Addressing Common Challenges in Upholstery Welding
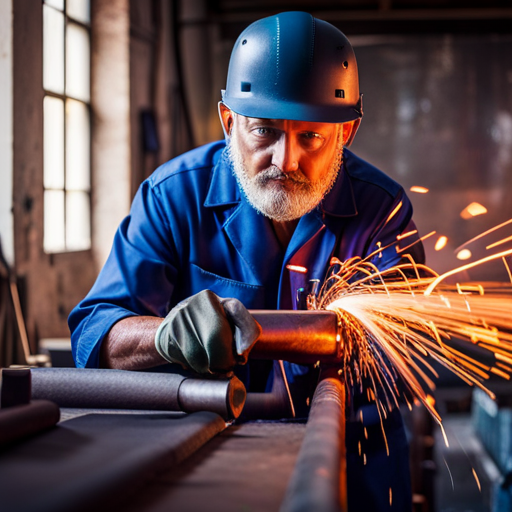
Like the intricate stitching that transforms fabric into art, upholstery welding requires precision and skill.
In the world of upholstery, challenges such as material selection, seam strength, and heat management can impact the quality of the final product.
This article delves into the nuances of addressing these common obstacles, offering insights and strategies for achieving impeccable welding results.
Material Selection
Frequently, the success of upholstery welding depends heavily on the careful selection of materials to ensure durability and aesthetic appeal. Fabric durability is a critical factor in material selection, as the upholstery will be subject to constant use and potential wear and tear. It’s essential to choose fabrics that can withstand the demands of everyday use without compromising on comfort or style.
Additionally, color choices play a significant role in upholstery design and aesthetics. The selected colors should complement the overall design scheme, enhance the visual appeal of the furniture, and withstand potential fading or discoloration over time.
Upholstery design and aesthetics are intertwined with material selection, as the chosen materials will ultimately determine the visual impact and longevity of the finished product. The fabric’s texture, pattern, and overall look should align with the desired aesthetic outcome. By carefully considering these factors, upholstery professionals can ensure that the materials chosen not only meet functional requirements but also contribute to the overall visual appeal of the finished product.
Transitioning into the subsequent section about ‘seam strength’, the careful selection of materials sets the foundation for ensuring the structural integrity and longevity of upholstery welds.
Seam Strength
When it comes to achieving optimal seam strength in upholstery welding, it is essential to consider various welding techniques that enhance the overall durability of the seams.
Additionally, implementing seam reinforcement methods can significantly contribute to the longevity and robustness of the upholstery.
Furthermore, careful consideration of material compatibility is crucial to ensure that the welded seams withstand the expected stress and wear in upholstery applications.
Welding Techniques for Strength
One essential consideration for achieving strong seam strength in upholstery welding is the selection of appropriate welding techniques. The joint design and penetration depth, welding speed, and filler material all play crucial roles in determining the strength of the weld.
Consideration | Key Factors |
---|---|
Joint Design | Proper joint design ensures optimal contact between the materials being welded, resulting in a strong seam. |
Penetration Depth | Sufficient penetration ensures that the weld extends deep into the materials, enhancing its strength. |
Welding Speed | Controlling the welding speed is essential to achieve proper heat distribution and fusion, contributing to seam strength. |
Filler Material | Selecting the right filler material is vital for reinforcing the seam and ensuring a strong bond between the materials. |
Heat Control | Proper heat control during welding prevents material degradation and contributes to seam strength. |
Understanding these factors is vital for achieving strong seam strength in upholstery welding.
This leads us to the subsequent section about ‘seam reinforcement methods’.
Seam Reinforcement Methods
Continuing from the consideration of welding techniques for strength, it is vital to address seam reinforcement methods to ensure optimal seam strength in upholstery welding.
-
Stitching Reinforcement: One of the most common methods for reinforcing upholstery seams is through stitching. Double stitching or using heavy-duty thread can significantly enhance the seam’s durability and strength.
-
Seam Durability: Upholstery welding often involves high levels of wear and tear. Therefore, it is crucial to employ seam reinforcement methods that enhance the durability of the seam, ensuring it can withstand constant use and potential stress.
-
Material Selection: Choosing the right materials for seam reinforcement, such as using reinforced tapes or additional layers of fabric, can greatly contribute to the overall strength and longevity of the upholstery seam.
Material Compatibility Considerations
How can material compatibility enhance seam strength in upholstery welding? Material compatibility plays a crucial role in determining the overall strength and durability of welded seams in upholstery. When welding materials with compatible properties are used, the resulting seam is more likely to exhibit higher tensile strength and resistance to wear and tear. Material testing is essential to ensure that the welding material properties are well-suited for the specific upholstery application. A thorough understanding of the materials being welded, including their composition, thickness, and flexibility, is necessary to achieve optimal seam strength. By carefully considering material compatibility, upholsterers can ensure that the welded seams meet the required performance standards, leading to longer-lasting and more resilient upholstery products.
Material Compatibility Considerations | Benefits |
---|---|
Enhanced Seam Strength | Increased Durability |
Improved Tensile Strength | Better Wear Resistance |
Optimal Performance | Long-lasting Upholstery |
Reduced Maintenance Needs | Higher Customer Satisfaction |
Enhanced Product Reliability | Improved Safety |
Heat Management
In the realm of upholstery welding, effective heat management is critical for ensuring high-quality, durable seams.
Welding temperature control, heat distribution techniques, and managing thermal stress are pivotal components of heat management.
Welding Temperature Control
To ensure precise and consistent welds in upholstery, welding temperature control, also known as heat management, is crucial. Proper control of welding temperature is essential for achieving high-quality welds in upholstery manufacturing.
This involves:
-
Understanding the Welding Process: Different welding processes require specific temperature control techniques. For example, hot air welding and RF welding demand precise temperature monitoring to ensure the correct fusion and bonding of materials.
-
Temperature Monitoring: Utilizing thermocouples and infrared thermometers to monitor the temperature in real-time during the welding process is essential for maintaining consistency and quality.
-
Adjusting Heat Settings: Implementing precise heat management by adjusting the temperature settings on welding equipment to match the requirements of the materials being welded is critical for achieving durable and aesthetically pleasing upholstery welds.
Heat Distribution Techniques
Effective heat distribution techniques are crucial for achieving consistent and high-quality upholstery welds. Welding precision and temperature control are directly impacted by heat management and material compatibility.
To ensure uniform heat distribution, it is essential to use welding equipment with precise temperature controls and suitable for the specific materials being welded. Heat management also involves the use of proper welding techniques and tools to evenly distribute heat across the upholstery materials.
Material compatibility is an important consideration as different materials have varying heat absorption and dissipation rates. By understanding the unique properties of the materials being welded, upholstery welders can implement appropriate heat distribution techniques to achieve strong and durable welds.
Consistency in heat distribution not only ensures the structural integrity of the weld but also contributes to the overall aesthetics of the upholstery.
Managing Thermal Stress
How can upholstery welders effectively manage thermal stress during the welding process?
Managing Thermal Stress
-
Understanding Thermal Expansion: Upholstery welders need to have a thorough understanding of how different materials expand and contract when exposed to heat. By comprehending thermal expansion, welders can anticipate potential stress points and take preventative measures.
-
Implementing Stress Management Techniques: Utilizing stress management techniques such as preheating, post-weld heat treatment, and controlled cooling can help mitigate the impact of thermal stress on upholstery welding. These techniques are essential for maintaining the structural integrity of welded components.
-
Welding Process Optimization: By optimizing welding parameters and techniques, upholstery welders can minimize thermal stress while improving productivity. This involves selecting the appropriate welding method, adjusting parameters such as heat input, and using efficient welding equipment.
Pressure Control
The proper application of pressure control is essential for achieving high-quality and consistent welds in upholstery manufacturing. Welding pressure and equipment calibration are crucial factors in ensuring the desired outcome. Pressure consistency is vital to prevent material deformation during the welding process. To illustrate the significance of pressure control, consider the following table:
Factors | Importance |
---|---|
Welding Pressure | Proper pressure ensures strong and durable welds. |
Equipment Calibration | Regular calibration maintains consistent welding pressure. |
Pressure Consistency | Ensures uniformity and prevents material deformation. |
Maintaining the right welding pressure and equipment calibration is essential to achieve consistent and high-quality welds. It ensures that the material is not deformed during the welding process, ultimately resulting in a durable and aesthetically pleasing finished product. Proper pressure control is a critical aspect of upholstery welding and requires careful attention to detail.
Next, let’s delve into the importance of welding machine compatibility.
Welding Machine Compatibility
Proper welding machine compatibility is essential for achieving consistent and high-quality welds, as it ensures that the welding equipment is suitable for maintaining the required pressure and performing precise welds on upholstery materials.
When considering welding machine compatibility in upholstery welding, several key factors should be taken into account:
-
Welding Equipment Specifications: It is crucial to ensure that the welding machine meets the specific requirements for welding upholstery materials. This includes factors such as the type of welding technology, the capacity to maintain consistent heat, and the ability to control pressure during the welding process.
-
Material Compatibility: Different upholstery materials may require specific welding techniques and machine settings. Understanding the compatibility of the welding machine with various upholstery materials is essential for achieving optimal weld quality.
-
Machine Maintenance: Regular maintenance of welding equipment is vital for ensuring its compatibility with upholstery welding. This includes inspection, calibration, and servicing to guarantee that the machine operates at its best capacity and delivers consistent welds.
Stitching Accuracy
To ensure precise stitching accuracy in upholstery welding, upholsterers must carefully consider the alignment of the welding equipment with the material and the maintenance of the machinery.
Thread tension is a critical factor in achieving stitching precision. Proper adjustment of the thread tension is essential to prevent loose or tight stitching, which can compromise the overall quality of the upholstered piece. Upholsterers need to regularly inspect and adjust the thread tension to ensure consistent and even stitching.
Additionally, maintaining the machinery is crucial for stitching accuracy. Regular cleaning and lubrication of the equipment prevent thread snags and ensure smooth stitching motion, ultimately contributing to the precision of the finished product.
Moreover, aligning the welding equipment with the material is imperative. Misalignment can lead to crooked stitching lines and uneven seam allowances, affecting the overall aesthetics and structural integrity of the upholstery. Upholsterers should pay close attention to the positioning of the material in relation to the welding equipment to guarantee accurate and uniform stitching.
Environmental Factors
Achieving optimal stitching accuracy in upholstery welding requires consideration of environmental factors such as temperature and humidity levels within the workspace. To ensure a conducive environment for upholstery welding, the following factors need to be addressed:
-
Environmental impact, sustainability measures: Upholstery welding processes can have a significant environmental impact due to the use of materials and energy. Implementing sustainability measures such as using eco-friendly materials and optimizing energy usage can mitigate this impact.
-
Workplace safety, ventilation requirements: Upholstery welding often involves the use of adhesives, sealants, and other potentially hazardous substances. Adequate ventilation systems and workplace safety protocols should be in place to ensure the well-being of the workers and to comply with safety regulations.
-
Temperature and humidity control: Fluctuations in temperature and humidity levels can affect the quality of welding and the durability of the finished products. Maintaining stable temperature and humidity conditions in the workspace is crucial for achieving consistent welding results.
Considering these environmental factors is essential not only for the quality of the upholstery welding but also for the overall sustainability and safety of the workspace.
Transitioning into the subsequent section about ‘quality assurance’, it is imperative to address the impact of environmental factors on the overall quality of the upholstery welding process.
Quality Assurance
Transitioning from the considerations of environmental factors, ensuring quality assurance in upholstery welding necessitates meticulous attention to detail and adherence to industry standards. Quality control is integral to the upholstery welding process, as it ensures that the final product meets the required specifications and performance standards. Upholstery welders must employ rigorous inspection techniques throughout the welding process to identify any potential defects or imperfections that could compromise the quality of the welds. This involves conducting visual inspections, non-destructive testing, and dimensional checks to verify the integrity and strength of the welds.
Furthermore, quality assurance in upholstery welding involves implementing comprehensive quality control measures at every stage of the manufacturing process. This includes stringent adherence to welding procedures, material specifications, and workmanship standards. Upholstery welders must also utilize advanced inspection techniques such as ultrasonic testing, radiographic testing, and dye penetrant testing to detect any internal or surface defects that may affect the weld quality.
Frequently Asked Questions
What Are the Best Practices for Maintaining the Welding Machine to Ensure Optimal Performance?
To ensure optimal performance of a welding machine, regular maintenance is essential. This includes cleaning, lubricating, and inspecting parts for wear. Implementing troubleshooting techniques can help identify and address issues promptly, minimizing downtime and ensuring smooth operation.
How Can Environmental Factors, Such as Temperature and Humidity, Impact the Quality of Upholstery Welding?
Environmental factors such as temperature and humidity can significantly impact the quality of upholstery welding. Fluctuations in temperature and high humidity levels can compromise the integrity of welds, leading to challenges in achieving consistent and durable welds.
What Are Some Common Quality Assurance Checks That Can Be Performed to Ensure the Integrity of Upholstery Welds?
Quality control in upholstery welding involves rigorous inspection processes to ensure weld integrity. Common quality assurance checks include visual inspections for weld consistency, strength testing, and non-destructive testing methods such as ultrasonic or dye penetrant inspection.
Are There Specific Techniques for Ensuring Stitching Accuracy When Working With Different Types of Upholstery Materials?
When working with different types of upholstery materials, it’s essential to employ specific stitching techniques to ensure accuracy and material compatibility. Utilizing appropriate needle types, thread tension, and stitch length can optimize stitching results.
What Are the Potential Consequences of Using a Welding Machine That Is Not Compatible With the Specific Type of Upholstery Material Being Used?
Using a welding machine incompatible with specific upholstery material can result in subpar welds, compromised material integrity, and potential safety hazards. Compatibility ensures precise bonding and durability, safeguarding both the upholstered item and the user.
Conclusion
In conclusion, addressing common challenges in upholstery welding requires careful consideration of several factors:
-
Material selection: Choosing the right materials for upholstery welding is crucial. Different materials may require different welding techniques and tools.
-
Seam strength: Ensuring strong and durable seams is essential for upholstery welding. Weak seams can lead to product failure and customer dissatisfaction.
-
Heat management: Proper heat management is necessary to prevent damage to the materials and maintain the integrity of the welds. Overheating can cause burning or melting, while insufficient heat may result in weak welds.
-
Pressure control: Controlling the pressure during welding is important to achieve consistent and strong welds. Too much pressure can deform the materials, while too little pressure may result in weak seams.
-
Welding machine compatibility: Ensuring that the welding machine is compatible with the materials being used is crucial. Incompatible machines can lead to inconsistent welds and poor quality.
-
Stitching accuracy: Proper stitching is necessary to reinforce the welds and add additional strength to the seams. Accurate stitching ensures that the welds are secure and durable.
-
Environmental factors: Environmental conditions such as temperature and humidity can affect the welding process. It is important to consider these factors and make adjustments as needed.
-
Quality assurance: Implementing quality control measures is essential to ensure that the finished products meet the required standards. Regular inspections and testing can help identify any issues and prevent defects from reaching the market.
For example, a furniture manufacturer experienced a decrease in product quality due to inconsistent welding machine compatibility. This led to an increase in product returns and customer complaints. By addressing these challenges and implementing appropriate solutions, manufacturers can improve the overall quality and durability of their upholstery products.
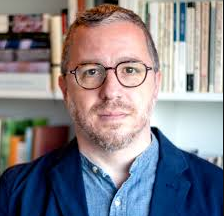
Dillon Hince, an expert in the realm of upholstery welding, brings a wealth of knowledge and experience to the craft. As the driving force behind nodpu.com, Dillon combines a passion for precision and creativity, offering unique insights into the art of seamlessly melding fabrics and materials. With a commitment to excellence, Dillon Hince is your go-to resource for innovative upholstery welding techniques, transforming ordinary pieces into extraordinary works of functional art.