposure to fumes, and electrical hazards. Training requirements and certification are essential to ensure proper handling and minimize workplace accidents.
Are There Any Specific Training or Certification Requirements for Operating Upholstery Welding Equipment?
Training requirements for operating upholstery welding equipment vary by jurisdiction and employer. Certification requirements may be needed, with some areas mandating specific certifications for safety and quality assurance. Employers should ensure compliance with regulations.
Can Upholstery Welding Equipment Be Used for Other Applications Besides Upholstery, Such as Automotive or Marine Upholstery?
Upholstery welding equipment can indeed be utilized for a range of applications beyond upholstery, including automotive and marine upholstery. Its versatility and precision make it suitable for various industries, offering a cost-effective solution for diverse welding needs.
What Are the Environmental Impacts and Sustainability Considerations of Using Upholstery Welding Equipment?
When considering the environmental impacts and sustainability considerations of using upholstery welding equipment, it is essential to evaluate its energy consumption, waste generation, and potential emissions. Assessing its overall ecological footprint is crucial for informed decision-making.
Are There Any Ongoing Maintenance or Servicing Requirements for Upholstery Welding Equipment?
Like a well-maintained garden, upholstery welding equipment requires regular upkeep to ensure optimal performance. Maintenance requirements and servicing intervals are essential to uphold the equipment’s efficiency, longevity, and safety in upholstery manufacturing operations.
Conclusion
In conclusion, the cost-benefit analysis of upholstery welding equipment demonstrates a clear advantage for businesses. Despite the initial investment, the long-term financial benefits and productivity enhancements make it a worthwhile investment.
When all factors are considered, the overall return on investment speaks for itself. The proof is in the pudding, as businesses can expect to see a significant improvement in efficiency and profitability with the implementation of upholstery welding equipment.
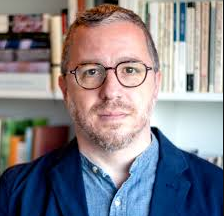
Dillon Hince, an expert in the realm of upholstery welding, brings a wealth of knowledge and experience to the craft. As the driving force behind nodpu.com, Dillon combines a passion for precision and creativity, offering unique insights into the art of seamlessly melding fabrics and materials. With a commitment to excellence, Dillon Hince is your go-to resource for innovative upholstery welding techniques, transforming ordinary pieces into extraordinary works of functional art.