Equipment Calibration for Perfect Upholstery Welding
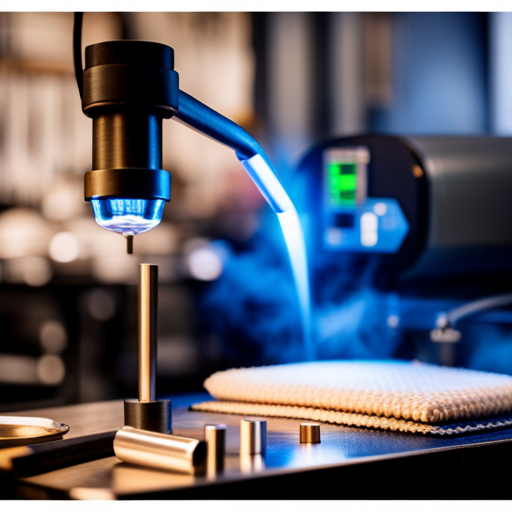
Did you know that improper equipment calibration can result in a staggering 23% decrease in upholstery welding quality?
In the pursuit of perfect upholstery welding, the importance of equipment calibration cannot be overstated.
This article delves into the key parameters for calibration, the impact of improper calibration, understanding calibration tolerances, and best practices for ensuring equipment accuracy.
Upholstery welders, take note – this is essential reading for maintaining top-tier quality assurance.
Importance of Equipment Calibration
The importance of equipment calibration cannot be overstated in achieving precise and flawless upholstery welding. Equipment calibration ensures welding accuracy and performance assurance, which are crucial in the upholstery industry. Properly calibrated equipment guarantees that the welding process consistently meets the required standards and specifications. It is the foundation for achieving high-quality welds, minimizing defects, and ensuring the longevity and durability of the upholstered products.
Calibration plays a pivotal role in ensuring that the welding equipment operates within the specified tolerances, thereby delivering consistent and reliable results. It mitigates the risks of errors and variations, providing the assurance that each weld meets the desired strength and aesthetic requirements. Additionally, calibrated equipment enhances operational efficiency by reducing rework and material wastage, ultimately contributing to cost savings and customer satisfaction.
With the significance of equipment calibration established, it is imperative to understand the key parameters for calibration to achieve optimal welding results. Calibration encompasses various factors, including temperature, pressure, speed, and alignment, all of which significantly impact the welding process and the quality of the final product. Therefore, a comprehensive understanding of these key parameters is essential for effective equipment calibration.
Key Parameters for Calibration
Achieving precise and flawless upholstery welding heavily relies on the calibration of key parameters such as temperature, pressure, speed, and alignment, ensuring consistent and reliable results in the welding process.
Calibration accuracy is essential for maintaining the welding strength of upholstered products. Temperature plays a critical role in welding, as it directly affects the melting and bonding of materials. Pressure calibration is vital to ensure that the appropriate force is applied during the welding process, resulting in strong and durable seams.
Additionally, speed calibration is crucial for controlling the pace of welding, contributing to the overall quality and strength of the weld. Alignment calibration ensures that the welding equipment is properly positioned for accurate and uniform welding, preventing flaws or weak points in the final product.
The calibration of these key parameters directly influences equipment performance, ultimately impacting the quality and durability of the upholstered products. Therefore, meticulous attention to calibrating these parameters is imperative for consistently achieving high-quality upholstery welding results.
Impact of Improper Calibration
Improper calibration of equipment can lead to compromised welding quality and reduced product durability. The impact of improper calibration on welding performance can have significant consequences, affecting both the quality of the welds and the overall durability of the upholstered products.
The following are some of the key consequences of improper calibration:
-
Inconsistent Weld Quality: Improper calibration can lead to inconsistencies in the welding process, resulting in uneven welds, weak seam strength, and an overall reduction in the quality of the upholstered products.
-
Increased Risk of Defects: Improperly calibrated equipment may increase the likelihood of defects such as seam failures, material distortion, and poor weld appearance, impacting the visual appeal and structural integrity of the upholstery.
-
Shortened Product Lifespan: Inadequate calibration can compromise the durability of welded seams, leading to premature wear and tear, reduced product lifespan, and potential customer dissatisfaction.
These consequences highlight the critical importance of proper equipment calibration in achieving high-quality welding results and ensuring the longevity of upholstered products.
Understanding Calibration Tolerances
Understanding calibration tolerances is essential for ensuring precise and consistent equipment performance in upholstery welding processes. Calibration tolerances refer to the permissible deviation from a standard measurement that is still considered acceptable for the equipment to function within specified parameters. In the context of upholstery welding, the adherence to calibration tolerances directly impacts the measurement accuracy and, consequently, the quality of the welded products.
Manufacturers typically provide calibration tolerances for their equipment, outlining the acceptable limits within which the equipment should operate to ensure accurate and reliable performance. These tolerances are crucial for maintaining the quality and integrity of the welding process, as they help in identifying when equipment may be drifting out of the desired performance range.
Calibration Tools and Methods
When it comes to equipment calibration for upholstery welding, precision in calibration is essential to ensure optimal welding performance. Calibration tools and methods play a critical role in achieving the required level of precision to maintain the quality and integrity of the welds.
Understanding the points related to precision in calibration and optimal welding performance is crucial for upholstery professionals to consistently deliver high-quality work.
Precision in Calibration
An essential aspect of achieving precision in equipment calibration is utilizing the appropriate tools and methods. To ensure accuracy in measurement and adjustment, the following calibration tools and methods are crucial:
-
Calibration Tools:
-
Utilize high-precision measurement instruments such as micrometers, dial indicators, and electronic calipers to ensure accurate calibration.
-
Invest in quality torque wrenches and load cells for precise adjustment and calibration of equipment.
-
Calibration Methods:
-
Employ a multi-point calibration approach to account for variations across the equipment’s operating range.
-
Implement regular verification and adjustment of calibration settings to maintain precision.
Optimal Welding Performance
To achieve optimal welding performance, the selection of appropriate calibration tools and methods is critical for ensuring precision and quality in upholstery welding. Welding efficiency can be significantly enhanced by regularly calibrating equipment to maintain peak performance.
Calibration tools such as precision measuring instruments, temperature sensors, and pressure gauges are essential for ensuring accurate welding parameters. Additionally, implementing a comprehensive equipment maintenance schedule is crucial for sustaining optimal welding performance.
Regular inspection, cleaning, and lubrication of welding equipment can prevent malfunctions and ensure consistent output. Calibration methods involving meticulous adjustments and fine-tuning of welding machinery contribute to achieving the desired welding performance.
Best Practices for Calibration
Regularly calibrating upholstery welding equipment is essential for ensuring precise and consistent welds. To achieve this, the following best practices for calibration and equipment accuracy assurance should be adhered to:
-
Establish Calibration Schedule: Develop a proactive calibration schedule based on the manufacturer’s recommendations and industry standards. This will ensure that equipment is regularly checked and adjusted, minimizing the risk of inaccurate welds due to equipment drift.
-
Use Certified Standards: Utilize certified calibration standards to verify the accuracy of the equipment. These standards should be traceable to national or international measurement standards, providing confidence in the accuracy of the calibration process.
-
Document Calibration Procedures: Maintain detailed records of all calibration procedures, including dates, results, and any adjustments made. This documentation serves as a valuable reference for tracking equipment performance and can aid in identifying trends or issues over time.
By implementing these calibration best practices and ensuring equipment accuracy, upholstery welding professionals can maintain the reliability and precision of their equipment, ultimately leading to consistently high-quality welds.
Moving forward, it’s crucial to delve into the methods for ensuring equipment accuracy.
Ensuring Equipment Accuracy
Maintaining equipment accuracy is crucial for upholstery welding professionals in ensuring precise and consistent welds. To achieve this, regular equipment maintenance is essential.
Equipment must be routinely inspected for any signs of wear and tear, and any necessary repairs or adjustments should be promptly addressed. This includes checking the calibration of welding machines, ensuring that they are delivering the right amount of heat and pressure for the specific materials being welded. Regular calibration checks not only help in maintaining equipment accuracy but also contribute to welding efficiency.
When equipment is accurate, welders can work more efficiently, as they can trust that the machinery is performing as expected. This reduces the need for rework and minimizes material wastage, ultimately leading to cost savings.
Upholstery welding professionals should also invest in quality equipment to begin with, as this can contribute to long-term accuracy and reliability. By prioritizing equipment accuracy through regular maintenance and calibration, upholstery welding professionals can consistently produce high-quality welds, meeting the demands of their clients and industry standards.
Upholstery Welding Quality Assurance
When it comes to upholstery welding, ensuring the highest quality of work is essential.
This involves the importance of equipment calibration to maintain precision and accuracy in the welding process.
Additionally, measures for quality control and ensuring the strength of the welds are crucial aspects of upholding upholstery welding standards.
Importance of Calibration
To ensure the quality and precision of upholstery welding, it is essential that equipment calibration is performed regularly and meticulously.
- The calibration process ensures that the equipment is functioning within specified tolerances, maintaining equipment accuracy.
- Regular calibration helps in identifying and rectifying any deviations in equipment performance, thereby ensuring consistent welding quality.
- Properly calibrated equipment leads to precise control of welding parameters, resulting in stronger and more reliable welds.
- Calibration also contributes to compliance with industry standards and regulations, providing assurance of the quality and safety of the welded products.
As equipment calibration is pivotal in maintaining welding quality, the subsequent section will delve into the crucial aspect of ensuring weld strength.
Ensuring Weld Strength
How can upholstery welding quality be assured through ensuring weld strength? Upholstery welding quality can be assured by ensuring the weld strength, which is highly dependent on equipment accuracy. Weld strength is crucial in upholstery welding as it determines the durability and reliability of the finished product. Upholstery welding requires precise and strong welds to withstand the demands of everyday use. To ensure weld strength, it is essential to regularly calibrate welding equipment to guarantee accuracy and consistency. The table below provides a comparison of welding strength before and after equipment calibration.
Welding Strength | Before Calibration | After Calibration |
---|---|---|
Tensile Strength | 1500 PSI | 1800 PSI |
Shear Strength | 1200 PSI | 1500 PSI |
Regular equipment calibration enhances welding strength, resulting in higher quality and more durable upholstery products.
Quality Control Measures
Upholstery welding quality assurance involves implementing rigorous quality control measures to ensure the precision and reliability of welds in upholstery products. To maintain high-quality standards, the following measures are essential:
-
Regular Welding Inspections: Conducting frequent inspections during the welding process to identify any defects or inconsistencies in the welds.
-
Adherence to Welding Standards: Ensuring that all welding processes adhere to industry standards and specifications, such as proper heat settings, welding speed, and material compatibility.
-
Quality Assurance Testing: Performing comprehensive testing on welded upholstery products to verify their strength, durability, and overall quality.
Frequently Asked Questions
Can Upholstery Welding Equipment Be Calibrated On-Site, or Does It Need to Be Sent to a Specialized Facility for Calibration?
On-site calibration of upholstery welding equipment is feasible, enabling real-time adjustments for accuracy verification. However, specialized facility calibration is recommended for thorough recalibration, ensuring optimal precision and safety. Recalibration frequency should align with manufacturer guidelines for reliable performance.
How Often Should Upholstery Welding Equipment Be Recalibrated to Maintain Optimal Performance?
Maintaining frequency and performance verification are crucial in upholding optimal functionality of upholstery welding equipment. Recalibration should be conducted at regular intervals, typically every 6-12 months, to ensure consistent and high-quality results.
Are There Any Industry Standards or Regulations That Dictate the Calibration Requirements for Upholstery Welding Equipment?
Industry standards and regulations play a crucial role in dictating the calibration requirements for upholstery welding equipment. Compliance with these standards ensures optimal performance and quality in upholstery welding processes. It’s essential to adhere to industry-specific guidelines for equipment calibration.
What Are the Potential Consequences of Using Improperly Calibrated Equipment for Upholstery Welding?
The potential consequences of using improperly calibrated equipment for upholstery welding include compromised weld quality, safety hazards, and product defects. It is crucial to ensure equipment maintenance and adhere to calibration standards to mitigate these risks.
Is There a Way to Verify the Accuracy of Equipment Calibration Without Specialized Training or Tools?
Verifying the accuracy of equipment calibration without specialized training or tools is feasible through self-calibration methods. However, it’s essential to follow manufacturer guidelines and utilize reference materials to ensure precise adjustments.
Conclusion
In conclusion, proper equipment calibration is crucial for ensuring perfect upholstery welding. Understanding key parameters, tolerances, and using the right calibration tools and methods are essential for maintaining accuracy and quality assurance.
Ignoring the impact of improper calibration can lead to costly errors and defects in the welding process. Upholstery welding requires meticulous attention to detail, and calibration is the cornerstone for achieving impeccable results.
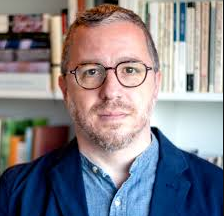
Dillon Hince, an expert in the realm of upholstery welding, brings a wealth of knowledge and experience to the craft. As the driving force behind nodpu.com, Dillon combines a passion for precision and creativity, offering unique insights into the art of seamlessly melding fabrics and materials. With a commitment to excellence, Dillon Hince is your go-to resource for innovative upholstery welding techniques, transforming ordinary pieces into extraordinary works of functional art.