Cost-Effective Solutions in Upholstery Welding

Just as a skilled artisan seamlessly weaves together the finest threads to create a masterpiece, the art of upholstery welding requires precision, expertise, and cost-effective solutions.
In the world of upholstery fabrication, where every stitch counts, efficiency and quality are paramount.
This article explores the innovative techniques, advanced technologies, and strategic practices that enable upholstery manufacturers to achieve cost-effective welding solutions without compromising on durability and aesthetic appeal.
Advanced Welding Technologies
Advanced welding technologies have revolutionized the upholstery industry by enhancing precision and efficiency in joining materials. These advanced techniques have paved the way for the use of innovative materials and have significantly improved the overall quality of upholstered products.
One such technology that has made a substantial impact is ultrasonic welding. This method utilizes high-frequency ultrasonic acoustic vibrations to create solid-state welds, resulting in strong and precise seams.
Additionally, laser welding has gained traction in the industry for its ability to join materials with minimal heat input, reducing the risk of damage to delicate fabrics.
Furthermore, advancements in adhesive bonding techniques have provided alternatives to traditional stitching, offering a sleek and seamless finish while maintaining durability.
These advanced welding technologies have not only improved the structural integrity of upholstered products but have also streamlined the manufacturing process. By enhancing the precision of joining materials, manufacturers have been able to minimize material waste and optimize production timelines.
As the upholstery industry continues to embrace these advanced techniques, the potential for further innovation and improvement in product quality remains promising.
Efficient Production Practices
Efficient production practices in upholstery welding build upon the advancements in welding technologies, optimizing manufacturing processes to minimize waste and maximize output. Workflow streamlining is a key aspect of efficient production practices. By analyzing and reorganizing the sequence of tasks involved in upholstery welding, manufacturers can identify bottlenecks and inefficiencies, leading to a more streamlined and efficient workflow. This can include reconfiguring workstations, implementing lean manufacturing principles, and utilizing automation where appropriate.
Labor efficiency is another crucial component of efficient production practices. This involves maximizing the productivity of the workforce through proper training, effective task allocation, and the use of ergonomic tools and equipment. By ensuring that workers are equipped with the necessary skills and tools, manufacturers can significantly enhance productivity while reducing the risk of injuries and fatigue.
Efficient Production Practices | ||
---|---|---|
Benefits | Strategies | Implementation |
Minimize waste | Workflow streamlining | Analyze and reorganize tasks |
Maximize output | Labor efficiency | Proper training and task allocation |
Improved productivity | Automation | Utilize technology strategically |
Implementing these strategies not only improves the overall efficiency of upholstery welding but also contributes to cost savings and higher-quality output.
Material Optimization Strategies
The material optimization strategies in upholstery welding aim to maximize the utility of raw materials and minimize waste, further enhancing the cost-effectiveness and efficiency of the manufacturing process. To achieve this, the following strategies are employed:
-
Precision Cutting: Utilizing advanced cutting technologies such as computer numerical control (CNC) machines to ensure precise and efficient cutting of upholstery materials, minimizing waste and maximizing material efficiency.
-
Advanced Welding Techniques: Implementing innovative welding processes such as ultrasonic welding or hot wedge welding, which optimize the use of materials by ensuring strong and durable seams while minimizing material consumption.
-
Utilization of Fabric Scraps: Developing processes to effectively repurpose fabric scraps generated during upholstery production, such as utilizing them for smaller upholstery components or recycling them for use in other manufacturing processes.
-
Material Selection: Careful selection of materials based on their suitability for the welding process and the specific requirements of the upholstery, ensuring that the right materials are used in the right quantities to minimize waste and optimize material efficiency.
Cost-Effective Equipment Investments
Investing in cost-effective equipment is crucial for enhancing the efficiency and productivity of upholstery welding processes. It is essential to consider the long-term cost implications and benefits of equipment investments. Cost-effective equipment not only reduces operational expenses but also minimizes downtime due to maintenance and repairs. However, it’s important to ensure that the investment in equipment aligns with the specific needs of the upholstery welding operation. This can be achieved through thorough research, consultation with industry experts, and evaluating the track record of the equipment manufacturer.
A well-planned equipment investment strategy should also include provisions for equipment maintenance and training programs. Regular maintenance not only extends the lifespan of the equipment but also ensures that it operates at optimal levels, thereby maximizing productivity. Additionally, training programs for the workforce can enhance their skills in operating and maintaining the equipment, leading to improved efficiency and reduced errors.
Benefits of Cost-Effective Equipment Investments | |
---|---|
Reduced operational expenses | Enhanced productivity |
Minimized downtime | Alignment with specific operational needs |
Extended equipment lifespan | Improved workforce skills and efficiency |
Quality Control Measures
Implementing quality control measures is essential for ensuring the consistency and reliability of upholstery welding processes. To achieve high-quality welding results, the following measures can be implemented:
-
Regular Inspections: Conduct regular inspections of the welding equipment and materials to identify any potential defects or issues. This proactive approach can help in early defect detection and prevent further complications during the welding process.
-
Quality Assurance Testing: Implementing quality assurance tests at various stages of the welding process can help in identifying any deviations from the set standards. This can ensure that the final welded products meet the required quality criteria.
-
Employee Training: Provide comprehensive training to the welding operators to improve their skills and knowledge about defect detection and process improvement. Well-trained employees are better equipped to identify potential defects and take corrective actions.
-
Feedback Mechanism: Establish a feedback mechanism to gather insights from the welding operators about the challenges they face during the welding process. This feedback can be instrumental in identifying areas that require process improvement and enhancing overall welding quality.
Frequently Asked Questions
Can Upholstery Welding Be Used on a Variety of Materials, Including Leather and Vinyl?
Upholstery welding is a versatile process suitable for a variety of materials, including leather and vinyl. Leather offers durability, while vinyl provides flexibility, making both materials compatible with upholstery welding for various applications.
Are There Any Environmental Considerations or Sustainability Practices Associated With Upholstery Welding?
Upholstery welding presents environmental considerations and sustainability practices. It is crucial to assess the environmental impact of materials used, energy consumption, and waste management. Implementing sustainable practices, such as using eco-friendly materials, and efficient energy utilization, is essential.
How Does Upholstery Welding Impact the Overall Design and Aesthetic of Furniture and Automotive Interiors?
Upholstery welding significantly impacts the aesthetics and design flexibility of furniture and automotive interiors. It enables precise material compatibility, enhancing durability while allowing for intricate and seamless designs, contributing to the overall visual appeal and functionality.
What Are Some Common Challenges or Limitations in Upholstery Welding, and How Can They Be Addressed?
Addressing challenges in upholstery welding involves understanding limitations in materials and techniques, ensuring solutions align with design aesthetics and environmental impact. By employing innovative approaches and advanced materials, these challenges can be effectively overcome.
Are There Any Regulations or Industry Standards That Specifically Apply to Upholstery Welding Processes?
Regulations and safety standards governing upholstery welding processes are imperative to ensure workplace safety and product quality. Material compatibility and appropriate welding techniques are vital considerations to meet industry standards and maintain product integrity.
Conclusion
In conclusion, the implementation of cost-effective solutions in upholstery welding requires a combination of advanced welding technologies, efficient production practices, material optimization strategies, cost-effective equipment investments, and quality control measures.
By incorporating these strategies, businesses can achieve higher productivity, lower production costs, and improved product quality.
It’s time to ‘seize the day’ and embrace these innovative solutions to stay competitive in the market.
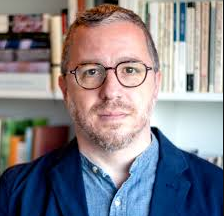
Dillon Hince, an expert in the realm of upholstery welding, brings a wealth of knowledge and experience to the craft. As the driving force behind nodpu.com, Dillon combines a passion for precision and creativity, offering unique insights into the art of seamlessly melding fabrics and materials. With a commitment to excellence, Dillon Hince is your go-to resource for innovative upholstery welding techniques, transforming ordinary pieces into extraordinary works of functional art.