Upholstery Welding for Aircraft and Marine Interiors
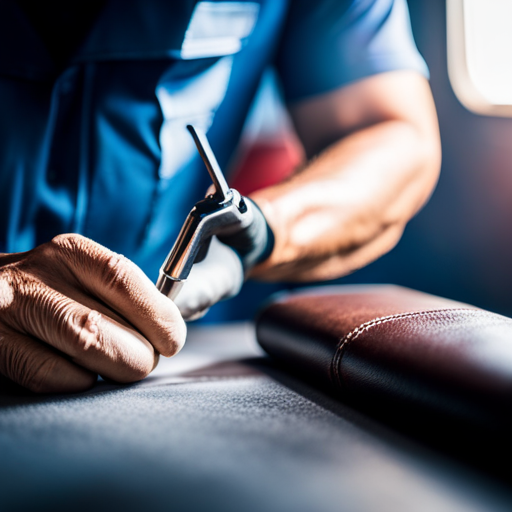
Upholstery welding stands as the pinnacle of precision and innovation, revolutionizing the construction of aircraft and marine interiors. This advanced technique seamlessly melds materials, ensuring unparalleled durability and aesthetics.
In this article, we delve into the multifaceted world of upholstery welding, exploring its advantages, applications in aircraft and marine interiors, welding techniques, and quality assurance measures.
Join us as we uncover the intricacies of this essential process in the realm of interior design and construction.
Upholstery Welding: An Overview
Upholstery welding in aircraft and marine interiors is a specialized technique used to join and seal fabric or vinyl materials. This process involves applying heat and pressure to create a strong and durable bond between the materials. Material compatibility is crucial, as different fabrics and vinyls require specific welding techniques and temperatures for optimal results. The welding process must be tailored to the specific materials being joined to ensure a seamless and secure bond.
The compatibility of materials is essential to guarantee the structural integrity and longevity of welded seams in aircraft and marine interiors. Understanding the properties of the materials being welded is paramount to achieving high-quality, durable welds that can withstand the unique demands of the aerospace and marine environments. With material compatibility at the forefront, upholstery welding becomes a vital skill in ensuring the safety and reliability of interior components.
Moving forward, it is essential to delve into the advantages of upholstery welding in aircraft and marine interiors.
Advantages of Upholstery Welding
Upholstery welding offers several advantages that make it a preferred choice for aircraft and marine interiors.
The process results in upholstery that is not only strong and durable but also resistant to wear and tear, making it ideal for high-traffic areas.
Additionally, upholstery welding allows for customization and intricate design work, providing endless possibilities for creating unique and visually appealing interior spaces.
Strength and Durability
The strength and durability of upholstery welding in aircraft and marine interiors is unparalleled in ensuring long-term performance and safety. This method offers numerous advantages, including:
-
Material Selection: Upholstery welding allows for the use of a wide range of materials, providing flexibility in design and function.
-
Maintenance: Welded upholstery offers ease of maintenance, reducing the need for frequent repairs and replacements.
-
Impact Resistance: Welded seams provide exceptional strength, enhancing the interior’s ability to withstand impact and stress.
-
Weight Reduction: By eliminating the need for additional hardware or fasteners, upholstery welding contributes to weight reduction, crucial for aircraft and marine applications.
These benefits make upholstery welding a superior choice for enhancing the strength and durability of interiors in aircraft and marine settings.
Customization and Design
How can upholstery welding contribute to the customization and design of aircraft and marine interiors? Upholstery welding offers a wide range of customization options and design flexibility, making it a preferred choice for interior designers and manufacturers in the aviation and marine industries. By using upholstery welding techniques, interior designers can create unique and personalized designs that cater to the specific preferences of their clients. Whether it’s intricate patterns, custom logos, or tailored color schemes, upholstery welding allows for endless design possibilities. The table below illustrates some of the key customization options and design flexibility provided by upholstery welding in aircraft and marine interiors.
Customization Options | Design Flexibility | Durability |
---|---|---|
Intricate Patterns | Tailored Designs | High Strength |
Custom Logos | Flexible Materials | Long-lasting |
Personalized Colors | Unique Textures | Resilience |
These features make upholstery welding an invaluable asset in achieving aesthetically pleasing and functional interiors.
This design versatility positions upholstery welding as an essential technique for creating bespoke and durable interiors in aircraft and marine settings. The next section will delve into the specific applications of upholstery welding in aircraft interiors.
Applications in Aircraft Interiors
Aircraft interiors benefit from the application of upholstery welding for enhancing durability and aesthetics. Upholstery welding plays a crucial role in ensuring aircraft safety, as it reinforces the integrity of the interior materials. Moreover, it allows for the use of a wide range of upholstery materials, including leather, synthetic fabrics, and vinyl, providing both functionality and visual appeal. Compliance with aircraft regulations is also facilitated through the use of welding technology, as it ensures that all interior components meet the required safety standards.
The intricate process of welding enables the creation of seamless and smooth finishes, contributing to a luxurious and modern cabin ambiance. Ultimately, the application of upholstery welding in aircraft interiors not only enhances the overall safety and quality of the cabin but also elevates the passenger experience, as it fosters a sense of comfort and sophistication.
Moving forward, let’s delve into the significance of upholstery welding in marine interiors.
Applications in Marine Interiors
The application of upholstery welding in marine interiors presents a range of innovative solutions tailored to the unique challenges of marine environments.
From improved durability in saltwater conditions to enhanced customization options, welding techniques offer numerous benefits for marine upholstery.
In the following discussion, we will explore the specific innovations and advantages that welding brings to marine interior applications.
Marine Upholstery Innovations
Innovative marine upholstery solutions are transforming the interiors of boats and ships, enhancing both aesthetics and durability.
The latest marine upholstery trends are witnessing a shift towards sustainable materials, reflecting the industry’s commitment to environmental responsibility.
Key innovations in marine upholstery applications include:
-
Sustainable Fabric Choices: Utilizing eco-friendly materials such as recycled polyester and organic cotton for upholstery, reducing environmental impact.
-
Advanced Water-Resistant Technologies: Incorporating hydrophobic fabrics and moisture-wicking upholstery to enhance durability and performance in marine environments.
-
Customized Design Options: Offering personalized upholstery solutions, allowing boat owners to express their individual style and preferences.
-
Ergonomic Comfort Features: Integrating innovative cushioning and support systems to ensure optimal comfort during long voyages, enhancing the overall boating experience.
Benefits of Welding
Upholstery welding offers significant advantages in the fabrication of marine interiors, ensuring robustness and longevity in the face of maritime conditions. Welding techniques, when applied to marine interiors, provide exceptional durability and resistance to corrosion, making them ideal for withstanding the harsh marine environment. This ensures that the upholstery maintains its quality and appearance over an extended period, aligning with industry standards for marine interior construction.
The benefits of welding in marine interiors extend beyond mere aesthetics, as the strength and reliability provided by welding techniques contribute to the overall safety and structural integrity of the marine vessel. This underscores the importance of adhering to industry standards in welding practices for marine interiors, ensuring that they meet stringent regulatory requirements.
Transitioning into the subsequent section, the focus will shift to exploring specific welding techniques tailored for upholstery.
Welding Techniques for Upholstery
When considering welding techniques for upholstery, it is important to prioritize precision and durability to ensure the integrity of the final product. Upholstery welding demands efficiency and precision to attain high-quality and durable results.
Here are four crucial aspects to consider when implementing welding techniques for upholstery:
-
Technology Integration: Embracing advanced welding technologies ensures precise and efficient results, enhancing the overall quality of the upholstery.
-
Skilled Labor: Employing highly skilled welders proficient in intricate welding techniques guarantees the precision required for upholstery welding.
-
Material Selection: Opting for materials conducive to welding and upholstery applications is essential for achieving durable and visually appealing results.
-
Quality Assurance: Rigorous quality checks and adherence to industry standards are imperative to ensure the longevity and safety of the upholstered components.
As welding techniques for upholstery demand meticulous attention to detail, these considerations play a pivotal role in achieving superior results.
Transitioning into the subsequent section about ‘considerations for aircraft interiors’, it is vital to understand how these welding techniques align with the specific requirements of aircraft upholstery.
Considerations for Aircraft Interiors
Transitioning from the considerations for welding techniques in upholstery, the integration of advanced technologies and skilled labor remains essential when addressing the specific requirements of aircraft interiors.
Design flexibility is a crucial factor in aircraft interiors, as it allows for the customization of components to fit the available space while meeting the aesthetic and functional needs of the aircraft. Advanced welding technologies, such as ultrasonic and hot gas welding, enable the creation of intricate designs and shapes, ensuring that the interior components seamlessly integrate into the aircraft’s layout.
Moreover, weight reduction is a significant concern in aircraft interiors, as it directly impacts fuel efficiency and operational costs. Welding techniques that enable the use of lightweight materials, such as advanced thermoplastics and composites, play a pivotal role in achieving weight reduction goals without compromising structural integrity and safety.
Additionally, the skilled labor involved in upholstery welding for aircraft interiors must adhere to strict regulatory standards and quality control measures to ensure that the finished components meet the highest safety and performance requirements.
Considerations for Marine Interiors
A critical aspect of marine interiors is the integration of durable and corrosion-resistant materials to withstand the harsh maritime environment. When considering marine interiors, several important points must be taken into account:
-
Reliability: The use of materials that meet or exceed durability standards is crucial to ensure the interior can withstand the rigors of marine environments, including exposure to saltwater, UV radiation, and temperature fluctuations.
-
Longevity: High-quality, moisture-resistant materials are essential to prevent degradation over time, maintaining the integrity and aesthetics of the interior for an extended lifespan.
-
Safety: The selection of materials that are resistant to mold, mildew, and other microbial growth is vital for ensuring a healthy and hygienic environment for occupants.
-
Aesthetics: While durability and moisture resistance are paramount, the materials chosen should also contribute to an aesthetically pleasing interior, enhancing the overall experience for passengers and crew.
Considering these factors is essential to ensure that marine interiors are not only durable and resistant to moisture but also meet stringent safety and aesthetic standards. This attention to detail is imperative for creating comfortable and long-lasting marine interiors.
The next section will delve into the crucial aspect of quality assurance in upholstery welding.
Quality Assurance in Upholstery Welding
In ensuring the durability and longevity of marine interiors, a rigorous approach to quality assurance in upholstery welding is imperative.
Quality control in upholstery welding involves adhering to stringent inspection standards to guarantee the structural integrity and aesthetic appeal of the final product.
Upholstery welding quality assurance begins with the selection of high-quality materials and the employment of skilled craftsmen with expertise in welding techniques specific to marine interiors.
Throughout the welding process, continuous inspection and monitoring are essential to identify and rectify any potential defects or imperfections. These inspections encompass various factors including seam strength, material distortion, and weld consistency.
Additionally, adherence to industry regulations and standards is paramount in maintaining quality control.
Implementing comprehensive quality assurance measures not only ensures the safety and reliability of marine interiors but also contributes to customer satisfaction and the longevity of the upholstery.
Upholstery welding for marine interiors demands unwavering attention to detail and a commitment to upholding the highest inspection standards to deliver superior and enduring products.
Frequently Asked Questions
What Are the Most Common Materials Used in Upholstery Welding for Aircraft and Marine Interiors?
The most common materials used in upholstery welding for aircraft and marine interiors include vinyl, leather, and synthetic fabrics. Welding techniques such as hot air, radio frequency, and ultrasonic welding are often employed for joining these materials.
Are There Any Regulations or Standards Specific to Upholstery Welding in Aircraft and Marine Interiors?
Regulations and standards specific to upholstery welding in aircraft and marine interiors are critical to ensure compliance, safety, and innovation. These guidelines help maintain design elements while adhering to stringent industry requirements for quality and durability.
How Does Upholstery Welding Compare to Traditional Stitching or Gluing Methods in Terms of Durability and Longevity?
Upholstery welding offers superior durability compared to traditional stitching or gluing methods. It provides an average longevity of 15-20 years, significantly outperforming alternatives. This makes it a compelling choice for aircraft and marine interiors.
What Are the Typical Maintenance and Repair Requirements for Upholstery Welding in Aircraft and Marine Interiors?
Typical maintenance and repair requirements for upholstery welding involve regular inspections, use of specialized welding materials, adherence to regulations and standards, and addressing unique design elements. Welding provides durability and offers custom limitations compared to stitching or gluing methods.
Can Upholstery Welding Be Used for Custom or Unique Design Elements in Aircraft and Marine Interiors, and What Are the Limitations?
Innovative techniques in custom design and unique elements for interior aesthetics can be achieved through upholstery welding. However, limitations may arise in complex designs or with certain materials, requiring careful consideration for creative applications.
Conclusion
In conclusion, upholstery welding offers a seamless and durable solution for aircraft and marine interiors. With its advantages in strength, aesthetics, and customization, it has become a popular choice for interior design.
However, ‘the devil is in the details,’ and careful consideration of welding techniques and quality assurance is essential for successful implementation.
Whether it’s in the air or on the water, upholstery welding is a critical aspect of creating comfortable and safe interior spaces for passengers and crew.
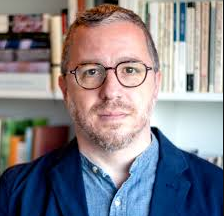
Dillon Hince, an expert in the realm of upholstery welding, brings a wealth of knowledge and experience to the craft. As the driving force behind nodpu.com, Dillon combines a passion for precision and creativity, offering unique insights into the art of seamlessly melding fabrics and materials. With a commitment to excellence, Dillon Hince is your go-to resource for innovative upholstery welding techniques, transforming ordinary pieces into extraordinary works of functional art.