The Latest Trends in Upholstery Welding Materials
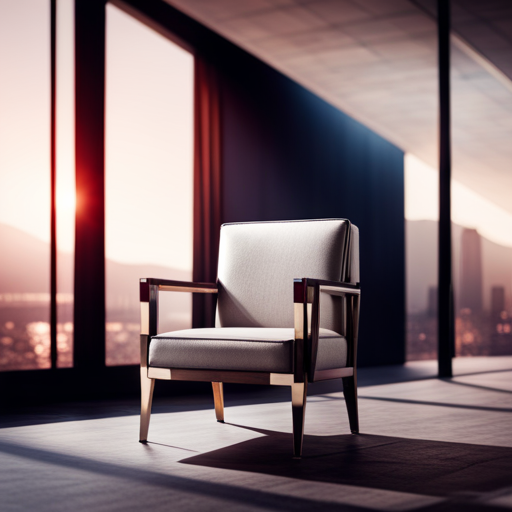
Coinciding with the ever-evolving demands of the upholstery industry, the latest trends in welding materials have ushered in a new era of innovation and efficiency.
From advanced synthetic materials to sustainable options, the landscape of upholstery welding is witnessing a transformation.
High-frequency welding technology, integration of smart fabrics, and multi-material welding innovations are among the key drivers shaping the future of upholstery welding materials.
This article delves into the cutting-edge developments revolutionizing the upholstery welding industry.
Advanced Synthetic Materials
As manufacturers seek to improve the durability and performance of upholstery welding materials, they are increasingly turning to advanced synthetic materials that offer superior strength and flexibility. Synthetic innovations have revolutionized the upholstery welding industry, providing a wide range of materials that can withstand the demands of modern furniture design. These advanced synthetic materials, such as polyurethane and polyester blends, are engineered to enhance the longevity and resilience of upholstery welds, ensuring that the end products meet the highest quality standards.
One of the key advantages of advanced synthetic materials is their compatibility with a variety of fabrics. Whether it’s leather, vinyl, or woven textiles, these materials offer excellent adhesion and compatibility, resulting in durable and visually appealing welds. Manufacturers can now confidently work with different fabric types, knowing that these synthetic materials will deliver consistent and reliable results.
Furthermore, the flexibility of these advanced synthetic materials allows for greater design freedom, enabling the creation of intricate and complex upholstery patterns without compromising on strength. This versatility has propelled synthetic materials to the forefront of upholstery welding, driving innovation and setting new standards for durability and performance.
High-Frequency Welding Technology
The usage of high-frequency welding technology in the upholstery industry has significantly enhanced the precision and efficiency of joining advanced synthetic materials. This innovative welding technique offers numerous benefits, including improved welding efficiency and enhanced material compatibility.
Furthermore, high-frequency welding technology has a wide range of industry applications, from automotive upholstery to furniture manufacturing, due to its ability to seamlessly join various synthetic materials. Additionally, this technology contributes to substantial cost savings by reducing production time and minimizing material waste. Its precise and rapid welding process ensures a high-quality finish while optimizing resource utilization.
Moreover, the versatility of high-frequency welding technology allows for the creation of intricate designs and patterns, expanding the creative possibilities in upholstery manufacturing. As a result, this advanced welding technique has become an indispensable tool for upholsterers seeking to achieve superior quality, cost-effective production, and innovative design solutions.
Sustainable and Eco-Friendly Options
Utilizing sustainable and eco-friendly materials for upholstery welding aligns with the growing demand for environmentally conscious manufacturing practices, complementing the advancements in high-frequency welding technology. Manufacturers are increasingly turning to sustainable textiles and eco-friendly alternatives to meet consumer demand for greener products. These materials not only reduce the environmental impact but also offer comparable performance and durability to traditional materials.
Sustainable Textiles | Eco-Friendly Alternatives | Benefits |
---|---|---|
Organic Cotton | Recycled Polyester | Reduced environmental impact |
Hemp | Linen | Energy and resource conservation |
Bamboo | Tencel (Lyocell) | Biodegradability and renewability |
Integration of Smart Fabrics
The integration of smart fabrics in upholstery represents a significant advancement in the industry. These fabrics offer a wide range of applications, from temperature regulation to moisture management, enhancing the comfort and functionality of upholstered furniture.
With ongoing technological advancements, the possibilities for smart fabrics in upholstery are expanding, promising innovative solutions for both consumers and manufacturers.
Smart Fabric Applications
Smart fabric applications are increasingly being integrated into upholstery welding materials to enhance functionality and performance. This integration is driving smart fabric development into future applications, opening new possibilities for innovative upholstery solutions.
The following are key areas where smart fabrics are revolutionizing upholstery materials:
-
Sensory Integration: Smart fabrics are being used to integrate sensors that can monitor body temperature, posture, and pressure points, enhancing the ergonomic design of upholstered furniture.
-
Health Monitoring: Upholstery materials are being designed with smart fabrics that can monitor vital signs and provide real-time health data, offering a new level of comfort and safety for users.
-
Interactive Interfaces: Smart fabric applications enable the integration of interactive touch interfaces into upholstery, providing seamless control of integrated technologies.
-
Environmental Adaptability: Smart fabrics are being utilized to create upholstery materials that can adapt to environmental changes, ensuring optimal comfort in any condition.
These developments in smart fabric applications are revolutionizing upholstery welding materials and setting the stage for enhanced comfort and functionality in upholstered furniture.
Enhanced Comfort and Functionality
An increasing number of upholstery welding materials are incorporating smart fabric technology to enhance comfort and functionality.
Smart fabrics are being integrated into upholstery to provide ergonomic design and improved material durability. These fabrics are designed to respond to the user’s body, providing enhanced support and comfort.
By utilizing sensors and responsive materials, smart fabrics can adjust to the user’s posture and movements, promoting better sitting experiences.
Additionally, the incorporation of smart fabrics enhances the durability of upholstery welding materials, ensuring longevity and resilience to wear and tear.
This integration of smart fabrics not only elevates the comfort and functionality of upholstery but also aligns with the growing demand for innovative and adaptive furniture solutions in modern living spaces.
Technological Advancements in Upholstery
Incorporating technological advancements in upholstery, particularly the integration of smart fabrics, is revolutionizing the comfort, functionality, and durability of modern furniture. This integration is driving significant improvements in the upholstery industry, including:
-
Robotic Welding: Smart fabrics are being seamlessly integrated using advanced robotic welding techniques, ensuring precision and consistency in the assembly process.
-
Material Durability: Smart fabrics are enhancing material durability, making upholstery more resistant to wear and tear, thus extending the lifespan of furniture.
-
Enhanced Functionality: Smart fabrics are enabling the incorporation of innovative features such as temperature regulation, moisture control, and even interactive capabilities, elevating the functionality of upholstered furniture.
-
Seamless Integration: The integration of smart fabrics is being done in a way that maintains the aesthetic appeal of the furniture while seamlessly incorporating advanced technological capabilities.
Heat-Activated Bonding Solutions
In the realm of upholstery welding materials, heat-activated bonding solutions have emerged as a focal point of interest. These solutions offer advantages such as enhanced durability and flexibility, making them compatible with an array of fabrics.
Moreover, their impact on production efficiency is a key aspect that merits exploration in the context of upholstery manufacturing.
Advantages of Heat-Activated Bonding
Utilizing heat-activated bonding solutions offers numerous advantages in upholstery welding materials, providing enhanced strength and durability while minimizing the use of adhesives. The benefits of heat-activated bonding include:
-
Improved Durability: Heat-activated bonding creates strong, long-lasting bonds, ensuring the durability of the upholstery welding materials.
-
Cost Efficiency: By reducing the need for additional adhesives, heat-activated bonding solutions contribute to cost efficiency in manufacturing processes.
-
Enhanced Strength: The heat-activated bonding process results in materials with increased strength, improving the overall quality of the final product.
-
Minimized Chemical Use: Heat-activated bonding reduces reliance on chemical adhesives, making it an environmentally friendly choice.
This innovative bonding method not only offers improved durability and cost efficiency but also aligns with sustainable manufacturing practices.
The next section will explore its compatibility with various fabrics.
Compatibility With Various Fabrics
The compatibility of heat-activated bonding solutions with various fabrics in upholstery welding materials is a crucial consideration for manufacturers seeking to enhance strength and durability while maintaining cost efficiency. Compatibility tests are essential to ensure the heat-activated bonding solutions adhere effectively to different fabrics, thereby optimizing fabric performance and material durability. Factors such as heat resistance and material durability play a significant role in determining the suitability of these bonding solutions for specific fabric types. This ensures that the upholstery welding materials meet the required standards and provide the desired level of performance. The table below provides a concise summary of the compatibility of heat-activated bonding solutions with various fabrics in upholstery welding materials.
Fabric Type | Compatibility Rating |
---|---|
Cotton | High |
Polyester | Medium |
Leather | High |
Nylon | Low |
Velvet | Medium |
Impact on Production Efficiency
An analysis of the impact of heat-activated bonding solutions on production efficiency in upholstery welding materials reveals their significant influence on manufacturing processes and overall operational productivity.
-
Improved Productivity: Heat-activated bonding solutions contribute to faster production cycles, reducing the time required for welding different fabric components.
-
Enhanced Production Optimization: These solutions enable better control over the welding process, leading to fewer errors and rework, ultimately optimizing the overall production workflow.
-
Cost Savings: By streamlining the welding process and minimizing material wastage, heat-activated bonding solutions contribute to cost savings, directly impacting the bottom line.
-
Quality Assurance: The use of these solutions ensures consistent and durable bonds, contributing to higher-quality finished products and customer satisfaction.
Multi-Material Welding Innovations
How can multi-material welding innovations improve the durability and aesthetics of upholstered furniture?
Robotic welding and advanced joining techniques play a pivotal role in enhancing the quality and appearance of upholstered furniture.
Multi-material welding enables the seamless integration of different components, such as metal frames and fabric upholstery, resulting in more durable and visually appealing furniture pieces.
Robotic welding systems offer precision and consistency in joining various materials, ensuring strong and reliable bonds. This level of accuracy is particularly crucial in creating furniture that can withstand the rigors of everyday use.
Additionally, multi-material welding allows for the combination of diverse materials, opening up new design possibilities and enabling the creation of furniture with unique and sophisticated aesthetics.
By utilizing innovative joining techniques, manufacturers can achieve sleek and unobtrusive welds, contributing to the overall visual appeal of the furniture.
Ultimately, multi-material welding innovations not only enhance the structural integrity of upholstered furniture but also elevate their aesthetic appeal, meeting the evolving demands of the market for both durability and design.
Frequently Asked Questions
Are There Any Upcoming Advancements in Upholstery Welding Materials That Are Not Covered in This Article?
Upcoming advancements in upholstery welding materials are driven by market trends and future developments. Material innovations and technological breakthroughs are expected to enhance durability, flexibility, and ease of application, revolutionizing the industry.
How Do Upholstery Welding Materials Compare in Terms of Cost and Durability?
When comparing upholstery welding materials, a thorough analysis of cost and durability is essential. Cost comparison involves examining initial investment versus long-term value. Durability analysis evaluates the material’s ability to withstand wear and tear over time.
Are There Any Specific Safety Concerns or Precautions to Consider When Using These Advanced Materials for Upholstery Welding?
When using advanced upholstery welding materials, it’s crucial to prioritize safety precautions and consider material compatibility. This involves ensuring proper ventilation, using protective equipment, and conducting thorough testing to guarantee safe and effective welding processes.
Can These Welding Materials Be Used for Both Indoor and Outdoor Upholstery Applications?
Indoor and outdoor upholstery applications necessitate distinct material properties. Upholstery welding materials suitable for indoors may not withstand environmental factors outdoors. Considering the environmental impact of these materials is vital for sustainable upholstery solutions.
What Are the Potential Challenges or Limitations Associated With Using These Innovative Upholstery Welding Materials?
Innovative upholstery welding materials present challenges in terms of maintenance requirements and potential environmental impact. Limitations may arise in their compatibility with certain fabrics or in meeting specific industry standards for safety and durability.
Conclusion
In conclusion, the latest trends in upholstery welding materials highlight the advancements in synthetic materials, high-frequency welding technology, sustainable and eco-friendly options, smart fabrics, heat-activated bonding solutions, and multi-material welding innovations.
These innovations have the potential to revolutionize the upholstery industry by offering durable, efficient, and environmentally friendly solutions.
One anticipated objection to these trends may be the initial cost of implementing these advanced materials and technologies. However, the long-term benefits in terms of durability and sustainability outweigh the initial investment.
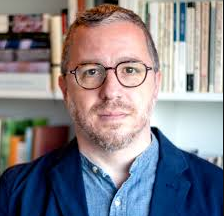
Dillon Hince, an expert in the realm of upholstery welding, brings a wealth of knowledge and experience to the craft. As the driving force behind nodpu.com, Dillon combines a passion for precision and creativity, offering unique insights into the art of seamlessly melding fabrics and materials. With a commitment to excellence, Dillon Hince is your go-to resource for innovative upholstery welding techniques, transforming ordinary pieces into extraordinary works of functional art.