The Future of Upholstery Welding Technology

The art of upholstery welding has transcended its traditional boundaries to become a symbol of innovation and progress.
As the industry embraces cutting-edge technology, the future of upholstery welding promises to revolutionize the way we perceive and interact with furniture.
From the evolution of materials to the integration of diverse elements, this article delves into the advancements that are set to define the future of upholstery welding technology.
Evolution of Materials
The evolution of materials in upholstery welding technology has significantly impacted the durability and aesthetic appeal of furniture products. Innovation in material advancements has played a pivotal role in enhancing the overall quality and longevity of upholstered furniture. With the integration of advanced materials, furniture manufacturers have been able to achieve superior structural integrity, ensuring that the upholstery withstands the test of time.
The evolution of materials has also facilitated the integration of cutting-edge design elements into furniture products. This has allowed for greater design integration, enabling furniture designers to explore a wide array of creative possibilities. The use of innovative materials has not only enhanced the durability of upholstered furniture but has also opened up new avenues for unique and aesthetically pleasing designs.
Furthermore, the continuous evolution of materials has led to the development of upholstery that is not only visually appealing but also more sustainable and environmentally friendly. Manufacturers are now able to create furniture that meets both aesthetic and eco-friendly standards, catering to the growing demand for sustainable products.
As material advancements continue to progress, the future of upholstery welding technology holds even greater potential for innovation and design excellence.
Enhanced Durability and Precision
As the demand for higher quality and longer-lasting upholstered furniture continues to grow, manufacturers are incorporating advanced welding technologies to achieve enhanced durability and precision in their products. Precision welding techniques are being employed to ensure seamless and strong joins in upholstery frames, thereby enhancing their structural integrity and longevity. Additionally, the use of durable materials such as high-strength steel and aluminum alloys is becoming increasingly prevalent in upholstery manufacturing. These materials offer superior resistance to wear, tear, and corrosion, contributing to the overall durability of the furniture.
Furthermore, advancements in welding technology have led to the development of more precise and efficient welding processes. This precision in welding not only ensures the strength and stability of the furniture but also allows for intricate designs and seamless finishing, meeting the evolving aesthetic preferences of consumers. Manufacturers are also integrating robotic welding systems to achieve consistent and precise welds, further enhancing the durability and quality of upholstered furniture.
Streamlined Production Processes
In the realm of upholstery welding technology, streamlined production processes are increasingly reliant on automation and efficiency.
Advanced robotic welding techniques have revolutionized the industry, enabling enhanced precision and speed in production.
Moreover, the integration of advanced material handling systems has further optimized the workflow, minimizing downtime and maximizing output.
Automation and Efficiency
Implementing automated welding processes in upholstery production has revolutionized efficiency and streamlined production processes.
Robotic automation has significantly enhanced the speed and accuracy of welding tasks, leading to a reduction in production time and increased output. This has resulted in a more efficient allocation of resources and a decrease in production costs.
The utilization of advanced technologies has also improved the overall quality and consistency of welds, minimizing rework and enhancing the final product.
Furthermore, the integration of automation has facilitated a more flexible production line, allowing for quick adjustments to accommodate custom orders and changing market demands.
Advanced Robotic Welding
The incorporation of advanced robotic welding technology has drastically enhanced the speed and precision of upholstery welding processes, leading to a quantifiable reduction in production time and an increase in overall output.
Advanced robotics have revolutionized the upholstery welding industry by enabling highly precise and efficient welding techniques. These robotic systems are equipped with advanced sensors and sophisticated programming, allowing them to execute intricate welds with unparalleled accuracy.
The use of advanced robotics in precision welding has minimized human error and increased the consistency of weld quality, resulting in higher productivity and cost-efficiency. Furthermore, these robotic systems can be seamlessly integrated into streamlined production processes, optimizing the entire manufacturing workflow.
As a result, upholstery manufacturers are experiencing significant improvements in operational efficiency and product quality due to the implementation of advanced robotic welding technology.
Enhanced Material Handling
The seamless integration of advanced robotic welding technology into streamlined production processes has significantly improved operational efficiency and product quality within the upholstery manufacturing industry. This advancement has led to improved ergonomics and efficient production through enhanced material handling.
The benefits of this integration include:
- Reduced manual labor requirements
- Increased precision in material placement
- Optimized workflow management
These improvements have not only streamlined the production processes but also minimized the risk of errors and workplace injuries. As the industry continues to embrace these technological advancements, the integration of diverse materials into the upholstery welding process becomes an essential aspect to explore further.
Integration of Diverse Materials
The integration of diverse materials in upholstery welding technology has led to significant advancements in material compatibility, allowing for the seamless joining of different types of materials. This has resulted in streamlined welding processes, leading to increased efficiency and reduced production time.
Furthermore, the enhanced compatibility has also contributed to improved product durability, meeting the evolving demands of the upholstery industry.
Material Compatibility Advancements
Material compatibility advancements in upholstery welding technology have revolutionized the integration of diverse materials, paving the way for enhanced functionality and design possibilities.
Material innovation has led to the development of new combinations of fabrics, foams, and other materials, expanding the scope of possibilities for upholstered products.
Compatibility testing processes have become more rigorous, ensuring the durability and longevity of the welded joints, even when disparate materials are used. This has opened up opportunities for combining materials with different properties, such as strength, flexibility, and heat resistance, to create innovative and high-performance upholstery products.
These advancements are driving the industry towards a future where designers and manufacturers can seamlessly integrate a wide range of materials, resulting in products that are both aesthetically pleasing and highly functional.
This progress seamlessly transitions into the subsequent section about ‘streamlined welding processes’.
Streamlined Welding Processes
Advancing the integration of diverse materials in upholstery welding technology, streamlined welding processes have become a focal point for enhancing efficiency and precision. These processes leverage advanced techniques to seamlessly weld different materials, resulting in improved efficiency and cost-effective solutions.
By integrating diverse materials such as plastics, fabrics, and metals with precision, manufacturers can achieve significant cost savings and reduced production times. Streamlined welding processes also contribute to minimizing material waste, further enhancing cost-effectiveness.
Moreover, the improved efficiency in welding diverse materials ensures that the final products meet high-quality standards, enhancing customer satisfaction. As the industry continues to embrace these advancements, streamlined welding processes are poised to revolutionize upholstery manufacturing.
This emphasis on efficiency and precision sets the stage for enhanced product durability, which is crucial for meeting evolving market demands.
Enhanced Product Durability
An essential aspect of enhancing product durability in upholstery welding technology involves the seamless integration of diverse materials. Improved techniques for integrating materials such as leather, fabric, and synthetic fibers are crucial for enhancing the longevity of upholstered products.
The use of advanced welding technologies allows for a stronger bond between different materials, resulting in increased durability and resistance to wear and tear. Additionally, the implementation of innovative longevity solutions, such as reinforced seam welding and multi-material bonding, further enhances the overall strength and lifespan of upholstered products.
Aesthetically Pleasing Designs
Upholstery welding technology is evolving to produce aesthetically pleasing designs that demonstrate precision and artistry. Creative innovation in welding techniques has led to an enhanced visual appeal in upholstered products. This has allowed for the creation of intricate and elegant designs that were previously challenging to achieve. The use of advanced welding methods has enabled the incorporation of intricate patterns, smooth contours, and seamless edges, elevating the overall aesthetics of upholstered furniture and automotive interiors.
Creative Innovation | Visual Appeal |
---|---|
Advanced Welding Methods | Intricate Patterns |
Smooth Contours | |
Seamless Edges |
These developments have not only enhanced the visual appeal of upholstered products but also expanded the possibilities for designers to explore new artistic expressions. As upholstery welding technology continues to advance, it opens doors for designers to push the boundaries of creativity, offering consumers a wide array of visually captivating and aesthetically pleasing options.
The focus on aesthetically pleasing designs seamlessly transitions into the subsequent section about sustainability and environmental impact, addressing the holistic approach in upholstery welding technology.
Sustainability and Environmental Impact
The focus on aesthetically pleasing designs seamlessly transitions into the sustainability and environmental impact of upholstery welding technology. As the industry evolves, there is a growing emphasis on sustainable practices and environmental responsibility. Upholstery welding technology is following suit, with manufacturers and designers prioritizing eco-friendly processes and materials.
This shift towards sustainability is driven by the recognition of the environmental impact of traditional manufacturing methods and the need to minimize it.
-
Recyclable Materials: Upholstery welding technology is increasingly utilizing recyclable materials, reducing waste and lessening the burden on landfills.
-
Energy-Efficient Processes: Manufacturers are investing in energy-efficient welding equipment and processes, significantly reducing energy consumption and greenhouse gas emissions.
-
Eco-Friendly Finishing Techniques: There is a rising adoption of environmentally friendly finishing techniques, such as powder coating, which eliminates the need for harmful solvents and reduces volatile organic compound (VOC) emissions.
Frequently Asked Questions
How Does Upholstery Welding Technology Impact the Overall Cost of Furniture Production?
Upholstery welding technology significantly impacts the overall cost of furniture production by enhancing efficiency and enabling cost-saving measures. It streamlines the manufacturing process, reduces material wastage, and enhances the durability of furniture, ultimately leading to cost savings.
What Advancements in Upholstery Welding Technology Are Expected in the Next 5-10 Years?
Advancements in upholstery welding technology are expected to revolutionize the industry in the next 5-10 years. These advancements will enhance efficiency, precision, and durability, impacting the future of furniture production and design.
Are There Any Potential Health and Safety Concerns Associated With the Use of Advanced Upholstery Welding Technology?
Potential health concerns associated with the use of advanced upholstery welding technology may include exposure to fumes, gases, and ultraviolet radiation. Safety measures such as proper ventilation, protective gear, and training are critical for mitigating these risks.
How Does the Integration of Diverse Materials in Upholstery Welding Impact the Overall Quality and Longevity of the Furniture?
The integration of diverse materials in upholstery welding significantly impacts the overall quality and longevity of the furniture. Welding techniques, when tailored to specific materials, can enhance durability and aesthetics, although this may impact the cost of production.
What Are the Potential Implications of Sustainability and Environmental Impact in the Future of Upholstery Welding Technology?
Sustainability impact and environmental implications are crucial factors in shaping the future of upholstery welding technology. As the industry evolves, a focus on sustainable materials and processes will be essential for reducing environmental impact and ensuring long-term viability.
Conclusion
In the grand tapestry of technological evolution, upholstery welding technology stands as a beacon of progress. Its seamless integration of diverse materials, enhanced durability, and streamlined production processes have paved the way for a future of aesthetically pleasing designs and sustainable practices.
As we continue to weave the fabric of innovation, the future of upholstery welding technology holds the promise of a harmonious blend of precision and environmental consciousness.
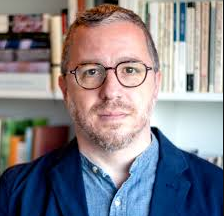
Dillon Hince, an expert in the realm of upholstery welding, brings a wealth of knowledge and experience to the craft. As the driving force behind nodpu.com, Dillon combines a passion for precision and creativity, offering unique insights into the art of seamlessly melding fabrics and materials. With a commitment to excellence, Dillon Hince is your go-to resource for innovative upholstery welding techniques, transforming ordinary pieces into extraordinary works of functional art.