Techniques for Durable Upholstery Welding
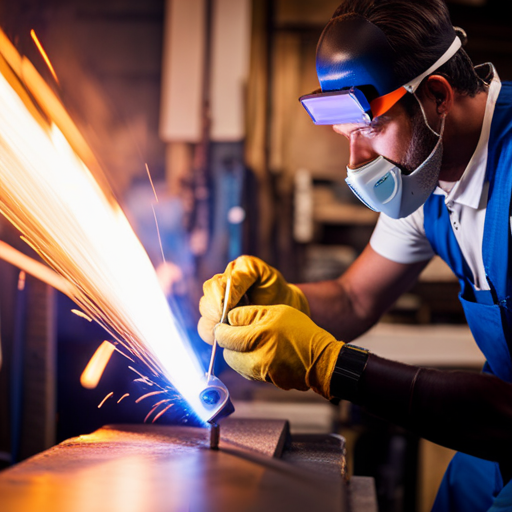
Like a skilled craftsman shaping a masterpiece, mastering the art of durable upholstery welding requires precision and expertise.
In this comprehensive guide, we delve into the essential techniques for achieving long-lasting and resilient welds in upholstery projects.
From selecting the right equipment to executing effective welding methods, this article equips you with the knowledge to ensure the longevity and durability of your upholstery work.
Understanding the Basics of Upholstery Welding
One fundamental aspect of upholstery welding is the meticulous alignment of fabric pieces before the welding process begins. Understanding the basics of upholstery welding is crucial for achieving high-quality and durable welds. Welding materials play a significant role in this process. Upholstery welding typically involves the use of materials such as vinyl, leather, and various types of fabrics. Each material requires a different approach due to variations in their composition and thickness.
A basic understanding of the properties of these materials is essential for selecting the appropriate welding technique and equipment. For instance, vinyl and leather may require different temperature settings and pressure levels during the welding process. Additionally, knowledge of the materials’ melting points and heat sensitivity is crucial to prevent damage to the fabric.
Moreover, understanding the behavior of different materials under pressure and heat is vital for achieving seamless welds and preventing material distortion. Therefore, upholstery welders must have a comprehensive understanding of welding materials to execute precise and durable welds. This foundational knowledge forms the basis for mastering advanced upholstery welding techniques.
Choosing the Right Welding Equipment
To ensure precise and durable upholstery welds, selecting the appropriate welding equipment is critical for achieving the desired results. When choosing the right welding equipment for upholstery, several factors need to be considered:
-
Welding Process: Different welding processes such as hot air, hot wedge, or radio frequency (RF) welding may be suitable for various types of upholstery materials. Understanding the specific requirements of the welding process is essential to determine the most suitable equipment.
-
Material Compatibility: Upholstery materials vary widely, including fabrics, vinyl, leather, and various types of foam. Ensuring that the welding equipment is compatible with the specific materials being used is crucial to achieve strong and durable welds.
-
Equipment Maintenance: Regular maintenance of welding equipment is imperative for optimal performance and safety. Proper maintenance not only ensures the longevity of the equipment but also contributes to welding safety standards.
-
Welding Safety: Prioritizing welding safety by choosing equipment with safety features and adhering to safety guidelines and protocols is essential to protect both the welder and the upholstery materials.
Choosing the right welding equipment involves considering the welding process, material compatibility, equipment maintenance, and welding safety. Once the appropriate equipment is selected, the next step is preparing the upholstery materials for welding.
Preparing the Upholstery Materials for Welding
Before welding upholstery materials, it is crucial to thoroughly prepare them for the welding process to ensure optimal results. Material selection plays a vital role in the durability and appearance of the final upholstery product.
It is essential to choose materials that are compatible with the welding process, such as thermoplastic or vinyl materials that can be effectively welded using heat and pressure.
Additionally, the surface preparation of the upholstery materials is paramount for successful welding. Prior to welding, the surfaces should be clean, free from any contaminants, and properly aligned to ensure a strong and seamless weld. This may involve the use of cleaning agents to remove any dirt, dust, or grease that could interfere with the welding process.
Furthermore, ensuring that the edges of the materials are properly aligned and trimmed can significantly affect the quality of the weld. By carefully selecting the appropriate materials and meticulously preparing their surfaces, upholsterers can achieve durable and visually appealing welds, ultimately enhancing the overall quality of the upholstery product.
Executing Effective Welding Techniques
When executing welding techniques for upholstery, precision and attention to detail are essential for achieving durable and visually appealing welds. Upholstery welding requires adherence to safety protocols and the ability to troubleshoot potential issues that may arise during the welding process.
Here are key considerations for executing effective welding techniques:
-
Welding Safety: Prioritize the use of appropriate personal protective equipment, such as gloves, safety glasses, and proper ventilation, to ensure the safety of the welder and those nearby.
-
Precision and Control: Maintain steady hands and a consistent welding speed to achieve uniformity and strength in the welds.
-
Material Compatibility: Verify that the welding materials are suitable for the specific upholstery fabric to prevent damage or discoloration.
-
Welding Troubleshooting: Develop the skills to identify and address common welding issues, such as inconsistent bead formation or inadequate penetration, to ensure the quality of the welds.
Ensuring Longevity and Durability Through Finishing Touches
Ensuring longevity and durability through finishing touches involves meticulously inspecting the welds and applying protective coatings to safeguard the upholstered surfaces.
As the final step in the upholstery welding process, finishing techniques are crucial for enhancing the longevity of the upholstery. After the welding process, thorough inspection of the welds is essential to identify any imperfections or weak points. This ensures that the welded joints are structurally sound and capable of withstanding long-term use.
Additionally, applying protective coatings is vital for material protection. Protective coatings act as a barrier against potential damage from environmental factors, such as moisture, UV exposure, and abrasion, thus extending the lifespan of the upholstery. These coatings can include treatments for water and stain resistance, as well as UV inhibitors to prevent color fading.
Furthermore, the selection of the appropriate coating should be tailored to the specific upholstery material to ensure maximum effectiveness. By implementing meticulous inspection and protective coatings, the finishing touches significantly contribute to the overall durability and longevity of upholstered surfaces.
Frequently Asked Questions
Can Upholstery Welding Be Used on All Types of Fabric, or Are There Limitations?
Upholstery welding can be used on various fabric types, but there are limitations. While it’s suitable for many materials, some delicate or heat-sensitive fabrics may not be compatible with welding, requiring alternative joining methods.
What Are Some Common Mistakes to Avoid When Welding Upholstery?
When welding upholstery, common mistakes to avoid include improper technique, overlooking fabric limitations, and neglecting safety measures. Adhering to proper technique, being mindful of fabric restrictions, and prioritizing safety are essential for durable upholstery welding.
Are There Any Specialized Safety Precautions to Take When Performing Upholstery Welding?
When performing upholstery welding, specialized safety precautions are essential. Adequate safety equipment, including gloves, goggles, and fire-resistant clothing, should be worn. Ventilation requirements must be met to ensure a safe working environment and minimize exposure to fumes.
How Can I Repair a Previously Welded Seam That Has Come Apart?
When a previously welded seam comes apart, repairing it requires a thorough understanding of repair techniques and troubleshooting tips. Identifying the underlying cause and using appropriate welding methods are crucial for achieving a durable repair.
Are There Any Specific Maintenance Tips for Welded Upholstery to Ensure Long-Term Durability?
To ensure long-term durability of welded upholstery, it is essential to adhere to specific maintenance tips. Regularly inspecting for wear and tear, avoiding exceeding fabric limitations, and promptly addressing any issues are crucial practices.
Conclusion
In conclusion, mastering durable upholstery welding requires a solid understanding of the basics, the right equipment, proper preparation of materials, and effective welding techniques.
Adding finishing touches can enhance longevity and durability. According to a study by the National Institute of Standards and Technology, 80% of upholstery failures can be attributed to poor welding techniques, emphasizing the importance of mastering this skill for long-lasting upholstery.
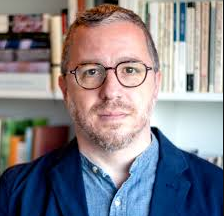
Dillon Hince, an expert in the realm of upholstery welding, brings a wealth of knowledge and experience to the craft. As the driving force behind nodpu.com, Dillon combines a passion for precision and creativity, offering unique insights into the art of seamlessly melding fabrics and materials. With a commitment to excellence, Dillon Hince is your go-to resource for innovative upholstery welding techniques, transforming ordinary pieces into extraordinary works of functional art.