Precision and Accuracy in Upholstery Welding

In the craft of upholstery welding, the art of precision and accuracy holds paramount significance.
Ensuring the seamless fusion of materials not only enhances the durability of the final product but also elevates its aesthetic appeal.
Employing advanced technologies and techniques, upholsterers strive to achieve impeccable precision, thereby setting new standards for customer satisfaction.
This article delves into the pivotal role of precision and accuracy in upholstery welding, shedding light on the latest advancements in this specialized field.
Importance of Precision in Welding
One must recognize the crucial importance of precision in upholstery welding for ensuring structural integrity and aesthetic appeal. Upholstery welding quality is directly impacted by the precision techniques employed during the welding process. Precision in welding is essential for creating strong and durable seams that can withstand the stresses of everyday use. Without precision, the structural integrity of the upholstered furniture may be compromised, leading to potential safety hazards and a decrease in overall product quality.
Precision techniques in welding also play a significant role in the aesthetic appeal of the finished upholstery. Clean and precise welds contribute to a visually appealing end product, enhancing the overall value and desirability of the furniture piece. Conversely, sloppy or imprecise welding can detract from the visual appeal, giving the impression of poor craftsmanship and subpar quality.
Impact on Product Durability
Ensuring precision and accuracy in upholstery welding has a significant impact on the product durability, as it directly influences the strength and resilience of the welded seams. The following points highlight the specific ways in which precision and accuracy in welding techniques contribute to product longevity:
-
Enhanced Structural Integrity: Precise welding techniques ensure that the seams are strong and durable, thereby preventing premature wear and tear of the upholstery. This, in turn, improves the overall longevity of the product.
-
Resistance to Stress and Strain: Accurate welding minimizes the likelihood of seam failure under stress, increasing the product’s ability to withstand regular usage and maintain its structural integrity over time.
-
Reduction of Potential Weak Points: By maintaining precision in welding, the creation of weak points in the upholstery is minimized, thus enhancing the product’s resilience and longevity.
The meticulous application of welding techniques significantly impacts the durability of upholstered products, ensuring they can withstand the rigors of everyday use.
This, in turn, sets the stage for discussing the importance of aesthetics in upholstery welding.
Aesthetics in Upholstery Welding
In upholstery welding, achieving seamless welds is crucial for enhancing the overall aesthetics of the finished product.
The choice of materials also plays a significant role in determining the visual appeal of the welds.
Attention to detail in the welding process is essential for ensuring that the final upholstery product meets high aesthetic standards.
Seamless Welds for Aesthetics
To achieve seamless welds for aesthetics in upholstery welding, it is essential to prioritize meticulous attention to detail and precision throughout the welding process. This ensures a flawless and visually appealing finish that elevates the overall quality of the upholstered piece.
The following key factors contribute to achieving seamless welds for aesthetics:
-
Material Preparation: Properly preparing the materials before welding, including cleaning and smoothing the surfaces, is crucial for achieving a seamless finish.
-
Optimal Welding Techniques: Employing the most suitable welding techniques, such as high-frequency welding or hot air welding, helps to create seamless and aesthetically pleasing welds.
-
Quality Control Inspection: Implementing rigorous quality control measures throughout the welding process guarantees that each weld meets the highest standards of visual appeal and structural integrity.
Choosing the Right Materials
Achieving seamless welds for aesthetics in upholstery welding relies on meticulous attention to detail and precision throughout the welding process, particularly in choosing the right materials.
When choosing materials for upholstery welding, it is essential to consider factors such as material compatibility and welding safety precautions. Selecting the right materials involves evaluating their suitability for the specific welding technique and ensuring they meet the required industry standards.
Additionally, welding equipment selection plays a crucial role in achieving the desired aesthetic outcomes. The equipment must be capable of providing the necessary precision and control to create seamless welds.
Importance of Attention
Meticulous attention to detail and precision throughout the upholstery welding process is imperative to achieve the desired aesthetic outcomes, especially in ensuring seamless welds. Achieving high accuracy in upholstery welding involves the following:
-
Material alignment: Ensuring precise alignment of the materials before welding is crucial in creating a visually appealing and seamless finish.
-
Consistent heat control: Maintaining a consistent and controlled heat application during the welding process is essential for achieving uniform and aesthetically pleasing welds.
-
Seam finishing: Paying close attention to the finishing of seams and edges is vital to ensure a clean and polished appearance, reflecting the precision and accuracy of the welding process.
Attention to these details not only enhances the visual appeal of the upholstered piece but also reflects the craftsmanship and expertise of the welder. This attention to detail sets the stage for achieving high accuracy in upholstery welding.
Achieving High Accuracy
To ensure high accuracy in upholstery welding, it is essential to implement precise measurement techniques and utilize advanced welding equipment. Welding techniques such as TIG (Tungsten Inert Gas) and MIG (Metal Inert Gas) require precision tools and equipment to achieve the desired accuracy in welds.
Utilizing specialized welding machines with advanced controls and fine-tuned settings is crucial in achieving the level of accuracy required for upholstery welding. Furthermore, quality control and inspection standards play a pivotal role in ensuring high accuracy.
Implementing rigorous quality control measures, including thorough inspections at various stages of the welding process, helps to identify and rectify any deviations from the required accuracy levels. This involves the use of precision measuring instruments and adherence to strict inspection protocols to maintain consistency and accuracy in the welding process.
Latest Technologies for Precision
The latest technologies for precision upholstery welding encompass advanced welding equipment and cutting-edge measurement techniques. Upholstery welding has seen significant advancements due to the integration of welding automation and advanced robotics. These technologies have revolutionized the welding process, allowing for highly precise and consistent welds on upholstery materials.
Laser welding has also emerged as a game-changing technology in the upholstery welding industry. Its ability to produce fine, accurate welds with minimal heat-affected zones has made it a preferred choice for achieving precision in upholstery welding.
Additionally, ultrasonic technology has gained prominence for its capability to weld intricate patterns with utmost accuracy, especially in delicate upholstery applications.
These latest technologies not only ensure precision but also enhance efficiency and productivity in upholstery welding processes. As the demand for high-quality upholstered products continues to rise, these innovative technologies play a crucial role in meeting the industry’s need for precision and accuracy.
Techniques for Accurate Welding
In the realm of upholstery welding, achieving precision and accuracy is paramount. Utilizing specific techniques can greatly impact the quality of the weld, ensuring a seamless and durable result.
To achieve this, welders must adhere to welding precision tips and employ strategies that guarantee accurate welds.
Welding Precision Tips
For achieving accurate upholstery welding, one must carefully master the precision techniques. Upholstery welding requires attention to detail to ensure the precision and aesthetics of the final product. Here are three essential tips for achieving accurate and precise welding:
-
Proper Alignment: Ensure that the pieces to be welded are accurately aligned before starting the welding process. Proper alignment is crucial for achieving precise and clean welds, especially in upholstery where visual appeal is paramount.
-
Consistent Heat Control: Maintain a consistent and appropriate heat level during the welding process. Fluctuations in heat can lead to inconsistent welds, affecting both the strength and aesthetics of the weld.
-
Meticulous Execution: Pay close attention to the welding process, ensuring steady and even movements to create uniform and aesthetically pleasing welds.
Mastering these precision techniques is essential for achieving high-quality upholstery welding results.
Ensuring Accurate Welds
To achieve accurate and precise upholstery welding, mastering techniques such as proper alignment, consistent heat control, and meticulous execution is essential. Welding techniques play a pivotal role in ensuring the accuracy of welds. Quality control measures should be implemented to guarantee that the welded joints meet the required standards. Below is a table summarizing essential welding techniques and quality control measures:
Welding Techniques | Quality Control |
---|---|
Proper Alignment | Visual Inspection |
Consistent Heat Control | Non-destructive testing |
Meticulous Execution | Dimensional checks |
Joint Preparation | Metallurgical analysis |
Filler Material Selection | Documentation and record-keeping |
Significance for Customer Satisfaction
Customer satisfaction significantly depends on the consistent precision and accuracy of upholstery welding. Upholstery plays a crucial role in the overall aesthetics and functionality of furniture, and the quality of welding directly impacts the durability and visual appeal of the finished product.
The significance of precision and accuracy in upholstery welding for customer satisfaction is evident through various aspects:
-
Customer feedback: Upholstery welding directly influences customer feedback. The quality of welds reflects the overall craftsmanship and attention to detail, which are key factors that customers consider when evaluating the value and quality of the furniture they purchase.
-
Weld quality: Precision and accuracy in welding ensure the structural integrity of the furniture. High-quality welds contribute to the longevity of the upholstery, reducing the likelihood of premature wear and tear. This, in turn, enhances customer satisfaction by providing durable and reliable furniture.
-
Aesthetics: Accurate and precise welding contributes to the visual appeal of the furniture. Clean, seamless welds enhance the overall appearance, contributing to a more polished and professional finish that is likely to impress customers, thereby positively impacting their satisfaction with the product.
Frequently Asked Questions
Can Welding Precision Affect the Overall Cost of Upholstery Products?
Welding precision significantly impacts upholstery product costs as it affects material usage and production time. Market demand for high-quality, precise welding further amplifies this impact, making precision a critical factor in cost management and market competitiveness.
How Does Welding Accuracy Impact the Environmental Sustainability of Upholstery Materials?
Welding accuracy significantly impacts the environmental sustainability of upholstery materials. Poor precision can lead to material waste and increased energy consumption. Moreover, it can compromise the quality of materials, affecting their recyclability and overall environmental impact.
Are There Any Specific Safety Considerations Related to Achieving High Accuracy in Upholstery Welding?
Safety precautions, welding techniques, equipment maintenance, and workplace environment are crucial aspects related to achieving high accuracy in upholstery welding. Skilled labor and certification requirements play a vital role in ensuring the safety and quality of welding operations.
What Role Does Precision Welding Play in the Customization of Upholstery Products for Individual Customers?
Customization in upholstery products is pivotal for customer satisfaction. Precision welding plays a crucial role in achieving the exact specifications and details desired by individual customers. It ensures the high-quality, tailored finish that enhances customer satisfaction.
How Do Advancements in Welding Technology Specifically Benefit the Upholstery Industry?
Advancements in welding technology bring significant benefits to the upholstery industry. These include improved efficiency, enhanced precision, and expanded design possibilities. Technology advancements also enable better material compatibility, reducing production time and enhancing overall product quality.
Conclusion
In conclusion, precision and accuracy in upholstery welding are crucial for product durability, aesthetics, and customer satisfaction.
The use of latest technologies and techniques for achieving high accuracy is essential in ensuring the quality of welding.
Upholstery welding is like a delicate dance, where each movement must be exact and coordinated to create a flawless finished product.
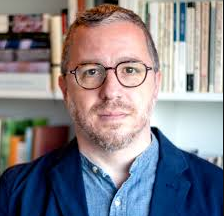
Dillon Hince, an expert in the realm of upholstery welding, brings a wealth of knowledge and experience to the craft. As the driving force behind nodpu.com, Dillon combines a passion for precision and creativity, offering unique insights into the art of seamlessly melding fabrics and materials. With a commitment to excellence, Dillon Hince is your go-to resource for innovative upholstery welding techniques, transforming ordinary pieces into extraordinary works of functional art.