The Role of Adhesives in Upholstery Welding
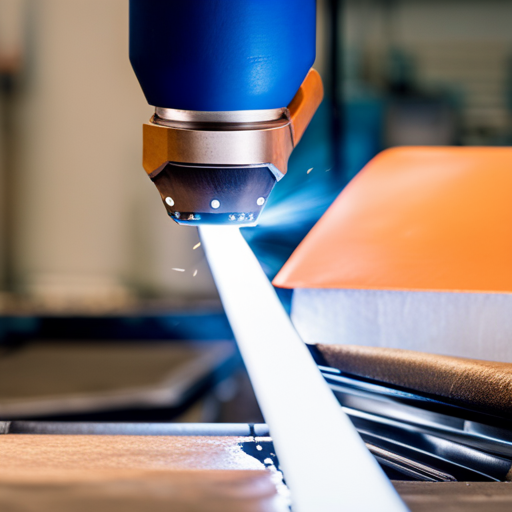
Sticking together like glue, adhesives play a crucial role in upholstery welding, offering a strong and durable bond between materials.
This article delves into the significance of adhesives in upholstery welding, exploring the various types and application techniques.
Additionally, it highlights the advantages of using adhesives in welding and provides insights into selecting the right adhesives.
Furthermore, the article discusses future trends in adhesive technology for upholstery welding, offering a comprehensive overview of this essential aspect of the industry.
Importance of Adhesives in Upholstery Welding
Playing a crucial role in strengthening seams and enhancing durability, adhesives are integral to the process of upholstery welding. Adhesive durability is of utmost importance in ensuring the longevity of upholstery welds, as it directly affects the overall lifespan of the upholstered product.
When selecting adhesives for upholstery welding, material compatibility is a critical consideration. Adhesives must be compatible with a wide range of upholstery materials, including fabrics, leather, vinyl, and various foam types, to ensure a strong and lasting bond. Poor material compatibility can lead to delamination, weakening of the seams, and ultimately, product failure.
Furthermore, adhesive durability and material compatibility are essential for withstanding the stresses and strains that upholstered products endure during their lifespan. They contribute significantly to the overall quality and performance of the upholstery welds.
Understanding the importance of adhesives in upholstery welding sets the foundation for exploring the different types of adhesives used in this process.
Types of Adhesives Used in Upholstery Welding
When it comes to upholstery welding, the types of adhesives used play a crucial role in determining the overall strength and durability of the bond. Adhesive bonding strength, heat resistance, and compatibility with upholstery materials are key factors that upholstery professionals consider when selecting the appropriate adhesive for the job.
Understanding the characteristics and limitations of different types of adhesives is essential for achieving high-quality and long-lasting upholstery welds.
Adhesive Bonding Strength
Various types of adhesives are commonly used in upholstery welding to achieve different levels of bonding strength. The choice of adhesive greatly influences the durability of the bond and the optimization of the bonding process. When considering adhesive bonding strength, it is essential to take into account the specific properties of different adhesives.
The following types of adhesives are often utilized in upholstery welding:
- Polyurethane adhesives
- Epoxy adhesives
- Cyanoacrylate adhesives
- Acrylic adhesives
Each type offers distinct characteristics that cater to varying bonding requirements in upholstery welding. Understanding the strengths and limitations of these adhesives is crucial for ensuring the desired bond integrity.
This discussion naturally leads to the subsequent section about the ‘heat resistance of adhesives’.
Heat Resistance of Adhesives
The heat resistance of adhesives used in upholstery welding is a critical factor in ensuring the long-term durability of bonded materials. Adhesive performance in high-temperature environments is essential to maintain the integrity of upholstered products, particularly in automotive and outdoor furniture applications.
When considering the manufacturing processes involved in upholstery welding, it is crucial to select adhesives that can withstand the heat generated during welding without compromising their bonding strength. Certain types of adhesives, such as heat-activated adhesives or solvent-based adhesives with high-temperature resistance, are commonly used in upholstery welding to ensure reliable and long-lasting bonds.
Manufacturers must carefully evaluate the heat resistance properties of adhesives to guarantee the quality and longevity of upholstered products.
Compatibility With Upholstery Materials
Adhesives used in upholstery welding must consistently demonstrate compatibility with a wide range of upholstery materials to ensure reliable and durable bonds. When selecting adhesives for upholstery material bonding, several factors need to be considered:
- Flexibility to accommodate different material movements
- Resistance to chemicals and solvents commonly found in upholstery
- Ability to bond to various upholstery substrates such as leather, fabric, and vinyl
- Compatibility with the temperature and humidity conditions upholstery may be exposed to
The adhesive material selection process is crucial in achieving strong and long-lasting bonds that withstand the demands placed on upholstered furniture. Understanding the compatibility of adhesives with different upholstery materials is essential for successful upholstery welding.
Now, let’s delve into the application techniques for adhesive bonding.
Application Techniques for Adhesive Bonding
When considering application techniques for adhesive bonding in upholstery welding, precision and consistency are essential for achieving strong and durable bonds. Adhesive surface preparation plays a crucial role in ensuring the effectiveness of the bonding process. Proper cleaning and priming of the surfaces to be bonded are essential for maximizing the adhesive’s ability to form a strong bond with the upholstery materials. Additionally, bonding process optimization involves controlling factors such as temperature, pressure, and curing time to ensure the adhesive cures uniformly and achieves the desired bond strength.
Factors to Consider in Adhesive Bonding |
---|
Adhesive Surface Preparation |
Bonding Process Optimization |
Temperature and Pressure Control |
Attention to these factors is critical in achieving consistent, high-quality adhesive bonds in upholstery welding applications.
These application techniques are crucial for ensuring the reliability and durability of the adhesive bonds in upholstery welding. Proper surface preparation and process optimization are essential for maximizing the performance of adhesives in bonding upholstery materials. The meticulous application of these techniques sets the stage for discussing the advantages of using adhesives in welding.
Advantages of Using Adhesives in Welding
Incorporating adhesives in welding processes enhances the structural integrity and long-term performance of upholstered components by providing a reliable and durable bonding solution. The advantages of using adhesives in welding are numerous, making it a preferred method for upholstery applications.
The following benefits highlight why adhesives are advantageous in upholstery welding:
-
Long-Term Durability: Adhesives create strong and lasting bonds, ensuring the longevity of the upholstered components.
-
Cost Effectiveness: Adhesives can reduce the need for additional mechanical fasteners, saving on material and labor costs.
-
Environmental Impact: Many adhesives are solvent-free and low in volatile organic compounds (VOCs), contributing to environmentally friendly manufacturing processes.
-
Improved Aesthetics: Adhesives can provide a seamless and clean finish, enhancing the overall appearance of the upholstery.
These advantages demonstrate the significant value that adhesives bring to the welding process in upholstery applications. Considering these benefits, it is crucial to carefully select adhesives that align with the specific requirements of upholstery welding.
Now, let’s delve into the considerations for selecting adhesives in upholstery welding.
Considerations for Selecting Adhesives in Upholstery Welding
When selecting adhesives for upholstery welding, several important considerations come into play.
First, one must assess the compatibility of the adhesive with the materials being joined to ensure a strong and durable bond.
Additionally, the heat resistance requirements of the application must be taken into account, as well as the suitability of the adhesive application method for the specific welding process.
Adhesive Compatibility With Materials
The selection of adhesives in upholstery welding must prioritize compatibility with the materials being joined to ensure optimal performance and durability. When considering adhesive compatibility with materials in upholstery welding, it is important to take into account the following factors:
- Material porosity and surface energy
- Environmental exposure and aging effects
- Chemical resistance and interaction with cleaning agents
- Flexibility and elongation properties
Adhesive bonding is significantly influenced by the compatibility of the adhesive and the materials being joined. Material compatibility ensures a strong and durable bond, contributing to the overall quality and longevity of the upholstery.
In the context of upholstery welding, considering these factors is crucial for achieving reliable and long-lasting results. Moving forward, it is essential to delve into the heat resistance requirements in the next section.
Heat Resistance Requirements
Considering the factors of material compatibility discussed previously, it is imperative to address the specific heat resistance requirements when selecting adhesives for upholstery welding. Heat resistance testing is crucial in determining the suitability of adhesives for this application.
Adhesive material selection should consider the temperature range to which the upholstery will be exposed during its lifetime, ensuring that the adhesive can withstand these conditions without degradation. High-temperature resistance is particularly important in upholstery welding, as the adhesives need to maintain their bond strength even when subjected to heat from sources such as sunlight or friction. Therefore, rigorous heat resistance testing is essential to assess the adhesive’s ability to withstand these conditions.
Understanding the heat resistance requirements is fundamental in ensuring the longevity and performance of the upholstery welding process.
Moving on to the subsequent section about ‘application method suitability’…
Application Method Suitability
To ensure optimal performance in upholstery welding, the selection of adhesives must carefully consider the suitability of the application method. When choosing adhesives for upholstery welding, it is crucial to consider the following factors related to application techniques and bonding strength:
- Compatibility with specific welding equipment
- Ease of application and dispensing
- Bonding strength relative to the intended application method
- Resistance to environmental factors such as temperature and humidity
The application method suitability directly impacts the overall effectiveness and durability of the adhesive bond in upholstery welding. Therefore, careful consideration of these factors is essential in selecting adhesives that can withstand the specific demands of the upholstery welding process.
Future Trends in Adhesive Technology for Upholstery Welding
As professionals in the upholstery welding industry, we anticipate significant advancements in adhesive technology that will revolutionize the way we approach bonding materials. Adhesive innovation is being driven by market demands for stronger, more flexible, and environmentally friendly bonding solutions. Manufacturers are investing heavily in research and development to meet these demands, leading to the creation of adhesives that offer superior strength and durability while being more sustainable.
Future challenges in adhesive technology for upholstery welding include the need to develop adhesives that can withstand extreme temperatures and harsh environmental conditions, as well as the demand for adhesives that can bond a wider range of materials, including plastics and composites. Additionally, there is a growing focus on developing adhesives that offer rapid curing times to improve production efficiency.
In terms of industry applications, the future of adhesive technology in upholstery welding looks promising. Advancements in adhesive technology are expected to enable the bonding of a wider variety of materials, opening up new design possibilities for manufacturers. Furthermore, the development of adhesives with enhanced environmental credentials will align with the industry’s increasing focus on sustainability.
Frequently Asked Questions
Can Adhesives Be Used as a Sole Method for Upholstery Welding, or Do They Need to Be Used in Conjunction With Other Techniques?
Adhesives can provide significant adhesive strength for upholstery welding. However, they are typically used in conjunction with other techniques to ensure fabric compatibility and durability. Various application methods should be considered for optimal results.
Are There Any Environmental or Health Considerations to Take Into Account When Using Adhesives in Upholstery Welding?
When using adhesives in upholstery welding, it’s crucial to consider the environmental impact and health considerations. Proper ventilation and the use of eco-friendly, low-VOC adhesives can minimize health risks and reduce environmental impact.
How Do Adhesives Affect the Overall Durability and Longevity of Upholstery Welds Compared to Other Methods?
In upholstery welding, adhesive application significantly impacts weld strength and material compatibility, influencing overall durability. The environmental impact and maintenance requirements of adhesives also warrant consideration, underscoring their pivotal role in upholstery longevity.
Are There Any Specific Maintenance or Care Requirements for Upholstery Welds That Have Been Bonded With Adhesives?
Maintenance requirements for upholstery welds bonded with adhesives include regular inspection for wear and tear, cleaning with gentle solutions, and avoiding harsh chemicals. Care considerations involve protecting the bonded area from excessive moisture and extreme temperature fluctuations.
How Do Different Types of Fabrics and Materials Used in Upholstery Affect the Selection and Application of Adhesives for Welding?
Selecting adhesives for upholstery welding involves considering adhesive compatibility with different fabric types. Factors like porosity, stretch, and heat resistance influence adhesive selection. Understanding fabric properties is crucial for successful adhesive application in upholstery welding.
Conclusion
In conclusion, the role of adhesives in upholstery welding is crucial for creating strong and durable bonds. Various types of adhesives are used, and careful consideration must be given to selecting the right one for the job.
Application techniques and future trends in adhesive technology continue to evolve, offering new opportunities for improving the quality and efficiency of upholstery welding.
Adhesives provide numerous advantages and are an essential component in the process of upholstery welding.
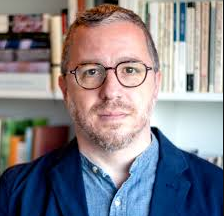
Dillon Hince, an expert in the realm of upholstery welding, brings a wealth of knowledge and experience to the craft. As the driving force behind nodpu.com, Dillon combines a passion for precision and creativity, offering unique insights into the art of seamlessly melding fabrics and materials. With a commitment to excellence, Dillon Hince is your go-to resource for innovative upholstery welding techniques, transforming ordinary pieces into extraordinary works of functional art.