Troubleshooting Common Material Issues in Upholstery Welding
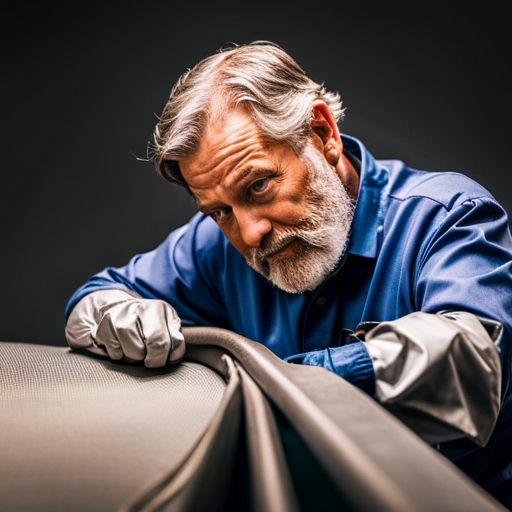
‘An ounce of prevention is worth a pound of cure,’ goes the proverb, and in the world of upholstery welding, this sentiment holds true. Troubleshooting common material issues is an essential skill for upholsterers seeking to ensure the quality and integrity of their work.
From fabric distortion to stitching irregularities, understanding and addressing these issues can make the difference between a flawless weld and a flawed finish. This article explores key techniques and solutions for resolving these challenges.
Fabric Distortion
Fabric distortion during upholstery welding can be caused by excessive heat or improper tensioning of the fabric. When the fabric is subjected to excessive heat during the welding process, it can lead to fabric stretching and warping. This can result in an uneven and distorted appearance of the upholstery, affecting the overall quality of the finished product.
Proper temperature control and adjustment are crucial in preventing fabric distortion. By carefully monitoring and regulating the welding temperature, the risk of fabric stretching and warping can be significantly reduced.
Additionally, ensuring that the fabric is appropriately tensioned before welding is essential. Improper tensioning can lead to uneven stress distribution during the welding process, causing the fabric to warp and distort.
Seam Puckering
Seam puckering can be a frustrating issue in upholstery welding. It is often caused by factors such as heat distribution problems, tension inconsistency, and the choice of material.
Understanding how these factors can lead to seam puckering is crucial for troubleshooting and resolving the problem effectively.
Heat Distribution Problems
The occurrence of seam puckering in upholstery welding can be attributed to uneven heat distribution during the welding process. This issue can significantly affect the quality and aesthetics of the welded seams.
To address heat distribution problems and prevent seam puckering, the following factors should be carefully considered:
-
Temperature Control: Ensure that the temperature settings on the welding equipment are appropriate for the specific material being welded. Inconsistent temperatures can lead to uneven heat distribution and subsequent seam puckering.
-
Welding Technique: Proper welding technique is crucial for even heat distribution. Techniques such as maintaining consistent speed and pressure during welding can help prevent seam puckering by ensuring uniform heat application.
-
Equipment Maintenance: Regular maintenance of welding equipment, including cleaning and calibration, is essential for consistent and even heat distribution.
-
Material Selection: Some materials are more prone to seam puckering due to their composition. Choosing materials with better heat resistance can help mitigate heat distribution problems.
Tension Inconsistency Issues
Addressing tension inconsistency issues in upholstery welding requires careful attention to the interplay between material properties and welding parameters. Seam puckering, a common result of tension inconsistency, can be mitigated through proper tension adjustment and troubleshooting.
To ensure seam consistency, maintenance techniques such as regular inspection of the tensioning system and cleaning of the welding equipment are essential. Additionally, verifying the compatibility of the fabric and welding machine is crucial for achieving optimal tension and preventing seam puckering.
Material Choice Impact
Achieving optimal tension and preventing seam puckering in upholstery welding is significantly influenced by the choice of materials used. The welding temperature and material compatibility play crucial roles in determining the final quality of the weld. Here are some key considerations for material choice impact:
-
Welding Temperature: Different materials require specific welding temperatures to achieve a strong and seamless bond. It is essential to understand the optimal welding temperature for the materials being welded to prevent seam puckering.
-
Material Compatibility: Using compatible materials is vital to ensure that the welding process results in a smooth and consistent seam. Incompatible materials can lead to tension inconsistency and seam puckering, affecting the overall quality of the upholstery.
-
Heat Resistance: Materials with varying heat resistance levels can cause tension inconsistencies during welding, leading to seam puckering. Selecting materials with similar heat resistance properties is crucial to prevent this issue.
-
Stretch and Recovery: The stretch and recovery characteristics of materials can impact seam puckering during welding. Choosing materials with similar stretch and recovery properties can help maintain optimal tension and prevent seam puckering.
Material Burn Marks
Material burn marks can be a common issue in upholstery welding that affects the visual appeal and structural integrity of the material.
Preventing burn marks through proper welding techniques and equipment maintenance is crucial to ensuring high-quality results.
Additionally, knowing how to effectively remove burn marks when they occur is essential for maintaining the overall quality of the upholstery.
Preventing Burn Marks
To prevent burn marks during upholstery welding, it is essential to carefully control the temperature and speed of the welding process. This can be achieved through proper temperature control and adherence to specific welding speed guidelines.
To further prevent burn marks and discoloration, consider the following:
-
Use appropriate welding tools: Ensure that the welding tools are suitable for the specific type and thickness of the upholstery material.
-
Maintain consistent speed: Avoid rapid movements during welding to prevent overheating and burn marks.
-
Test on scrap material: Before welding the actual upholstery, conduct a test on a scrap piece to determine the optimal temperature and speed settings.
-
Regular equipment maintenance: Keep the welding equipment clean and well-maintained to prevent any irregularities in temperature or speed control.
Removing Burn Marks
When addressing the issue of removing burn marks in upholstery welding, it is essential to carefully assess the extent of the damage and employ appropriate techniques to restore the material’s appearance.
Burn mark prevention and cleaning techniques play a crucial role in preserving the integrity of the fabric. For minor burn marks, gentle cleaning with a fabric-safe cleaner and a soft brush can effectively diminish their visibility.
However, for more severe damage, fabric color restoration and repair methods may be necessary. Utilizing fabric dyes or seeking professional reweaving services can help restore the original color and texture of the material.
By employing these techniques, it is possible to effectively remove burn marks from upholstery, ensuring a seamless and well-maintained appearance.
Now, let’s delve into the subsequent section about adhesion problems.
Adhesion Problems
One common adhesion problem encountered in upholstery welding is the occurrence of uneven or incomplete bonding between materials. This can lead to compromised durability and aesthetics of the upholstered products. To address this issue, consider the following:
-
Adhesion improvement, temperature control: Adjusting the temperature settings on the welding equipment can enhance the adhesion properties of the materials. Experiment with different temperature levels to find the optimal setting for the specific materials being welded.
-
Welding technique, surface preparation: Utilize proper welding techniques such as adjusting the welding speed and pressure to ensure a consistent and strong bond between materials. Additionally, thorough surface preparation, including cleaning and roughening the materials’ surfaces, can significantly improve adhesion.
-
Material compatibility: Ensure that the materials being welded are compatible with each other and suitable for the welding process being used. Incompatible materials can lead to poor adhesion.
-
Adhesive selection: Consider using specialized adhesives or bonding agents designed specifically for upholstery welding to enhance adhesion properties and overall bond strength.
By addressing these factors, upholstery welders can effectively mitigate adhesion problems and improve the overall quality of their welded products.
Transition: Now, let’s delve into the next common issue encountered in upholstery welding – ‘stitching irregularities’.
Stitching Irregularities
Stitching irregularities in upholstery welding can manifest as inconsistent or uneven stitching patterns across the material. These irregularities can be caused by various factors, with thread tension playing a crucial role. Incorrect thread tension can result in loose or tight stitches, leading to an unbalanced and irregular appearance in the stitching patterns. It is essential to ensure that the thread tension is properly adjusted to achieve uniform and aesthetically pleasing stitching.
The following table illustrates the impact of thread tension on stitching patterns:
Thread Tension | Stitching Pattern |
---|---|
Too Loose | Uneven stitches, loopy appearance |
Correct | Consistent and uniform stitches |
Too Tight | Excessive puckering, fabric distortion |
Maintaining the appropriate thread tension is fundamental in addressing stitching irregularities. By understanding the relationship between thread tension and stitching patterns, upholstery welders can troubleshoot and rectify irregularities effectively, ensuring high-quality and visually appealing upholstery products.
Thread Breakage
The upholstery welding process can be impeded by thread breakage, which is a common issue in the industry. Thread breakage can disrupt the stitching process and result in subpar welds. To address this issue, consider the following:
-
Check Thread Tension: Inconsistent or incorrect thread tension can lead to breakage. Ensure that the tension is set according to the material being welded to prevent excessive strain on the thread.
-
Inspect Stitch Quality: Poor stitch quality, such as irregular or overly tight stitching, can cause excessive stress on the thread, leading to breakage. Adjust the stitching parameters to ensure uniform and balanced stitching.
-
Evaluate Thread Quality: Low-quality or worn-out thread is more prone to breakage. Invest in high-quality, durable thread that is suitable for the specific welding application.
-
Maintain Equipment: Regularly maintain and lubricate the welding machine and the sewing mechanism to prevent unnecessary strain on the thread.
By addressing these factors, the occurrence of thread breakage can be minimized, resulting in more efficient and high-quality upholstery welding processes.
Now, let’s delve into the next common issue: ‘uneven welding lines’.
Uneven Welding Lines
Uneven welding lines can impede the upholstery welding process, leading to suboptimal weld quality and visual inconsistencies, which may arise from inadequate material alignment during the stitching process. Proper welding techniques are essential to ensure even welding lines.
Additionally, surface preparation is crucial to remove any contaminants or irregularities that could affect the welding process. Temperature control is another critical factor, as variations in temperature can result in uneven welding lines.
Welder experience also plays a significant role in achieving consistent and even welding lines. Experienced welders are better equipped to handle the intricacies of the welding process, ensuring that the material is aligned correctly and the welding is performed evenly. Regular training and skill development for welders can help in minimizing uneven welding lines.
Frequently Asked Questions
Can Upholstery Welding Be Used on All Types of Fabrics, or Are There Certain Materials That Are More Prone to Fabric Distortion or Adhesion Problems?
Fabric compatibility is crucial in upholstery welding, as certain materials are more prone to adhesion challenges and fabric distortion. Factors such as fabric thickness, composition, and coatings influence the success of welding applications. Understanding fabric properties is essential for successful results.
Are There Specific Techniques or Tools That Can Be Used to Prevent Material Burn Marks During the Upholstery Welding Process?
Preventing burn marks during upholstery welding is crucial for a flawless finish. Using protective tools like silicone-coated tape and heat-resistant fabrics can help avoid fabric distortion. Additionally, adjusting welding settings and using proper techniques can prevent seam puckering in stretchy fabrics.
How Can Seam Puckering Be Avoided When Welding Upholstery, Especially on Delicate or Stretchy Fabrics?
To avoid seam puckering when welding delicate or stretchy fabrics in upholstery, employ specific techniques such as adjusting heat settings, using a Teflon foot to reduce friction, and employing a lighter touch to prevent excessive stretching or distortion of the material.
What Are the Common Causes of Stitching Irregularities in Upholstery Welding, and How Can They Be Fixed?
Common causes of stitching irregularities in upholstery welding include improper stitching tension, leading to fabric warping. To fix this, ensure proper heat control and pressure distribution. Adjusting these factors can help achieve consistent stitching results.
Are There Any Special Considerations or Adjustments That Need to Be Made When Welding Upholstery With Uneven or Varied Thicknesses?
When welding upholstery with uneven or varied thicknesses, it is crucial to make adjustments to welding settings to accommodate the material thickness. Additionally, special attention should be given when welding on curves and uneven surfaces to ensure proper fusion.
Conclusion
In conclusion, troubleshooting common material issues in upholstery welding is essential for achieving high-quality results. By addressing fabric distortion, seam puckering, material burn marks, adhesion problems, stitching irregularities, thread breakage, and uneven welding lines, upholstery welders can ensure a finished product that meets industry standards.
Just as a skilled craftsman carefully hones their tools to create a masterpiece, attention to detail and problem-solving skills are crucial in the upholstery welding process.
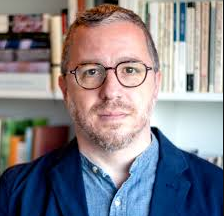
Dillon Hince, an expert in the realm of upholstery welding, brings a wealth of knowledge and experience to the craft. As the driving force behind nodpu.com, Dillon combines a passion for precision and creativity, offering unique insights into the art of seamlessly melding fabrics and materials. With a commitment to excellence, Dillon Hince is your go-to resource for innovative upholstery welding techniques, transforming ordinary pieces into extraordinary works of functional art.