The Science Behind Upholstery Welding
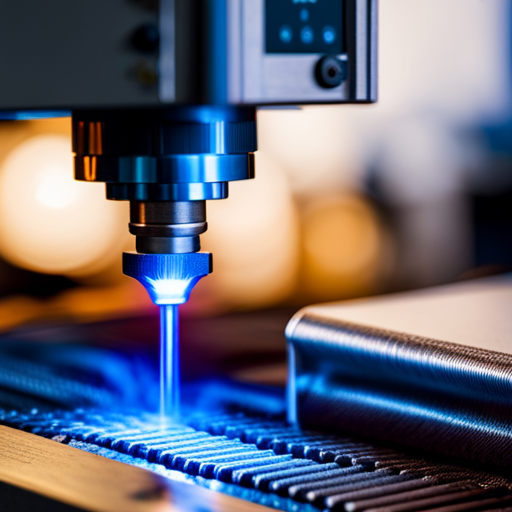
The theory of upholstery welding goes beyond mere fabrication; it delves into the intricate science behind the creation of durable and high-quality seams. By understanding the principles of heat transfer, molecular bonding, and material manipulation techniques, upholstery welding becomes a precise art form.
This article explores the scientific intricacies and factors that contribute to the longevity and durability of upholstery welding, shedding light on the meticulous process that goes into creating strong and resilient seams.
Principles of Heat Transfer
The principles of heat transfer play a crucial role in the process of upholstery welding, dictating the efficient transfer of heat to bond materials together. In upholstery welding, heat transfer mechanisms such as conduction, convection, and radiation are utilized to ensure the effective joining of materials.
Conduction involves the transfer of heat through direct molecular contact between the materials being bonded, while convection facilitates heat transfer through the movement of fluids or gases. Additionally, radiation enables heat to be transferred through electromagnetic waves. Understanding the molecular structure of the materials being welded is essential for optimizing heat transfer.
Different materials have varying molecular structures, which can affect their ability to conduct and retain heat. By comprehending these molecular properties, upholsterers can adjust welding parameters such as temperature and pressure to achieve strong and durable bonds.
This understanding of heat transfer mechanisms and molecular structure sets the stage for examining the next critical aspect of upholstery welding: the molecular bonding process.
Molecular Bonding in Upholstery Welding
Molecular bonding plays a crucial role in upholstery welding, impacting the overall strength and durability of the final product. Understanding the bonding mechanisms and considering material compatibility are essential factors in achieving high-quality welds.
The way molecules bond together not only affects the aesthetic appeal of the upholstery but also determines its resilience and longevity.
Bonding Mechanisms Explained
Bonding mechanisms in upholstery welding involve the interaction of molecules to create strong and durable bonds. This is achieved through two primary bonding mechanisms:
-
Mechanical bonding: This involves the interlocking of molecules at the surface level, creating a physical bond between the materials.
-
Chemical bonding: This occurs when the molecules of the materials being welded together form new chemical bonds, resulting in a strong and permanent fusion.
Understanding these bonding mechanisms is crucial for achieving high-quality upholstery welding results. By comprehending how molecules interact and bond at a molecular level, welders can optimize their techniques to create durable and long-lasting upholstery products.
Moreover, the choice of materials and their compatibility is essential in ensuring successful bonding mechanisms. Now, let’s delve into the crucial consideration of material compatibility in upholstery welding.
Material Compatibility Considerations
Considerations for material compatibility play a crucial role in achieving successful molecular bonding in upholstery welding. When selecting materials for welding, it is essential to ensure that they are compatible to achieve a strong and durable bond. Different materials may require specific welding techniques to ensure proper molecular bonding.
For instance, thermoplastic materials require heat-based welding techniques, while thermoset materials may require specialized adhesives or ultrasonic welding methods. The choice of welding technique must align with the compatibility of the materials to achieve optimal molecular bonding.
Understanding the molecular structure and properties of the materials is imperative in determining the most suitable welding technique for successful upholstery welding. Material compatibility directly impacts the effectiveness of the welding process and the overall durability of the upholstered product.
This compatibility is vital in ensuring the longevity and performance of the final upholstery product.
Impact on Durability
The compatibility of materials directly influences the durability of molecular bonding in upholstery welding. Upholstery welding, a process that involves the fusion of materials at a molecular level, is heavily reliant on the durability of the molecular bonds formed.
Durability factors, such as the strength of the molecular bonds and the resistance to wear and tear, play a crucial role in determining the overall longevity enhancement of the welded upholstery.
Factors influencing the impact on durability include the types of materials being welded, the welding technique employed, and the environmental conditions to which the welded upholstery will be subjected.
These factors collectively contribute to the overall resilience and longevity of the upholstery welding, ensuring a high-quality end product.
Synthetic Material Manipulation Techniques
An essential aspect of upholstery welding involves the manipulation of synthetic materials to achieve durable and aesthetically pleasing seams. Material manipulation techniques are crucial for ensuring the overall fabric strength and seam integrity.
When welding synthetic materials, heat transfer plays a pivotal role. By carefully controlling the heat application during the welding process, the molecular bonding of the synthetic materials can be optimized, resulting in strong and resilient seams. Understanding the behavior of different synthetic materials under varying heat transfer conditions is essential for achieving high-quality welds.
Additionally, the manipulation of synthetic materials requires a deep understanding of fabric strength, ensuring that the welding process does not compromise the overall integrity and durability of the upholstery. These techniques are fundamental in achieving seamless and durable welds on synthetic materials, enhancing the overall quality and longevity of upholstered products.
Understanding material properties further enhances the ability to manipulate synthetic materials effectively for upholstery welding.
Understanding Material Properties
Manipulating synthetic materials requires a comprehensive understanding of their properties, allowing for precise control of the heat transfer process during upholstery welding. Material properties play a crucial role in determining the suitability of a material for welding, as well as the specific welding techniques that should be employed.
Key factors to consider include:
-
Melting Point: Each synthetic material has a specific melting point, which must be carefully matched with the welding temperature to ensure proper fusion without causing damage to the material.
-
Thermal Conductivity: Understanding the material’s ability to conduct heat is essential for controlling the heat transfer process during welding. Materials with high thermal conductivity require different welding techniques compared to those with low thermal conductivity.
-
Chemical Composition: The chemical composition of the material influences its reaction to heat, affecting the welding process. It is vital to consider how the material will behave under the application of heat to achieve strong and durable welds.
Importance of Pressure in Upholstery Welding
Understanding the role of pressure is crucial in achieving high-quality upholstery welding. In upholstery welding, pressure and temperature control are essential factors for successful seam welding. The pressure applied during the welding process plays a pivotal role in ensuring proper fusion of the materials. Optimal pressure ensures that the materials are held firmly together, allowing for effective heat transfer and fusion. Insufficient pressure may result in weak or incomplete welds, compromising the overall integrity of the seam.
When comparing welding techniques, the importance of pressure becomes evident. For instance, in hot air welding, the pressure exerted by the welding equipment directly impacts the quality of the seam. Additionally, in high-frequency welding, pressure is instrumental in creating a uniform bond between the materials. Proper pressure control also contributes to reducing the likelihood of material distortion during the welding process.
Role of Heat in Creating Strong Seams
Heat plays a crucial role in creating strong seams in upholstery welding by facilitating molecular bonding between the materials. This process not only enhances the overall strength of the seams but also ensures durability and longevity.
Additionally, the application of heat can have a significant impact on different types of fabrics, influencing their behavior and performance in welded seams.
Heat and Molecular Bonding
The application of precise heat during upholstery welding plays a crucial role in creating strong molecular bonds in the seams. The molecular structure of the materials being welded is directly influenced by the heat application, affecting the overall strength and durability of the seams. Understanding the relationship between heat and molecular bonding is essential for achieving high-quality upholstery welding.
Key factors to consider include:
-
Temperature Control: Precise control of the heat input is necessary to ensure the desired molecular bonding without damaging the materials.
-
Heat Distribution: Uniform distribution of heat across the weld area is vital for consistent and strong molecular bonding.
-
Material Compatibility: Different materials require specific heat application techniques to achieve optimal molecular bonding and seam strength.
Seam Strength Enhancement
The creation of strong seams in upholstery welding relies on precise heat application, which is pivotal for reinforcing molecular bonds and ensuring seam durability.
When heat is applied to the welded seam, it enhances the strength of the bond by promoting molecular interlocking, resulting in an improved overall durability. The heat softens the materials, allowing them to merge and form a robust, cohesive bond.
As the heat dissipates, the materials cool and solidify, creating a strong and enduring seam. This process not only enhances the strength of the seam but also contributes to its longevity, ensuring that the upholstered furniture withstands the rigors of everyday use.
Therefore, the role of heat in creating strong seams is essential for enhancing strength and improving durability in upholstery welding.
Impact on Fabric
The impact of precise heat application on fabric is pivotal for reinforcing molecular bonds and ensuring seam durability in upholstery welding.
Fabric compatibility is essential to consider when applying heat during the welding process. Different fabrics have varying heat tolerances, and understanding their compatibility with the welding process is crucial for achieving strong seams.
Additionally, temperature control plays a significant role in creating strong seams. Maintaining the optimal temperature during the welding process is essential for preventing fabric damage while ensuring the formation of durable seams.
Durability Factors in Upholstery Welding
Durability factors play a crucial role in determining the longevity and quality of upholstery welding. One of the key durability factors in upholstery welding is seam strength. The strength of the seam is vital as it directly impacts the overall durability of the upholstered piece. A strong seam prevents fraying and separation, ensuring that the upholstery maintains its integrity over time, even in high-stress areas. Factors such as the type of fabric, thread, and welding technique contribute to seam strength. Additionally, the quality of the weld itself is paramount in enhancing durability. Proper penetration and fusion of the materials through welding result in a robust and enduring bond, further reinforcing the seam strength.
In the subsequent section about ‘longevity enhancement through welding’, the focus will shift to the specific welding techniques and materials that contribute to the overall durability of upholstery. By understanding the key factors that influence durability in upholstery welding, it becomes possible to optimize the welding process for enhanced longevity and quality.
Longevity Enhancement Through Welding
Enhancing the longevity of upholstery through welding involves employing advanced welding techniques and durable materials. By utilizing these methods, upholstery can be made to withstand the test of time, ensuring that it remains in top condition for an extended period. Longevity improvement is a crucial aspect of upholstery welding, and it can be achieved through various welding techniques and approaches.
-
Precision Welding: Employing precise welding techniques ensures that the upholstery is welded together with accuracy, minimizing the risk of weak points or premature deterioration.
-
Material Selection: Choosing high-quality, durable materials for welding is essential for enhancing the longevity of upholstery. The use of robust fabrics and strong welding materials can significantly prolong the lifespan of the upholstery.
-
Reinforcement Strategies: Implementing reinforcement strategies, such as additional stitching or strategic welding in high-stress areas, can effectively enhance the longevity of the upholstery, making it more resistant to wear and tear.
Frequently Asked Questions
Can Upholstery Welding Be Used on Natural Materials Like Leather or Wool?
Upholstery welding can be used on natural materials like leather and wool. Leather’s durability makes it suitable for welding, while wool’s flexibility can also be effectively welded. These materials offer diverse options for upholstery welding applications.
Are There Any Environmental Concerns Associated With Upholstery Welding Processes?
There is a growing environmental impact associated with upholstery welding processes. Concerns about sustainability are mounting, as the industry grapples with reducing emissions and waste. Upholstery welding can contribute to these concerns.
How Does Humidity or Moisture in the Air Affect the Quality of Upholstery Welding?
Humidity and moisture in the air can impact upholstery welding quality. Material compatibility and welding techniques play a crucial role in mitigating these effects. Additionally, air quality and the welding process must be carefully managed to ensure optimal results.
Are There Any Safety Precautions or Potential Health Risks for Workers Involved in Upholstery Welding?
Ensuring employee well-being and workplace safety is paramount in upholstery welding. Safety precautions such as proper ventilation, protective gear, and training on potential health risks like fume exposure are crucial for a healthy work environment.
Can Upholstery Welding Be Used to Repair or Reinforce Existing Seams in Furniture or Other Upholstery Items?
Upholstery welding can effectively repair and reinforce existing seams in furniture and other upholstery items. By using specialized welding techniques, it is possible to strengthen and extend the lifespan of these structures, providing a durable solution.
Conclusion
In conclusion, it is evident that upholstery welding involves complex principles of heat transfer, molecular bonding, and material manipulation.
By understanding material properties and applying appropriate pressure and heat, strong seams can be created, enhancing the durability and longevity of upholstery.
The science behind upholstery welding not only ensures the structural integrity of furniture but also contributes to its aesthetic appeal, making it an essential process in the upholstery industry.
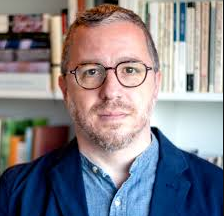
Dillon Hince, an expert in the realm of upholstery welding, brings a wealth of knowledge and experience to the craft. As the driving force behind nodpu.com, Dillon combines a passion for precision and creativity, offering unique insights into the art of seamlessly melding fabrics and materials. With a commitment to excellence, Dillon Hince is your go-to resource for innovative upholstery welding techniques, transforming ordinary pieces into extraordinary works of functional art.