Innovations in Upholstery Welding Equipment
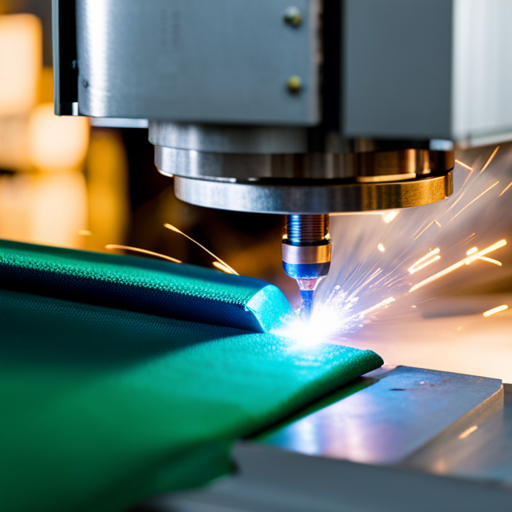
As the demands for high-quality and durable upholstery continue to rise, the innovations in upholstery welding equipment have become paramount.
Just as a skilled artisan meticulously weaves together fabric to create a masterpiece, advancements in ultrasonic, laser, and high-frequency welding technologies have revolutionized the upholstery industry.
This article explores the latest developments in automated, multi-functional welding equipment, and the integration of smart control systems, shaping the future of upholstery manufacturing.
Advancements in Ultrasonic Welding Technology
Advancements in ultrasonic welding technology have revolutionized the upholstery industry by enabling precise and efficient bonding of materials. This cutting-edge technology has significantly improved material compatibility, allowing for the seamless joining of a wide range of materials, including fabrics, foams, and plastics. Traditional methods often struggled with bonding dissimilar materials, but ultrasonic welding has overcome these challenges, expanding the possibilities for innovative designs and improved product durability.
Moreover, the environmental impact of ultrasonic welding is a key advantage. Unlike traditional adhesives or solvent-based bonding methods, ultrasonic welding does not require consumables such as adhesives, solvents, or fasteners. This results in a reduction of hazardous waste and emissions, aligning with the growing focus on sustainable and eco-friendly manufacturing practices. Additionally, the energy-efficient nature of ultrasonic welding further contributes to its environmental benefits, as it requires lower energy consumption compared to other bonding techniques.
Integration of Laser Welding Systems
The integration of laser welding systems in upholstery manufacturing offers precise seam welding, resulting in enhanced productivity and improved product quality.
Laser welding technology enables manufacturers to achieve intricate and detailed welds, ensuring strong and durable seams in upholstered products.
This innovation is revolutionizing the upholstery industry by providing a reliable and efficient method for achieving high-quality welds in a wide range of upholstery applications.
Precision in Seam Welding
A growing number of upholstery manufacturers are integrating laser welding systems to achieve unprecedented precision in seam welding. This integration has led to significant advancements in welding process optimization and quality control.
Laser welding systems offer precise control over the energy input and heat-affected zones, resulting in superior seam quality and consistency. Additionally, the automation and robotics integration in seam welding have further enhanced the precision and repeatability of the process.
Seam welding automation ensures consistent welding parameters, reducing the likelihood of human error and enhancing overall product quality. Robotics integration allows for intricate seam welding patterns and complex designs to be executed with exceptional accuracy.
The combination of laser welding systems and automation technologies has revolutionized the upholstery manufacturing industry, setting new benchmarks for precision in seam welding.
Enhanced Productivity and Quality
With the integration of laser welding systems, upholstery manufacturers have experienced enhanced productivity and improved product quality. The precision and speed of laser welding have significantly increased the efficiency of the upholstery manufacturing process. This technology allows for seamless and precise welding, resulting in stronger and more durable seams.
Moreover, laser welding systems contribute to improved safety in the workplace by minimizing the risks associated with traditional welding methods. Additionally, manufacturers have incorporated ergonomic design into these systems, ensuring that operators can work comfortably and efficiently.
The integration of laser welding systems not only enhances productivity but also elevates the overall quality of upholstered products, meeting the demands for durability and aesthetic appeal in the market.
Development of High-Frequency Welding Machines
The development of high-frequency welding machines has brought about increased welding precision, allowing for the creation of stronger and more durable upholstery products.
Furthermore, these machines have significantly enhanced production efficiency, leading to reduced manufacturing time and costs.
Additionally, high-frequency welding machines offer distinct advantages over traditional welding methods, such as the ability to weld various materials and the production of seamless seams, further revolutionizing the upholstery industry.
Increased Welding Precision
An increasing number of upholstery manufacturers are adopting high-frequency welding machines to achieve greater precision in their welding processes. This trend is driven by the need for welding automation and robotic welding to enhance efficiency and consistency.
The use of high-frequency welding machines enables upholstery manufacturers to improve welding accuracy and achieve higher quality seams. This technology advancement has revolutionized the upholstery industry by allowing for intricate and precise welds, resulting in superior finished products.
The high-frequency welding machines offer greater control and uniformity, ensuring that every weld meets the highest standards. As a result, manufacturers can produce upholstery with impeccable seams, meeting the demands of discerning customers and elevating the overall quality of their products.
Enhanced Production Efficiency
Upholstery manufacturers are revolutionizing their production processes through the development and integration of high-frequency welding machines. These machines enhance efficiency and precision in welding operations. The use of high-frequency welding machines has resulted in significant improvements in weld strength, ensuring that upholstered products meet high-quality standards.
Furthermore, the implementation of these advanced machines has led to substantial cost savings in production. The precise control and rapid welding capabilities of high-frequency machines reduce material waste and contribute to efficient resource utilization. This ultimately leads to cost-effective manufacturing processes.
This heightened production efficiency aligns with the industry’s increasing demand for high-quality upholstered products while maintaining cost-effectiveness. The integration of high-frequency welding machines offers upholstery manufacturers distinct advantages over traditional methods. It positions them to effectively meet evolving market demands.
Advantages Over Traditional Methods
Revolutionizing their production processes through the development and integration of high-frequency welding machines has enabled upholstery manufacturers to achieve significant improvements in efficiency and precision, ensuring enhanced weld strength and substantial cost savings.
The advantages of high-frequency welding machines over traditional methods are as follows:
-
Improved Durability:
High-frequency welding creates stronger and more durable seams, ensuring the longevity and robustness of upholstered products. -
Enhanced Precision:
These machines offer precise control over the welding process, resulting in consistent and high-quality seams, thereby reducing material wastage and rework. -
Substantial Cost Savings:
Application of Hot Air and Hot Wedge Welding Techniques
The application of hot air and hot wedge welding techniques revolutionizes the efficiency and precision of joining upholstery materials. When comparing hot air vs. hot wedge welding techniques, both offer distinct advantages. Hot air welding is versatile and suitable for a wide range of materials, including vinyl, PVC, and certain types of fabric. On the other hand, hot wedge welding provides exceptional control and is particularly effective for thicker materials and seams.
Welding Technique | Advantages |
---|---|
Hot Air | Versatile, suitable for various materials |
Hot Wedge | Exceptional control, effective for thicker materials |
In the upholstery industry, hot air welding finds widespread applications in manufacturing automobile upholstery, outdoor furniture, and medical furniture. It is also used in creating tarpaulins, tents, and inflatable products. Hot wedge welding, with its precise control, is commonly utilized in manufacturing truck covers, industrial curtains, and other heavy-duty fabric products. Both techniques offer enhanced seam strength, durability, and a seamless appearance, making them indispensable in modern upholstery manufacturing.
Implementation of Automated Welding Processes
Automated welding processes have significantly enhanced the efficiency and precision of joining upholstery materials, providing manufacturers with a quantifiable increase in production output and seam quality. This implementation has been made possible through the use of advanced automated welding robots and the integration of Industry 4.0 principles into upholstery manufacturing processes.
The following points highlight the key aspects of the implementation of automated welding processes:
-
Increased Efficiency: Automated welding robots have accelerated the welding process, reducing cycle times and increasing the overall efficiency of upholstery production lines.
-
Enhanced Precision: The use of automated welding processes ensures consistent and precise seam quality, minimizing material wastage and rework.
-
Industry 4.0 Integration: Integration of automated welding processes into the framework of Industry 4.0 enables real-time monitoring and data-driven decision-making, leading to optimized production workflows and predictive maintenance strategies.
The implementation of automated welding processes represents a significant leap forward in the upholstery manufacturing industry, delivering improved productivity, quality, and adaptability to the demands of modern production environments.
Introduction of Multi-functional Welding Equipment
Multi-functional welding equipment has been introduced to enhance the versatility and capabilities of upholstery manufacturing processes. Upholstery manufacturers are now able to meet industry demands more effectively by utilizing this advanced equipment. These welding machines offer customized solutions for a wide range of upholstery materials, including leather, fabric, and synthetic materials.
The introduction of multi-functional welding equipment has significantly improved the efficiency and precision of welding processes, enabling manufacturers to cater to diverse customer requirements with ease. The ability to switch between different welding techniques, such as hot air, hot wedge, and hot pulse, within a single machine provides unprecedented flexibility in upholstery production.
This versatility allows manufacturers to streamline their operations and adapt to changing market needs without the need for multiple specialized machines. As a result, upholstery manufacturers can now optimize their production processes, reduce downtime, and enhance overall productivity. The introduction of multi-functional welding equipment represents a significant advancement in the upholstery manufacturing industry, empowering manufacturers to deliver high-quality products while remaining agile in response to evolving market demands.
Incorporation of Smart Control and Monitoring Systems
Utilizing advanced smart control and monitoring systems enhances the precision and efficiency of welding processes, providing upholstery manufacturers with real-time insights and adjustments to ensure seamless production operations.
-
Enhanced Precision: Smart control systems enable precise control over welding parameters, ensuring consistent and high-quality welds across various upholstery materials. Real-time monitoring allows for immediate adjustments to maintain optimal welding conditions, minimizing defects and rework.
-
Operational Efficiency: Integration of smart control and monitoring systems streamlines the welding process, reducing setup time and increasing overall productivity. Manufacturers can remotely monitor and manage multiple welding stations from a centralized control interface, optimizing resource allocation and minimizing downtime.
-
Data-Driven Optimization: Real-time monitoring provides valuable data on welding performance and equipment status, enabling predictive maintenance scheduling and proactive troubleshooting. By leveraging this data, manufacturers can continuously improve welding processes, reduce waste, and enhance overall operational efficiency.
The incorporation of smart control and monitoring systems not only elevates the quality and consistency of upholstery welding but also empowers manufacturers with actionable insights to drive continuous improvement and operational excellence.
Frequently Asked Questions
What Are the Key Factors to Consider When Choosing the Right Upholstery Welding Equipment for a Specific Application?
When choosing upholstery welding equipment for a specific application, key features, performance standards, and cost efficiency are crucial. Specialized applications require equipment tailored to their unique requirements, ensuring optimal results and productivity.
How Do Upholstery Welding Equipment Manufacturers Ensure the Durability and Longevity of Their Products?
Upholstery welding equipment manufacturers ensure product durability and longevity through rigorous durability testing, high material quality, and adherence to longevity standards. This is achieved through continuous product development and engineering advancements, ensuring customer satisfaction.
What Are the Environmental Impacts of Using Different Types of Upholstery Welding Techniques and Equipment?
The environmental impacts of using different types of upholstery welding techniques and equipment vary. Factors such as energy consumption, emissions, and material waste play a significant role. Evaluating these aspects is crucial for sustainable manufacturing and minimizing environmental effects.
Can Upholstery Welding Equipment Be Customized to Meet Specific Industry Standards and Regulations?
Customization options for upholstery welding equipment allow for adherence to specific industry standards and regulatory compliance. This tailored approach ensures specialized applications meet the requirements of various sectors, offering flexibility and precision in welding processes.
How Do Advancements in Upholstery Welding Equipment Contribute to Overall Efficiency and Productivity in the Manufacturing Process?
Advancements in upholstery welding equipment significantly enhance efficiency and productivity in the manufacturing process. Application-specific considerations and customization to industry standards ensure tailored solutions, streamlining operations and ultimately contributing to improved output and profitability.
Conclusion
In conclusion, the advancements in upholstery welding equipment symbolize the evolution of technology and innovation in the manufacturing industry.
The integration of cutting-edge welding technologies, automated processes, and smart control systems represents the relentless pursuit of efficiency, precision, and quality.
These innovations not only improve productivity and cost-effectiveness but also signify the industry’s commitment to staying at the forefront of technological progress.
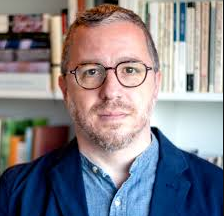
Dillon Hince, an expert in the realm of upholstery welding, brings a wealth of knowledge and experience to the craft. As the driving force behind nodpu.com, Dillon combines a passion for precision and creativity, offering unique insights into the art of seamlessly melding fabrics and materials. With a commitment to excellence, Dillon Hince is your go-to resource for innovative upholstery welding techniques, transforming ordinary pieces into extraordinary works of functional art.