Safety Practices in Upholstery Welding
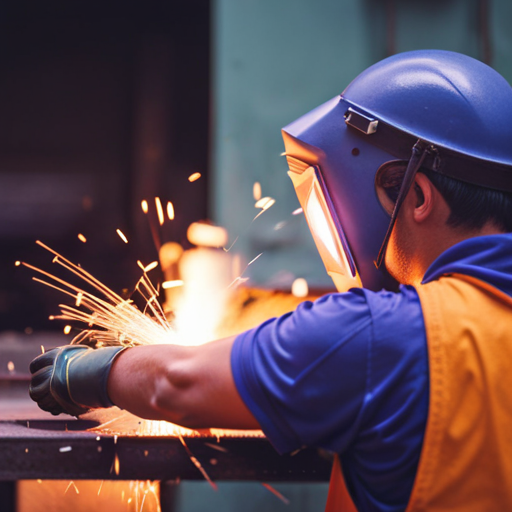
Discover the pivotal role of safety practices in upholstery welding, where precision meets potential hazards. Upholstery welding demands meticulous attention to detail and an unwavering commitment to safety.
This article provides essential insights into ventilation requirements, personal protective equipment, fire prevention measures, equipment maintenance, training protocols, and emergency response planning.
Uphold the highest standards of safety and efficiency in upholstery welding with the expert guidance outlined in this comprehensive piece.
Ventilation Requirements
While conducting upholstery welding, it is essential to ensure adequate ventilation requirements are met to safeguard the health and safety of workers. Upholstery welding releases fumes and airborne particles that can compromise indoor air quality and pose health risks if inhaled.
A well-designed ventilation system is crucial to mitigate these hazards. The ventilation system should effectively capture and remove airborne contaminants from the welding area, preventing their dispersion into the surrounding workspace. Additionally, the ventilation system should incorporate filtration mechanisms to trap particulate matter and fumes, thereby improving indoor air quality.
Properly maintained ventilation systems not only protect workers from immediate health concerns but also contribute to a healthier work environment in the long term. Adequate ventilation also plays a role in regulating temperature and humidity, creating a comfortable workspace.
Regular assessments of the ventilation system’s effectiveness and indoor air quality should be conducted to ensure that it meets safety standards. By prioritizing ventilation requirements, upholstery welding businesses can uphold a safe and healthy environment for their workers.
Personal Protective Equipment (Ppe)
As upholstery welding poses several hazards, it is crucial to prioritize personal protective equipment (PPE) to ensure the safety of workers.
This discussion will focus on the essential PPE for eye protection, respiratory protection guidelines, and proper hand protection.
Understanding and implementing these PPE measures is vital for safeguarding the health and well-being of workers in upholstery welding environments.
PPE for Eye Protection
Utilizing proper eye protection is essential in upholstery welding to prevent potential eye injuries. Welding hazards such as intense light, sparks, and debris can cause significant harm if the eyes are left unprotected.
Safety goggles are a crucial form of eye protection as they shield the eyes from flying particles and debris. Additionally, they provide a barrier against harmful UV exposure, which can lead to welding flash burns and long-term eye damage.
When selecting safety goggles for upholstery welding, it is important to choose ones that are specifically designed for welding applications, ensuring they meet the necessary safety standards.
Respiratory Protection Guidelines
To ensure comprehensive safety in upholstery welding, it is imperative to adhere to respiratory protection guidelines as part of the personal protective equipment (PPE) protocol.
Respiratory protection involves the use of respirators to safeguard workers from inhaling harmful fumes, gases, and particulates generated during welding processes. Fit testing is crucial to ensure that respirators form a tight seal on the user’s face, minimizing the risk of contaminants entering the breathing zone.
Moreover, compliance with National Institute for Occupational Safety and Health (NIOSH) guidelines is essential to guarantee the appropriate filtration efficiency of respirators. Upholstery welders must select respirators with the suitable assigned protection factor and ensure proper maintenance and storage to optimize their performance.
Adhering to these respiratory protection guidelines is essential for safeguarding the health and well-being of upholstery welding personnel.
Proper Hand Protection
Continuing from the previous subtopic on respiratory protection guidelines, proper hand protection is crucial for safeguarding upholstery welding personnel from potential hazards. It is considered a crucial component of personal protective equipment (PPE).
Proper ergonomics is an important aspect of hand protection. Utilizing gloves that provide a snug fit without limiting dexterity is crucial. Ergonomically designed gloves reduce hand fatigue and improve comfort during prolonged welding tasks.
Another important consideration is welding technique. Selecting gloves with heat-resistant materials is imperative. This protects against burns and ensures a secure grip on welding tools, preventing accidents.
Adequate hand protection not only shields against burns, cuts, and abrasions but also enhances the overall safety and efficiency of upholstery welding operations.
Transitioning into the subsequent section about ‘fire prevention measures’, it is imperative to address the proactive measures essential for mitigating fire risks in upholstery welding environments.
Fire Prevention Measures
Implementing effective fire prevention measures is crucial in maintaining a safe working environment during upholstery welding processes. When it comes to welding equipment, it is essential to use only well-maintained and appropriate machinery to minimize the risk of fire. Regular inspection and maintenance of welding equipment can help identify potential fire hazards, such as faulty wiring or leaks, and prevent them from causing a fire.
Additionally, ensuring that hazardous materials, such as flammable upholstery fabrics or chemicals, are stored and handled carefully is crucial in fire prevention. Proper storage and handling procedures, including the use of designated storage areas and the implementation of spill containment measures, can significantly reduce the likelihood of fire incidents.
Transitioning into the subsequent section about ‘equipment maintenance and inspection’, regular maintenance and inspection of welding equipment not only contribute to fire prevention but also play a significant role in ensuring overall workplace safety.
Equipment Maintenance and Inspection
In ensuring workplace safety during upholstery welding, the maintenance and inspection of welding equipment are critical components to be addressed. Equipment safety is paramount in preventing accidents and ensuring the smooth functioning of welding operations. Regular inspection procedures should be implemented to identify and address any potential issues with the equipment.
The following are key aspects to consider in equipment maintenance and inspection:
-
Routine Maintenance: Establish a schedule for regular maintenance of welding equipment to ensure that all components are in good working condition. This includes checking power sources, cables, and connections for any signs of wear or damage.
-
Calibration and Testing: Regularly calibrate and test welding equipment to maintain accuracy and efficiency. This involves checking pressure gauges, verifying flow rates, and ensuring that safety mechanisms are functioning properly.
-
Documentation: Maintain detailed records of equipment maintenance and inspection activities. Documentation should include dates of maintenance, details of any repairs or replacements, and the signatures of personnel involved in the process.
Training and Safety Protocols
Upholstery welding businesses prioritize comprehensive training and safety protocols to ensure workplace safety and minimize the risk of accidents. Workplace safety is paramount in upholstery welding, given the potential hazards associated with welding activities. Employees undergo thorough welding training to familiarize themselves with the equipment, proper welding techniques, and safety procedures. This training covers various aspects such as the proper handling of welding equipment, understanding the properties of different materials, and the correct usage of personal protective equipment (PPE). Additionally, safety protocols are established to address potential risks and ensure that all employees are aware of the necessary precautions to be taken during welding operations. Regular safety audits and assessments are conducted to identify and rectify any safety concerns proactively. Upholstery welding businesses also encourage a safety-oriented culture, where all employees are empowered to report any safety hazards or incidents promptly. By adhering to stringent training and safety protocols, upholstery welding businesses actively promote a secure working environment for their employees.
Transitioning into the subsequent section about ’emergency response planning’, it is crucial for upholstery welding businesses to have effective strategies in place to respond to potential emergencies.
Emergency Response Planning
When it comes to emergency response planning in upholstery welding, several key points must be considered.
This includes ensuring the availability of safety equipment, identifying evacuation routes, and establishing communication protocols.
These points are crucial in effectively responding to any emergency situations that may arise in the upholstery welding environment.
Safety Equipment Availability
Adequate safety equipment should be readily available for emergency response planning in upholstery welding environments. This ensures that workers are prepared to address potential welding hazards effectively. The availability of safety gear is crucial for safeguarding the well-being of individuals and minimizing the risk of injuries or accidents.
In upholstery welding settings, the following safety equipment should be easily accessible:
- Personal protective equipment (PPE) such as welding helmets, gloves, and flame-resistant clothing.
- Fire extinguishers designed for combating welding-related fires.
- Emergency eyewash stations to address eye exposure to welding fumes or debris.
Having these safety measures in place enhances the overall safety preparedness and response capabilities within upholstery welding facilities.
Evacuation Route Identification
The availability of safety equipment is essential for emergency response planning in upholstery welding environments. This ensures that workers are prepared to address potential hazards effectively and identify evacuation routes with precision.
Evacuation planning is a critical aspect of emergency response in upholstery welding facilities. It involves the identification and marking of primary and alternate evacuation routes, which should be clearly communicated to all employees.
Regular emergency drills should be conducted to familiarize workers with these routes and ensure a prompt and organized evacuation in the event of an emergency. During these drills, workers should practice evacuating the premises swiftly and safely, taking into account potential obstacles or hazards that may impede their escape.
Communication Protocols Established
Establishing clear and effective communication protocols is crucial for ensuring a coordinated and efficient emergency response in upholstery welding facilities. This involves the following key aspects:
-
Team Communication: Implementing a communication system that ensures all team members are aware of emergency procedures and can effectively communicate with each other during an emergency. Utilizing communication devices such as two-way radios or alarms to quickly and effectively notify all personnel in the event of an emergency. Establishing designated meeting points or assembly areas where employees can gather after evacuating the welding area.
-
Safety Procedures: Clearly communicating safety protocols related to the welding process to all personnel, including emergency shutdown procedures and the proper operation of firefighting equipment. Conducting regular safety drills to ensure that all employees are familiar with emergency response protocols and can respond effectively in high-stress situations.
Frequently Asked Questions
What Are the Specific OSHA Regulations Regarding Ventilation Requirements for Upholstery Welding?
OSHA regulations regarding ventilation requirements for upholstery welding are crucial to ensure worker safety. Adequate ventilation systems should be in place to control fumes and protect workers from exposure. Additionally, OSHA provides PPE recommendations for workers in this environment.
Are There Any Specialized Personal Protective Equipment (Ppe) Recommendations for Upholstery Welding, Such as Specific Gloves or Aprons?
When working with upholstery welding, it’s essential to use specialized personal protective equipment (PPE) such as specific welding gloves and protective aprons. Additionally, adherence to ventilation requirements, fire prevention, and emergency response planning is crucial.
What Are Some Common Fire Prevention Measures Specific to Upholstery Welding, Beyond General Fire Safety Practices?
Fire prevention in upholstery welding involves strict adherence to safety regulations, regular equipment maintenance, and employing welding techniques that minimize fire risks. Implementation of fire-resistant materials and a comprehensive fire safety plan are crucial.
How Often Should Upholstery Welding Equipment Be Inspected and Maintained to Ensure Safety and Performance?
How often should upholstery welding equipment be inspected and maintained to ensure safety and performance? Inspection frequency and a robust maintenance schedule are crucial to upholding safety standards and equipment efficiency in upholstery welding operations.
Are There Any Unique Emergency Response Planning Considerations for Upholstery Welding, Such as Specific Hazards or Evacuation Procedures?
When it comes to emergency response planning, hazard identification is crucial. Upholstery welding poses unique risks, requiring specific evacuation procedures and training. Identifying potential hazards and preparing a tailored emergency response plan is essential.
Conclusion
In conclusion, safety practices in upholstery welding are essential for protecting workers and preventing workplace hazards.
Like a well-oiled machine, proper ventilation, personal protective equipment, fire prevention measures, equipment maintenance, and training are all crucial components in ensuring a safe working environment.
By implementing these safety protocols and emergency response planning, businesses can create a solid foundation for a secure and productive workplace.
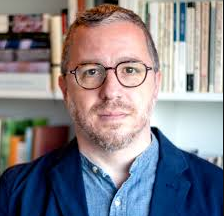
Dillon Hince, an expert in the realm of upholstery welding, brings a wealth of knowledge and experience to the craft. As the driving force behind nodpu.com, Dillon combines a passion for precision and creativity, offering unique insights into the art of seamlessly melding fabrics and materials. With a commitment to excellence, Dillon Hince is your go-to resource for innovative upholstery welding techniques, transforming ordinary pieces into extraordinary works of functional art.