The Role of Technology in Enhancing Upholstery Welding Services
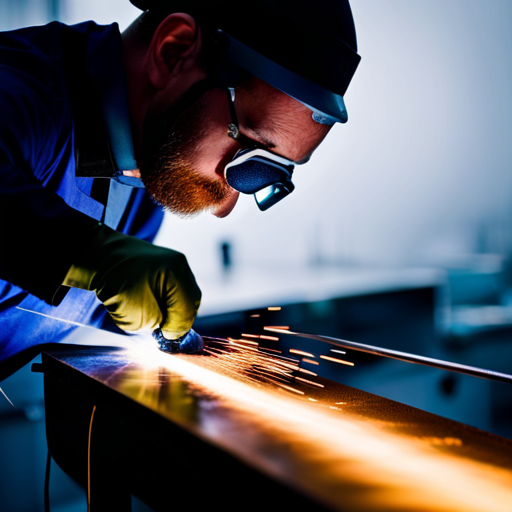
In the thriving world of upholstery welding, the integration of advanced technology has revolutionized the industry.
Take, for instance, the case of a furniture manufacturer who, by implementing state-of-the-art welding techniques, witnessed a substantial increase in production efficiency and product precision.
This article delves into the pivotal role of technology in enhancing upholstery welding services, exploring the evolution, automation, and future developments that are reshaping the landscape of this essential manufacturing process.
Evolution of Upholstery Welding Technology
The evolution of upholstery welding technology has significantly transformed the efficiency and precision of upholstery welding processes. Robotic welding has been a key innovation in this evolution. Robotic welding systems have revolutionized upholstery welding by offering consistent and high-quality welds, increasing production rates, and reducing overall operational costs. These systems are programmed to perform repetitive welding tasks with unparalleled accuracy, resulting in uniform and flawless welds across a wide range of upholstery materials.
Furthermore, laser welding has emerged as a game-changing technology in the upholstery welding industry. Laser welding provides several advantages, including minimal heat-affected zones, precise control over the welding process, and the ability to weld complex geometries with exceptional accuracy. This technology has significantly enhanced the quality and aesthetics of upholstery welding, meeting the increasing demand for seamless and visually appealing welds in modern upholstery design.
Automation in Upholstery Welding
With the implementation of advanced robotic and laser welding systems, automation has revolutionized the upholstery welding process, optimizing efficiency and precision.
Robotic welding applications offer numerous benefits in upholstery welding. One significant advantage is the consistency and accuracy achieved through automation. Robots can perform repetitive tasks with high precision, reducing the margin of error in welding upholstery components. This not only ensures a higher quality of welds but also minimizes material waste and rework.
Additionally, automation in upholstery welding enhances productivity by enabling continuous operation without the need for frequent breaks, resulting in faster turnaround times for upholstery projects. Furthermore, robotic welding systems can be programmed to work in various orientations and angles, allowing for greater flexibility in welding complex upholstery designs.
Automation also contributes to a safer working environment by reducing the exposure of human welders to hazardous fumes and intense welding conditions.
Advanced Welding Techniques
Implementing advanced welding techniques further enhances the efficiency and precision of upholstery welding processes, allowing for greater versatility and improved quality in manufacturing upholstery components. Two prominent advanced welding techniques that have revolutionized the upholstery welding industry are robotic welding and laser welding. These techniques offer various advantages such as increased speed, accuracy, and consistency in welding operations.
Advanced Welding Techniques | Advantages |
---|---|
Robotic Welding | – High precision |
– Consistency | |
– Increased speed | |
– Versatility | |
– Complex welds | |
Laser Welding | – Precise welds |
– Minimal heat input | |
– High welding speed | |
– Minimal distortion | |
– Enhanced quality |
Robotic welding, through the use of automated robotic arms, ensures high precision and consistency in welding operations. It is capable of handling complex welds with ease, leading to improved efficiency. On the other hand, laser welding offers precise welds with minimal heat input, resulting in high welding speeds and enhanced quality. This technique also minimizes distortion in the welded components, contributing to the overall quality of upholstery welding services.
Impact on Efficiency and Precision
Advanced welding techniques significantly enhance the efficiency and precision of upholstery welding processes, leading to improved productivity and quality in manufacturing upholstery components.
Efficiency improvement is a key benefit of advanced welding technologies in upholstery manufacturing. These techniques enable faster welding speeds, reduced material waste, and streamlined processes, ultimately resulting in cost savings and increased output.
Precision enhancement is another notable advantage. Advanced welding technologies offer greater control over the welding parameters, such as heat input and joint penetration, leading to more accurate and consistent welds. This level of precision is crucial in ensuring the structural integrity and aesthetic appeal of upholstery components. Additionally, precise welding minimizes the need for rework or repairs, saving both time and resources.
The combination of enhanced efficiency and precision not only elevates the overall quality of upholstery products but also contributes to a more sustainable and competitive manufacturing process.
As technology continues to advance, further improvements in efficiency and precision are anticipated, promising even more significant benefits for the upholstery welding industry.
Future Technological Developments
As technological advancements continue to progress, the future of upholstery welding services is poised for significant developments. Robotics integration is set to revolutionize the industry, offering precise and efficient welding processes. Robots can be programmed to handle complex welding tasks with high accuracy, enhancing the overall quality of upholstery welding. This integration not only improves speed and precision but also reduces the risk of human error, ultimately leading to higher quality and consistency in welding services.
Moreover, the utilization of smart materials is anticipated to play a pivotal role in the future of upholstery welding. Smart materials have the capability to adapt to changing environmental conditions, providing enhanced durability and flexibility in upholstery welding applications. These materials can self-repair, withstand extreme temperatures, and offer improved resistance to wear and tear. As a result, the integration of smart materials will lead to longer-lasting and more resilient upholstery products.
Frequently Asked Questions
What Are the Most Common Materials Used in Upholstery Welding?
Common materials used in upholstery welding include vinyl, leather, and fabric. Upholstery techniques such as heat sealing and hot air welding are commonly employed. These materials and techniques are vital in ensuring durable and aesthetically appealing upholstery products.
What Safety Considerations Should Be Taken Into Account When Using Advanced Welding Techniques in Upholstery?
Safety precautions and protective gear are crucial when using advanced upholstery welding techniques. Proper ventilation requirements must be met to ensure a safe working environment. Following these measures minimizes risks and promotes a secure welding process.
How Does Upholstery Welding Technology Impact Environmental Sustainability?
Upholstery welding technology fosters environmental sustainability through reduced emissions, efficient resource utilization, and waste minimization. Innovations in materials and processes, driven by sustainability initiatives, ensure a greener footprint for upholstery welding services.
Are There Any Specialized Training Programs Available for Mastering Advanced Upholstery Welding Techniques?
Specialized training and certification programs are available for mastering advanced upholstery welding techniques. These programs provide hands-on experience, ensuring proficiency in industry standards and safety protocols. They are essential for upskilling in the latest technology.
What Are the Potential Drawbacks or Limitations of Automation in Upholstery Welding?
Automation in upholstery welding can enhance efficiency, but it may face limitations in intricate designs or irregularly shaped furniture. Precision and adaptability are crucial. Technology must balance speed with quality in this specialized craft.
Conclusion
In conclusion, technology plays a pivotal role in enhancing upholstery welding services.
The evolution of upholstery welding technology has led to automation and advanced welding techniques, resulting in increased efficiency and precision.
Future technological developments are expected to further revolutionize the industry.
Overall, technology has transformed upholstery welding, leading to enhanced efficiency, precision, and productivity.
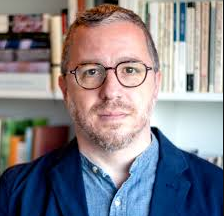
Dillon Hince, an expert in the realm of upholstery welding, brings a wealth of knowledge and experience to the craft. As the driving force behind nodpu.com, Dillon combines a passion for precision and creativity, offering unique insights into the art of seamlessly melding fabrics and materials. With a commitment to excellence, Dillon Hince is your go-to resource for innovative upholstery welding techniques, transforming ordinary pieces into extraordinary works of functional art.