The Impact of Fabric Weave on Welding Outcomes

Like threads intricately woven to create a strong fabric, the weave of materials used in welding can significantly impact the outcome of the process. From penetration depth to heat distribution, the characteristics of fabric weave play a crucial role in determining the quality of welds.
This article explores the correlation between fabric weave and welding outcomes, providing insights into optimizing techniques for different weaves.
Understanding this relationship is essential for achieving superior welding results.
Fabric Weave Characteristics
Weave patterns play a crucial role in the interaction between welding and fabric, ultimately impacting the quality of the weld. The weave pattern of a fabric can have significant effects on welding outcomes. For instance, a tight and uniform weave pattern can provide better support for the welding process, resulting in stronger and more reliable welds. On the other hand, a loose or irregular weave pattern may lead to inconsistencies in the welding process, affecting the overall integrity of the weld.
The interaction between welding and fabric weave patterns is a critical consideration in ensuring high-quality welding outcomes. Understanding how different weave patterns affect welding can help in selecting the most suitable fabric for specific welding applications. It also emphasizes the importance of fabric quality and consistency in achieving desired welding results.
Influence on Weld Penetration
The interaction between fabric weave patterns and welding directly impacts weld penetration, influencing the depth and uniformity of the weld bead. Weld penetration refers to the depth to which the weld extends into the base material. Fabric weave patterns can affect weld penetration by influencing the flow of molten metal and the heat distribution during welding.
When welding different fabric weaves, the welding parameters such as heat input, travel speed, and electrode size must be adjusted to accommodate the varying material thickness. For instance, a tighter fabric weave may require higher heat input to achieve sufficient weld penetration, while a looser weave may necessitate lower heat input to prevent excessive penetration. Material thickness also plays a crucial role in weld penetration, as thicker materials generally require higher heat input for adequate penetration.
Understanding the influence of fabric weave patterns on weld penetration is essential for achieving consistent and high-quality welds across different fabric types and material thicknesses.
This impact on weld penetration highlights the need to consider the fabric weave when determining welding parameters and strategies. This understanding also lays the groundwork for exploring the subsequent section on the impact of fabric weave on heat distribution during welding.
Impact on Heat Distribution
Fabric weave patterns directly influence heat distribution during welding, with a number of factors such as material thickness and weave tightness impacting the flow of heat and its uniform dispersion. The heat conduction behavior of different weave patterns plays a crucial role in determining the welding outcomes. When considering the impact of fabric weave on heat distribution, it is essential to take into account the material thickness as it directly affects the heat conduction characteristics. Thicker materials tend to conduct heat more slowly, leading to different heat distribution patterns compared to thinner materials. Additionally, the tightness of the weave also influences heat conduction, affecting the uniformity of heat dispersion across the fabric during welding. Understanding the relationship between fabric weave, material thickness, and heat conduction is vital for achieving consistent and high-quality welding results.
Heat Distribution Factors | Impact |
---|---|
Material Thickness | Affects heat conduction behavior |
Weave Tightness | Influences uniformity of heat dispersion |
Considering these factors, it becomes evident that the fabric weave has a significant impact on heat distribution during welding, which in turn affects the overall welding outcomes. Transitioning into the subsequent section, it is crucial to explore considerations for different weaves in welding processes.
Considerations for Different Weaves
When considering different weaves in welding processes, an understanding of their specific impact is essential for optimal outcomes. This understanding involves careful consideration of welding parameters and material compatibility.
Here are four key considerations for different weaves in welding:
-
Welding Parameters: Different weaves may require adjustments in welding parameters such as voltage, current, travel speed, and heat input. For instance, a tighter weave may necessitate higher heat input to ensure proper fusion, while a wider weave might require adjustments to prevent overheating.
-
Material Compatibility: The choice of weave should align with the material being welded. Certain weaves may work better with specific materials due to their melting points, thermal conductivity, and overall characteristics. Understanding the material compatibility is crucial for achieving strong and durable welds.
-
Heat Distribution: The weave pattern significantly influences heat distribution during welding. A tighter weave can lead to more concentrated heat, affecting the width and depth of the weld bead, while a wider weave can result in better heat dissipation.
-
Penetration and Fusion: Different weaves can impact the penetration and fusion of the weld. Understanding how each weave pattern affects the depth of penetration and the degree of fusion is critical for producing high-quality welds.
Optimizing Welding Techniques
Optimizing welding techniques requires a thorough understanding of weave patterns and their impact on the welding process. Weaving patterns play a crucial role in determining the welding speed and ensuring material compatibility. To effectively optimize welding techniques, it is essential to consider the weave type and its influence on the welding process. The table below outlines various weave patterns and their impact on welding outcomes.
Weave Pattern | Welding Speed | Material Compatibility |
---|---|---|
Plain Weave | Moderate | Most materials |
Twill Weave | Fast | Heat-resistant materials |
Satin Weave | Slow | Delicate materials |
Basket Weave | Variable | Thick materials |
Leno Weave | Variable | High-tensile materials |
Understanding the relationship between weave patterns and welding outcomes is crucial for achieving optimal results. By selecting the appropriate weave pattern and adjusting welding techniques accordingly, welders can enhance efficiency and ensure high-quality welds across a wide range of materials.
Frequently Asked Questions
Can the Fabric Weave Affect the Quality and Appearance of the Weld Seam?
Fabric weave significantly influences welding appearance, quality control, and distortion resistance. Careful fabric selection is crucial for achieving desired welding outcomes. Understanding how fabric weave affects welding is essential for maintaining high-quality weld seam appearance.
Are There Specific Fabric Weaves That Are More Prone to Distortion or Warping During Welding?
Fabric weave impact on welding outcomes is evident in the distortion susceptibility of certain weaves. For instance, twill weaves, due to their diagonal pattern, may be more prone to distortion during welding compared to plain weaves.
How Does the Fabric Weave Impact the Strength and Durability of the Welded Joint?
The impact of heat on the strength and durability of a welded joint is significant, with fabric structure playing a crucial role. Understanding how fabric weave influences these factors is imperative to achieving optimal welding outcomes.
Are There Any Fabric Weaves That Are More Susceptible to Porosity or Other Welding Defects?
Fabric weave susceptibility to welding defects varies. Certain weaves may be more prone to porosity. Understanding the impact of fabric weave on weld appearance is crucial to achieving high-quality welded joints.
Can the Fabric Weave Influence the Amount of Spatter Produced During Welding?
The fabric weave can significantly influence the amount of spatter produced during welding. Various weave patterns can impact spatter by affecting gas flow and heat dissipation, ultimately influencing the weld quality and efficiency.
Conclusion
In conclusion, the fabric weave plays a crucial role in determining welding outcomes. Understanding the characteristics of different weaves and their influence on weld penetration and heat distribution is essential for optimizing welding techniques. By carefully considering these factors, welders can achieve more precise and efficient results.
The impact of fabric weave on welding outcomes cannot be underestimated, and it is a critical factor that demands careful attention and consideration in the welding process.
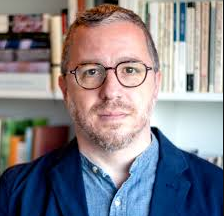
Dillon Hince, an expert in the realm of upholstery welding, brings a wealth of knowledge and experience to the craft. As the driving force behind nodpu.com, Dillon combines a passion for precision and creativity, offering unique insights into the art of seamlessly melding fabrics and materials. With a commitment to excellence, Dillon Hince is your go-to resource for innovative upholstery welding techniques, transforming ordinary pieces into extraordinary works of functional art.