Customizing Upholstery Welding Equipment for Unique Projects

Thinking outside the box is essential when it comes to customizing upholstery welding equipment for unique projects. In a world where one-size-fits-all solutions often fall short, the ability to modify and adapt tools and equipment to meet specific project requirements is a game-changer.
This article delves into the importance of tailored solutions, key considerations for modification, and techniques for adapting upholstery welding equipment, providing invaluable insights for professionals in the industry.
Importance of Customized Equipment
The importance of customized equipment in upholstery welding cannot be overstated. When it comes to upholstery welding, off-the-shelf equipment may not always meet the specific needs of a project. Customized equipment offers numerous benefits, primarily in terms of efficiency and effectiveness.
By tailoring equipment to the unique requirements of a project, upholstery welders can significantly improve their workflow and the quality of their work. This level of customization directly translates to cost-effectiveness, as it minimizes the need for rework and reduces material waste. Customized equipment also enhances efficiency by streamlining processes, thereby saving time and resources.
While the initial investment in customized equipment may seem higher than purchasing standard tools, the long-term benefits far outweigh the costs. Moreover, the ability to meet the exact specifications of a project can result in higher customer satisfaction and increased business opportunities. Ultimately, the importance of customized equipment in upholstery welding lies in its ability to deliver superior results while optimizing resources.
Key Considerations for Modification
When modifying upholstery welding equipment for unique projects, it is essential to carefully assess the specific requirements and constraints of the project. This ensures that any modifications made will effectively meet the project’s needs while maintaining safety and functionality.
Key considerations for modification include:
-
Project Requirements: Understanding the exact specifications and demands of the upholstery welding project is crucial. This includes the type of materials being used, the desired weld strength, and any specific design or size constraints.
-
Equipment Compatibility: Assessing the compatibility of the equipment with the intended modifications is essential. It’s important to ensure that the proposed changes will not compromise the overall functionality or safety of the welding equipment.
-
Modification Limitations: Identifying any limitations or restrictions associated with modifying the upholstery welding equipment is crucial. This includes considering factors such as warranty implications, regulatory compliance, and potential impacts on equipment lifespan.
-
Cost and Resource Implications: Evaluating the financial and resource implications of the proposed modifications is necessary. This includes assessing the cost of the modifications, availability of specialized parts or expertise, and any potential impact on project timelines.
Careful consideration of these key factors will help ensure that any modifications made to upholstery welding equipment align with the unique requirements of the project while maintaining equipment integrity and safety.
Tools and Equipment Adaptation Techniques
Adapting upholstery welding equipment for unique projects requires a meticulous assessment of tools and equipment adaptation techniques in order to ensure seamless integration with the project’s specific requirements and constraints.
Adapting tools and equipment modification are essential aspects of customizing upholstery welding equipment for specialized projects. One technique involves modifying the size and shape of nozzles to accommodate intricate welding patterns or hard-to-reach areas, ensuring precise and efficient welding.
Additionally, customization techniques such as adjustable temperature controls and specialized welding tips enable the equipment to cater to diverse materials and thicknesses, enhancing its versatility for different project demands. Furthermore, incorporating variable speed settings and ergonomic design modifications can improve the equipment’s maneuverability and operator comfort, making it suitable for prolonged usage in unique project environments.
These adaptation techniques are pivotal in ensuring that the upholstery welding equipment aligns with the distinct demands of specialized projects, ultimately contributing to the seamless execution of the welding processes.
Transitioning into the subsequent section about ‘examples of customized upholstery welding projects’, these adaptation techniques have been instrumental in achieving remarkable results across a wide range of unique and challenging projects.
Examples of Customized Upholstery Welding Projects
Utilizing these adaptation techniques, upholstery welding equipment has been successfully customized for a wide array of unique and challenging projects, demonstrating its versatility and precision in meeting specific project requirements. Examples of such customized upholstery welding projects include:
-
Customized Automotive Interiors: Upholstery welding equipment has been tailored to meet the specific needs of custom automotive interior projects, allowing for precise and durable seams on unique upholstery materials and designs.
-
Specialized Marine Upholstery: The customization of welding equipment has enabled the seamless joining of marine-grade upholstery materials, ensuring the durability and longevity required for marine applications.
-
Bespoke Furniture Upholstery: Welding equipment has been adapted to accommodate the intricate designs and materials often found in bespoke furniture upholstery, allowing for precise and aesthetically pleasing seams.
-
Aircraft Interior Refurbishment: Upholstery welding equipment has been customized to meet the stringent safety and quality standards of aircraft interiors, enabling the seamless integration of new upholstery materials in aircraft refurbishment projects.
These examples illustrate how customized upholstery welding equipment can be tailored to suit the unique requirements of various projects, ensuring high-quality and durable results in specialized fields such as automotive, marine, furniture, and aircraft upholstery.
Advantages of Tailored Solutions
One significant advantage of tailored solutions for upholstery welding equipment is the ability to precisely meet specific project requirements while ensuring optimal functionality and durability. Tailored efficiency allows for the customization of equipment to fit the unique needs of each project, resulting in enhanced productivity and cost-effectiveness. By utilizing unique solutions tailored to the specific demands of a project, upholstery welding equipment can offer improved precision, quality, and performance, leading to higher customer satisfaction and increased competitiveness in the market.
Advantages of Tailored Solutions | Emotional Response |
---|---|
Customized equipment to fit unique project requirements | Confidence and reassurance in the quality of the final product |
Enhanced productivity and cost-effectiveness | Excitement and motivation to take on challenging projects |
Improved precision, quality, and performance | Satisfaction and pride in delivering superior results |
Tailored solutions not only provide the practical benefits of meeting specific project requirements but also evoke an emotional response in the audience, instilling confidence, excitement, and satisfaction in the work being accomplished.
Frequently Asked Questions
Can Upholstery Welding Equipment Be Customized for Specialized Materials, Such as Leather or Vinyl?
Yes, upholstery welding equipment can be customized for specialized materials such as leather and vinyl. This customization involves adjusting settings, using specific tools, and applying techniques tailored to the unique properties of these materials.
What Are the Potential Drawbacks or Limitations of Modifying Upholstery Welding Equipment?
What are the potential risks of modifying upholstery welding equipment? Safety precautions are crucial to address these risks. Cost comparison and regulatory compliance must also be considered when customizing equipment to ensure optimal performance and adherence to industry standards.
Are There Specific Safety Considerations When Using Customized Upholstery Welding Equipment?
When using customized upholstery welding equipment, specific safety precautions must be observed. This includes thorough equipment maintenance, ensuring material compatibility, and employing proper welding techniques. These measures are critical for preventing accidents and ensuring successful project execution.
How Does the Cost of Customizing Upholstery Welding Equipment Compare to Purchasing Standard Equipment?
When considering the cost comparison of customizing upholstery welding equipment versus purchasing standard equipment, it’s important to weigh the upfront investment against long-term performance gains. Customized equipment may offer tailored features, but also requires careful financial assessment.
Are There Any Specific Regulations or Standards to Consider When Modifying Upholstery Welding Equipment for Unique Projects?
When modifying equipment, regulatory compliance is crucial. Equipment modifications should adhere to industry standards and safety regulations to ensure compliance. Understanding these standards is essential in customizing upholstery welding equipment for unique projects.
Conclusion
In conclusion, customized upholstery welding equipment plays a crucial role in meeting the unique needs of various projects. By carefully considering key modifications and adapting tools and equipment, tailored solutions can be achieved for specific welding projects.
The advantages of customized equipment are evident in the successful completion of diverse and complex upholstery welding tasks.
How can tailored solutions in welding equipment revolutionize the efficiency and precision of future projects?
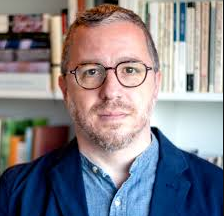
Dillon Hince, an expert in the realm of upholstery welding, brings a wealth of knowledge and experience to the craft. As the driving force behind nodpu.com, Dillon combines a passion for precision and creativity, offering unique insights into the art of seamlessly melding fabrics and materials. With a commitment to excellence, Dillon Hince is your go-to resource for innovative upholstery welding techniques, transforming ordinary pieces into extraordinary works of functional art.