Upholstery Welding for Automotive Interiors
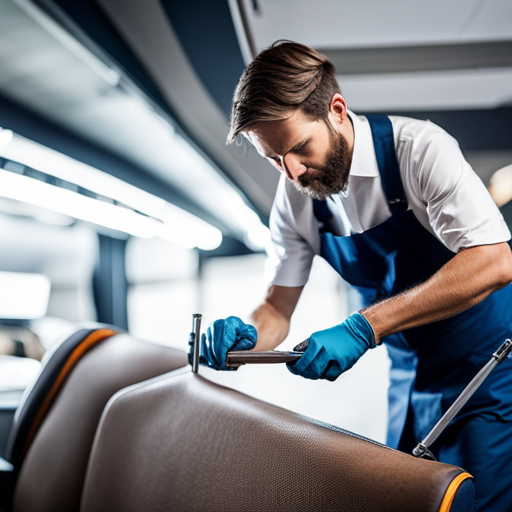
While traditional sewing methods have been the go-to for automotive upholstery, the evolution of upholstery welding has sparked interest in the automotive industry.
This article delves into the world of upholstery welding for automotive interiors, exploring the importance, materials, techniques, tools, and safety measures.
From enhancing durability to achieving intricate designs, upholstery welding offers a precise and efficient solution for automotive restoration and customization.
Importance of Upholstery Welding
The importance of upholstery welding lies in its ability to enhance the structural integrity and durability of automotive interiors. Welding techniques are crucial for ensuring that the upholstery in vehicles can withstand the stresses and strains of regular use. By using welding to reinforce the various components of the interior, such as the seats, door panels, and dashboard, automotive manufacturers can significantly increase the lifespan of these parts, reducing the need for frequent repairs or replacements. This increased durability directly contributes to the cost efficiency of vehicle ownership, as it minimizes maintenance expenses for the owner over time.
Furthermore, upholstery welding allows for customization, enabling manufacturers to create unique and aesthetically pleasing interior designs. Welding techniques provide the flexibility to combine different materials, textures, and shapes, resulting in visually appealing and comfortable automotive interiors. The ability to customize upholstery through welding also adds value to the vehicle, attracting potential buyers who seek individuality and style in their automobiles.
Ultimately, the importance of upholstery welding cannot be overstated, as it plays a vital role in ensuring the longevity, aesthetics, and cost efficiency of automotive interiors.
Types of Materials for Upholstery Welding
Upholstery welding techniques are essential for incorporating a diverse range of materials into automotive interiors, allowing manufacturers to reinforce the structural integrity and customize the aesthetics of the upholstery.
When it comes to upholstery welding, various materials are used to achieve the desired functional and visual outcomes. Common welding materials include PVC, polyurethane, vinyl, leather, and fabric. Each material requires specific welding techniques to ensure a strong and durable bond.
For instance, PVC and polyurethane often utilize hot air welding, which involves using heated air to soften the materials and then pressing them together to create a seamless weld. On the other hand, vinyl and leather may require radio frequency welding, where an electromagnetic field is used to generate heat and bond the materials. Additionally, fabric welding techniques involve ultrasonic welding, a process that uses high-frequency ultrasonic acoustic vibrations to join the materials.
Understanding the appropriate welding materials and techniques for each material is crucial for achieving high-quality, long-lasting automotive upholstery. With a grasp of these materials and techniques, it becomes possible to explore the common upholstery welding techniques in more detail.
Common Upholstery Welding Techniques
Commonly employed welding techniques for automotive upholstery include hot air welding for PVC and polyurethane, radio frequency welding for vinyl and leather, and ultrasonic welding for fabric. Each technique is tailored to the specific material’s requirements, ensuring seamless joins and precision welding in automotive upholstery.
Hot air welding for PVC and polyurethane uses hot air to soften the materials and then press them together, creating a strong and durable bond.
Radio frequency welding for vinyl and leather utilizes radio frequency energy to create heat, bonding the materials together seamlessly without the need for adhesives or additional materials.
Ultrasonic welding for fabric employs ultrasonic vibrations to create heat, fusing the fabric together with precision and strength.
In some cases, laser welding is utilized for intricate and specialized automotive upholstery, providing an exceptionally precise and clean weld.
These techniques are essential for ensuring the quality and durability of automotive upholstery, contributing to the overall comfort and aesthetic appeal of the vehicle interior.
Moving forward, it is important to explore the tools and equipment necessary for executing these welding techniques effectively.
Tools and Equipment for Upholstery Welding
Discussing the tools and equipment required for upholstery welding, it is crucial to ensure that each technique is supported by the appropriate machinery and resources to achieve precise and durable results. Upholstery welding tools and equipment commonly include:
- A hot air gun or a handheld plastic welder for thermoplastic materials
- A heat gun
- A hot stapler for repairing tears and attaching fabric
- A sewing machine for stitching fabric
Safety measures such as proper ventilation requirements and the use of protective gear, including gloves and goggles, are essential during the welding process to prevent inhalation of fumes and protect the welder from burns and eye injuries.
Best practices involve understanding the material types being worked on, especially when engaging in automotive restoration, as different materials require specific welding techniques and equipment.
Moreover, it’s crucial to have easy accessibility to a fire extinguisher in the workspace to swiftly address any potential fire hazards.
Car owner benefits of using the correct tools and equipment for upholstery welding include a professional and long-lasting finish, as well as the preservation of the vehicle’s interior aesthetics and structural integrity.
Benefits of Upholstery Welding for Car Owners
Car owners benefit from upholstery welding through the preservation of their vehicle’s interior aesthetics and structural integrity. Upholstery welding offers several advantages that contribute to the overall maintenance and longevity of a car’s interior.
-
Enhanced Durability: Welding reinforces the joints and seams of upholstery, ensuring that the interior materials remain intact and withstand daily wear and tear more effectively.
-
Improved Safety: Welded seams and joints provide better structural support, which can be crucial in the event of a collision or sudden impact.
-
Prevention of Moisture Damage: Welding helps seal seams, preventing moisture from seeping into the interior and causing damage such as mold or rust.
-
Long-Term Cost Savings: With a more durable and structurally sound interior, car owners can potentially reduce long-term maintenance and repair costs, as well as preserve the vehicle’s resale value.
Upholstery Welding in Automotive Restoration
In automotive restoration, upholsterers often incorporate welding techniques to meticulously repair and reinforce the interior components of classic and vintage vehicles. Welding plays a crucial role in restoring the structural integrity and aesthetics of automotive interiors.
When dealing with classic cars, it’s common to encounter damaged or deteriorated upholstery components such as seat frames, door panels, and trim pieces. Welding allows for the precise restoration of these parts, ensuring that they meet the original specifications and maintain the vehicle’s authenticity.
Additionally, welding techniques are employed to address issues such as broken seat brackets, torn or worn-out upholstery, and damaged mounting points for interior components.
The use of welding in automotive restoration enables upholsterers to achieve seamless repairs and modifications, ensuring that the interior of the vehicle not only looks authentic but also meets modern safety and performance standards.
Safety Measures in Upholstery Welding
When engaging in upholstery welding for automotive interiors, it is crucial to prioritize safety measures to mitigate potential risks.
This includes the use of appropriate protective gear to safeguard against burns and fumes, as well as ensuring sufficient ventilation systems are in place to minimize exposure to hazardous emissions.
Additionally, accessibility to fire extinguishers should be maintained to swiftly address any unforeseen combustion incidents.
Protective Gear Importance
Implementing proper protective gear is essential for ensuring the safety of workers during upholstery welding for automotive interiors. Upholstery welding poses various workplace hazards, making it crucial for workers to use the appropriate protective gear to mitigate the risks.
The following protective gear is essential for upholstery welding:
- Welding helmet with a protective visor to shield the face and eyes from sparks and UV radiation
- Flame-resistant clothing to prevent burns from sparks and hot metal
- Respirator or mask to protect against fumes and airborne particles
- Welding gloves to shield hands from heat and sharp objects
These safety measures are vital for safeguarding workers from potential injuries and health risks associated with upholstery welding.
Once the protective gear is in place, the next critical consideration is the ventilation system requirements for upholstery welding.
Ventilation System Requirements
To ensure the safety and well-being of workers during upholstery welding for automotive interiors, the efficient removal of airborne contaminants becomes imperative, necessitating the implementation of robust ventilation system requirements.
Ventilation requirements for upholstery welding must adhere to strict safety standards to protect workers from inhaling hazardous fumes and particulates. The ventilation system should provide a sufficient air exchange rate to dilute and remove contaminants from the welding area, ensuring air quality remains within permissible exposure limits.
Proper ventilation design should encompass the positioning of exhaust hoods near the welding operation, the use of high-efficiency particulate air (HEPA) filters, and the incorporation of local exhaust ventilation to capture and remove airborne contaminants at the source.
Regular maintenance and monitoring of the ventilation system are essential to uphold welding safety standards and protect workers from potential health risks.
Fire Extinguisher Accessibility
Fire extinguisher accessibility is a crucial safety measure in upholstery welding, ensuring the prompt and effective response to potential fire hazards that may arise during the welding process.
To enhance fire safety and emergency response, the following measures should be implemented:
- Place fire extinguishers strategically in designated areas around the welding site.
- Ensure that all personnel are trained in the proper operation of fire extinguishers.
- Regularly inspect and maintain fire extinguishers to guarantee their functionality.
- Clearly label and mark the locations of fire extinguishers for easy identification in case of an emergency.
These measures are essential for maintaining a safe working environment during upholstery welding, enabling quick and effective responses to any fire-related incidents.
Upholstery Welding Best Practices
When upholstering automotive interiors, it is essential to adhere to best practices for upholstery welding in order to ensure the durability and quality of the finished product. Welding techniques play a crucial role in achieving efficient and effective joins within automotive upholstery. It is important to employ proper welding methods such as hot air or hot wedge welding, which are suitable for joining various types of automotive upholstery materials. Efficiency in welding techniques not only ensures a strong bond but also contributes to the overall quality and aesthetics of the interior components.
Quality control and inspection processes are integral to upholding high standards in upholstery welding. Regular inspections during the welding process help identify any defects or inconsistencies, allowing for immediate corrective measures. Additionally, quality control measures should be implemented to evaluate the strength and integrity of the welds to ensure they meet industry standards and safety regulations.
Frequently Asked Questions
What Are the Potential Environmental Impacts of Upholstery Welding for Automotive Interiors?
The potential environmental impacts of upholstery welding for automotive interiors can include air and noise pollution, energy consumption, and waste generation. Implementing sustainable practices, such as using eco-friendly materials and efficient production processes, can mitigate these impacts.
How Does Upholstery Welding Affect the Overall Value of a Vehicle?
Upholstery welding can impact a vehicle’s overall value by enhancing its aesthetic appeal. This process ensures seamless, durable interior finishes, contributing to a vehicle’s perceived quality and desirability, potentially increasing its market value.
Are There Any Specific Regulations or Requirements for Upholstery Welding in Different Regions or Countries?
Regulatory compliance and safety standards for upholstery welding in different regions or countries vary. Specific requirements may include certification, material standards, and weld quality. Adhering to these standards is crucial for ensuring product safety and market access.
Can Upholstery Welding Be Used to Repair or Modify Vintage or Classic Car Interiors?
Upholstery welding can be a viable method for restoring vintage car interiors. It offers precise repairs and modifications, ensuring the preservation of original design and materials. When executed by skilled professionals, it can effectively rejuvenate classic car upholstery.
How Does Upholstery Welding Compare to Other Methods of Repairing or Modifying Automotive Interiors, Such as Sewing or Adhesive Bonding?
When comparing upholstery welding to sewing for automotive interiors, welding offers stronger and more durable seams. Compared to adhesive bonding, welding provides a more secure and long-lasting bond, especially in high-stress areas.
Conclusion
In conclusion, upholstery welding plays a crucial role in automotive interiors. It offers both durability and aesthetic appeal, making it an essential aspect of car maintenance. By utilizing various materials and techniques, car owners can benefit from a well-maintained and visually appealing interior.
Upholstery welding not only contributes to automotive restoration but also ensures safety and longevity. The precision and skill required for upholstery welding are unmatched. This makes it an indispensable practice for automotive interior upkeep, surpassing all other maintenance methods.
Overall, upholstery welding is a crucial practice that car owners should prioritize. It not only enhances the overall appearance of the interior but also guarantees its longevity and safety. With the right materials and techniques, upholstery welding can transform any automotive interior into a well-maintained and visually appealing space.
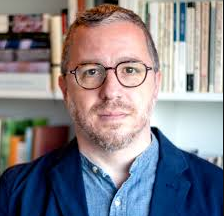
Dillon Hince, an expert in the realm of upholstery welding, brings a wealth of knowledge and experience to the craft. As the driving force behind nodpu.com, Dillon combines a passion for precision and creativity, offering unique insights into the art of seamlessly melding fabrics and materials. With a commitment to excellence, Dillon Hince is your go-to resource for innovative upholstery welding techniques, transforming ordinary pieces into extraordinary works of functional art.