The Environmental Impact of Upholstery Welding Materials
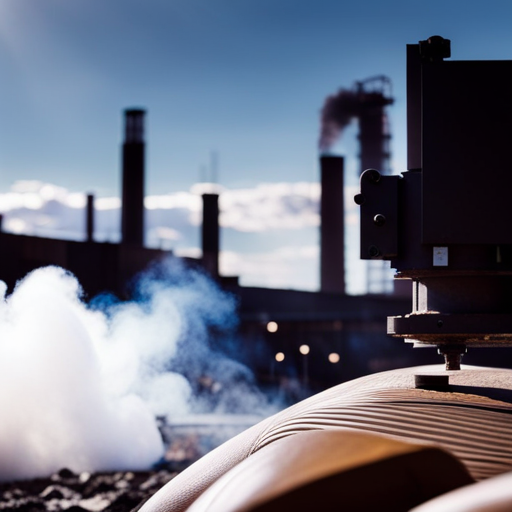
What is the true cost of upholstery welding materials on the environment?
As the demand for upholstered furniture continues to rise, it is crucial to assess the environmental impact of the materials used in their production. This article delves into the emissions of Volatile Organic Compounds (VOCs), energy consumption, and waste generation potential associated with upholstery welding materials.
Furthermore, it explores sustainable alternatives to mitigate their environmental impact.
Emissions of Volatile Organic Compounds (VOCs)
While upholstery welding materials contribute to the emissions of volatile organic compounds (VOCs), understanding the extent and impact of these emissions is crucial for environmental management and regulation. VOCs are a significant factor in air pollution and have various health implications. Long-term exposure to VOCs can lead to respiratory problems, irritation of the eyes and throat, and even damage to the central nervous system. Therefore, it is imperative to minimize VOC emissions from upholstery welding materials to protect the health of workers and the general public.
Regulatory compliance is another crucial aspect related to VOC emissions. Governments worldwide have enacted regulations to limit VOC emissions from industrial processes, including those related to upholstery welding. Upholstery manufacturers and welding professionals must adhere to these regulations to ensure that their operations do not contribute to environmental pollution. Failure to comply with these regulations can result in fines and legal consequences.
Therefore, understanding the VOC emissions from upholstery welding materials and ensuring regulatory compliance are essential for mitigating the environmental impact and protecting public health.
Energy Consumption During Production
Energy consumption during the production of upholstery welding materials is a critical factor in assessing their environmental impact. Several key aspects contribute to the energy consumption in this process:
-
Raw material sourcing: The extraction, processing, and transportation of raw materials such as fabrics, foams, and metal components demand significant energy inputs.
-
Manufacturing process: The energy-intensive nature of the manufacturing process, including cutting, shaping, and assembling materials, significantly contributes to the overall energy consumption.
-
Machinery operation: The operation of heavy machinery and equipment for cutting, welding, and finishing processes requires substantial energy.
-
Heating and drying processes: The utilization of energy for heating and drying materials during various stages of production is a significant contributor to overall energy consumption.
-
Packaging and transportation: The energy expended in packaging finished products and transporting them to distribution centers and end consumers should not be underestimated.
These factors collectively highlight the considerable energy consumption involved in the production of upholstery welding materials. Understanding and addressing these aspects are crucial in mitigating the environmental impact of this industry.
This leads to the subsequent section about ‘waste generation potential’, where the environmental consequences of the industry’s energy-intensive processes are further explored.
Waste Generation Potential
The considerable energy consumption during the production of upholstery welding materials leads to a significant waste generation potential. This waste must be carefully examined to assess its environmental impact.
Material disposal from the manufacturing processes of upholstery welding materials presents challenges. This is due to the various types of waste generated, including offcuts, trimmings, and unused materials. If not managed properly, these waste materials can contribute to environmental pollution and resource depletion.
Environmental regulations play a crucial role in governing the disposal of upholstery welding waste materials. These regulations ensure that waste is managed in an environmentally responsible manner. Upholstery welding materials manufacturers are required to comply with these regulations to minimize the environmental impact of waste generation.
One way to reduce the environmental footprint is by implementing waste management strategies such as recycling, reusing, or safely disposing of materials. By adhering to these regulations and adopting sustainable waste management practices, the upholstery welding industry can mitigate its waste generation potential. This will contribute to a more environmentally conscious approach to production.
Impact on Air Quality
Does the manufacturing of upholstery welding materials have a discernible impact on air quality?
Upholstery welding materials manufacturing can significantly impact air quality through the release of various pollutants. The following factors contribute to this impact:
-
Emissions of Volatile Organic Compounds (VOCs): VOCs are released during the production and application of upholstery welding materials, contributing to the formation of ground-level ozone and smog, which can have adverse health effects.
-
Particulate Matter (PM) Emissions: The manufacturing process can generate PM emissions, which can lead to respiratory and cardiovascular health effects upon inhalation.
-
Hazardous Air Pollutants (HAPs): Certain chemicals used in upholstery welding materials production, such as formaldehyde and benzene, are classified as HAPs and can have serious health effects.
-
Compliance with Regulatory Standards: Upholstery welding materials manufacturing facilities must adhere to regulatory standards set by environmental agencies to control air pollutant emissions and protect air quality.
-
Mitigation Measures: Implementation of emission control technologies and best practices can help minimize the impact on air quality.
Understanding the impact of upholstery welding materials on air quality is crucial for developing sustainable alternatives that mitigate these effects.
Transitioning to the subsequent section about ‘sustainable alternatives’, it is imperative to explore environmentally friendly materials and manufacturing processes that minimize air quality impacts while maintaining product quality and performance.
Sustainable Alternatives
Manufacturers are exploring sustainable alternatives to minimize the environmental impact of upholstery welding materials. This includes rethinking material sourcing and considering the entire product lifecycle to reduce the ecological footprint. To illustrate the sustainable alternatives being considered, the following table provides a comparison of traditional upholstery welding materials and potential sustainable alternatives.
Aspect | Traditional Material | Sustainable Alternative |
---|---|---|
Material Sourcing | Synthetic polymers derived from non-renewable resources | Natural fibers such as organic cotton or linen sourced from sustainable farms |
Product Lifecycle | Non-biodegradable materials leading to long-term waste | Biodegradable or recyclable materials to reduce end-of-life environmental impact |
Frequently Asked Questions
How Do Upholstery Welding Materials Affect the Health of Workers in the Manufacturing Process?
Upholstery welding materials can have significant health effects on workers in the manufacturing process. Exposure to fumes and gases can lead to respiratory issues, skin irritation, and other health concerns, highlighting the importance of prioritizing worker safety.
Are There Any Regulations or Standards in Place to Control the Use of Upholstery Welding Materials and Their Environmental Impact?
Regulations and compliance play a vital role in controlling the environmental impact of upholstery welding materials. To address this, the industry is increasingly adopting sustainable alternatives, aligning with stringent standards to minimize ecological repercussions.
Can Upholstery Welding Materials Contribute to Indoor Air Pollution in Homes and Offices?
Upholstery welding materials can contribute to indoor air pollution in homes and offices due to their emissions. This can pose health risks and may surpass exposure limits. Indoor air quality monitoring and appropriate ventilation are crucial for mitigating these impacts.
What Are the Long-Term Environmental Effects of Disposing of Upholstery Welding Materials?
The long-term environmental effects of disposing upholstery welding materials can be significant. The environmental impact of improper disposal methods includes soil and water contamination, as well as potential harm to wildlife and ecosystems. Proper disposal is crucial.
Are There Any Potential Risks Associated With Using Sustainable Alternatives to Traditional Upholstery Welding Materials?
When considering sustainable alternatives to traditional upholstery welding materials, it is crucial to assess potential risks. Understanding the environmental impact of these alternatives is essential to ensure that they are truly sustainable and do not pose unforeseen environmental risks.
Conclusion
In conclusion, the environmental impact of upholstery welding materials is significant. Emissions of VOCs contribute to air pollution, while high energy consumption and waste generation further exacerbate the environmental burden.
Sustainable alternatives, such as water-based adhesives and low-VOC materials, offer a promising solution. According to a recent study, the upholstery industry generates over 2.5 million tons of waste each year, highlighting the urgent need for more sustainable practices.
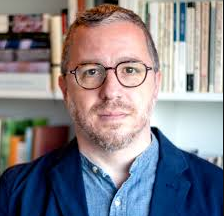
Dillon Hince, an expert in the realm of upholstery welding, brings a wealth of knowledge and experience to the craft. As the driving force behind nodpu.com, Dillon combines a passion for precision and creativity, offering unique insights into the art of seamlessly melding fabrics and materials. With a commitment to excellence, Dillon Hince is your go-to resource for innovative upholstery welding techniques, transforming ordinary pieces into extraordinary works of functional art.