The Role of Upholstery Foam in Welding
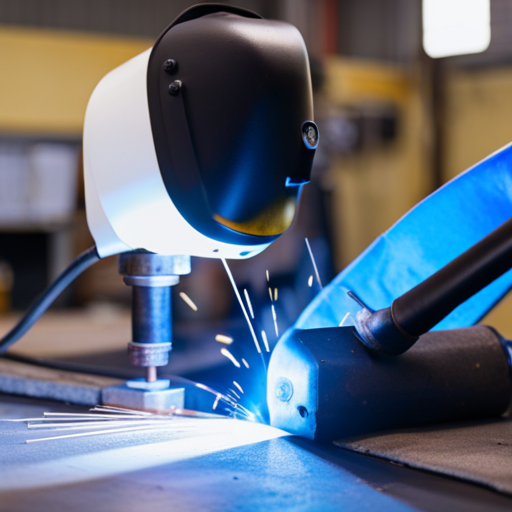
Like a shield against the fury of the flames, upholstery foam stands as a crucial barrier in welding operations. Its ability to withstand extreme heat and protect against molten metal splatter makes it an indispensable tool for maintaining material integrity and ensuring the safety of welders.
This article explores the vital role of upholstery foam in welding, from its heat-resistant properties to its impact on enhancing efficiency and safety in welding operations.
Heat Protection With Upholstery Foam
When considering heat protection in welding, upholstery foam serves as a reliable insulating barrier. Its ability to provide thermal insulation and protective padding makes it an essential element in ensuring the safety of welders. Upholstery foam acts as a heat-resistant shield, safeguarding individuals and surrounding materials from the intense temperatures generated during welding processes.
The thermal insulation properties of upholstery foam enable it to effectively minimize the transfer of heat, protecting individuals from potential burns or heat-related injuries. Additionally, its use as protective padding serves to cushion and shield against accidental contact with hot surfaces or splattering metal.
Upholstery foam’s capacity to withstand high temperatures and its fire-retardant characteristics further enhance its value in welding applications. By creating a barrier that reduces heat transfer, upholstery foam plays a critical role in maintaining a secure working environment for welders.
Upholstery Foam as a Heat-Resistant Barrier
Upholstery foam serves as a heat-resistant barrier by effectively minimizing the transfer of heat and providing protective padding in welding applications. The cellular structure of upholstery foam is designed to trap air within its pockets, creating a barrier that acts as a heat insulator. This property is particularly beneficial in welding, where intense heat is generated, and there is a need to protect nearby materials or components from heat damage. Upholstery foam effectively absorbs and disperses heat, preventing it from reaching the surfaces it covers. As a result, it helps in maintaining a safe working environment by reducing the risk of accidental burns or heat-related damage to surrounding materials.
The heat-resistant nature of upholstery foam makes it an indispensable component in welding applications, where the control and management of heat transfer are critical. Upholstery foam not only provides a protective barrier against heat but also contributes to enhancing the overall safety and efficiency of welding processes. Its ability to withstand high temperatures and minimize heat transfer makes it an invaluable material in various welding scenarios.
Transitioning into the subsequent section about ‘preventing heat transfer with upholstery foam’, it is essential to explore the specific mechanisms through which upholstery foam achieves this function.
Preventing Heat Transfer With Upholstery Foam
By effectively minimizing the transfer of heat, upholstery foam plays a crucial role in preventing heat transfer in welding applications. Heat insulation is a critical aspect of welding to ensure the safety of workers and the preservation of materials. Upholstery foam, with its heat-resistant properties, acts as a barrier that reduces heat transfer, protecting the surrounding environment and materials from damage.
Heat Insulation Properties | Material Preservation |
---|---|
High thermal resistance | Prevents material distortion |
Low thermal conductivity | Minimizes heat-induced degradation |
Retains shape under high temperatures | Preserves material integrity |
Resistant to thermal stress | Protects against heat-related wear |
Shields against radiant heat | Prevents overheating and melting |
The table above illustrates the key attributes of upholstery foam that contribute to its effectiveness in preventing heat transfer. Its high thermal resistance and low thermal conductivity make it an ideal material for heat insulation, ensuring that the welding process does not adversely affect the materials being worked on. Additionally, its ability to retain its shape under high temperatures and shield against radiant heat further enhances material preservation during welding operations.
Maintaining Material Integrity With Upholstery Foam
How does upholstery foam contribute to the preservation of material integrity during welding processes?
Upholstery foam plays a crucial role in maintaining material integrity during welding by providing essential support and protection. Its impact on material durability and thermal insulation is significant. Here are four key ways in which upholstery foam helps in maintaining material integrity during welding processes:
-
Protection from Heat Exposure:
Upholstery foam acts as a barrier, shielding the underlying materials from direct heat exposure during welding. This helps prevent damage and ensures the integrity of the materials being worked on. -
Support and Stability:
By providing a stable cushioning layer, upholstery foam supports the materials, preventing warping or distortion caused by heat and pressure during welding. -
Thermal Insulation:
The thermal insulation properties of upholstery foam help in maintaining consistent welding conditions, preventing fluctuations in temperature that could otherwise compromise material integrity. -
Reduction of Vibrations:
Upholstery foam absorbs vibrations generated during welding, reducing the risk of structural damage and maintaining the integrity of the materials involved.
Enhancing Safety and Efficiency in Welding Operations
To enhance safety and efficiency in welding operations, meticulous attention to the proper utilization of upholstery foam is essential. Upholstery foam plays a crucial role in creating a safe and efficient working environment for welders. When it comes to welding techniques, the use of upholstery foam can provide a protective barrier between the welder and hard surfaces, reducing the risk of injury and enhancing overall safety. This is particularly important during prolonged welding tasks, where fatigue can increase the likelihood of accidents. Additionally, upholstery foam can be used to create custom supports and padding for welding equipment, ensuring that it is ergonomically optimized for the welder’s comfort and safety.
Furthermore, proper equipment maintenance is vital in welding operations to ensure safety and efficiency. Upholstery foam can act as a protective layer for equipment, preventing damage from heat, sparks, and debris. Regularly inspecting and maintaining upholstery foam can prolong the lifespan of welding equipment, reducing the need for costly repairs or replacements. By incorporating upholstery foam into equipment maintenance routines, welders can uphold high safety standards and optimize operational efficiency.
Frequently Asked Questions
Can Upholstery Foam Be Used in High-Temperature Welding Applications?
Upholstery foam is not suitable for high-temperature welding applications due to its low heat resistance. When considering thermal insulation and material compatibility for welding techniques, it’s important to choose materials specifically designed for high-temperature environments.
What Types of Upholstery Foam Are Best for Preventing Heat Transfer in Welding Operations?
In selecting upholstery foam for preventing heat transfer in welding, consider foam selection carefully for safety measures. Prioritize heat resistance to maintain material integrity. Remember, "safety first" when choosing the best foam for welding operations.
Are There Any Specific Guidelines for Using Upholstery Foam as a Heat-Resistant Barrier in Welding?
When utilizing heat-resistant materials in welding, adherence to specific guidelines is crucial to ensure safety and effectiveness. Understanding welding techniques and the proper application of heat-resistant barriers, such as upholstery foam, is essential.
How Does Upholstery Foam Help Maintain Material Integrity in Welding Processes?
Upholstery foam, with its heat-resistant properties, acts as a protective barrier in welding processes, safeguarding material integrity and ensuring welding safety. Its efficient heat resistance enhances the overall efficiency of the welding process.
What Are the Best Practices for Incorporating Upholstery Foam to Enhance Safety and Efficiency in Welding Operations?
In welding operations, best practices for incorporating upholstery foam involve improving comfort while adhering to safety measures. This can be achieved by selecting high-quality foam materials and ensuring proper installation to enhance safety and efficiency.
Conclusion
In conclusion, upholstery foam plays a crucial role in welding operations. It provides heat protection and acts as a heat-resistant barrier. Additionally, it prevents heat transfer and maintains material integrity. Its use enhances safety and efficiency in the welding process, making it an indispensable tool for welders.
As the demand for high-quality welding continues to grow, the importance of upholstery foam in ensuring the safety and effectiveness of welding operations cannot be overstated.
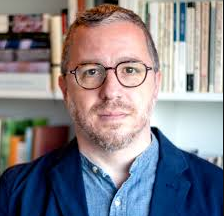
Dillon Hince, an expert in the realm of upholstery welding, brings a wealth of knowledge and experience to the craft. As the driving force behind nodpu.com, Dillon combines a passion for precision and creativity, offering unique insights into the art of seamlessly melding fabrics and materials. With a commitment to excellence, Dillon Hince is your go-to resource for innovative upholstery welding techniques, transforming ordinary pieces into extraordinary works of functional art.