Upholstery Welding in Furniture Manufacturing
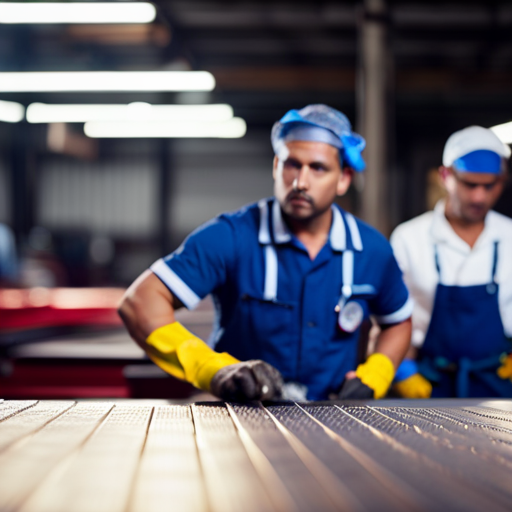
In the intricate world of furniture manufacturing, the art of upholstery welding stands as the cornerstone for creating durable and aesthetically pleasing pieces. Utilizing the juxtaposition of traditional craftsmanship with modern welding techniques, this process seamlessly melds fabrics and metals together.
This article delves into the essential aspects of upholstery welding, from materials and techniques to quality standards and future trends, providing a comprehensive understanding of this vital aspect of furniture production.
Upholstery Welding Process
The upholstery welding process in furniture manufacturing involves the fusion of fabric and foam materials to the frame using specialized welding equipment. Welding techniques play a crucial role in ensuring the durability and quality of the final upholstered product. Different welding methods such as hot air, hot wedge, and radio frequency welding are utilized based on the type of fabric and foam being used. These techniques allow for a strong and seamless bond between the materials and the frame, ensuring the longevity of the furniture piece.
Fabric durability is a key consideration in the upholstery welding process. The welding technique must not compromise the integrity of the fabric, ensuring that it remains resilient to wear and tear. The welding process should maintain the fabric’s original tensile strength and tear resistance while creating a firm bond with the foam and frame. Additionally, the welding process should not cause discoloration or damage to the fabric, ensuring that the aesthetic appeal of the furniture is preserved.
Materials Used in Upholstery Welding
The materials used in upholstery welding play a crucial role in the overall quality and durability of the furniture. Weldable synthetic fabrics, such as vinyl and polyurethane, are commonly used for their versatility and strength.
Additionally, metal frame construction and heat-sealing techniques are integral in ensuring the longevity and structural integrity of the upholstered furniture.
Weldable Synthetic Fabrics
Weldable synthetic fabrics play a crucial role in upholstery welding for furniture manufacturing. These fabrics have a wide range of applications, from creating seamless upholstery to reinforcing fabric joints. Fabric welding techniques, such as hot air welding and hot wedge welding, are commonly used to join weldable synthetic fabrics.
Hot air welding uses heated air to melt the fabric edges, creating a strong bond, while hot wedge welding employs a heated wedge to join the materials. These techniques ensure durable and aesthetically pleasing seams, enhancing the overall quality of upholstered furniture.
As we delve into the significance of weldable synthetic fabrics, it becomes evident that their integration is essential for achieving high-quality upholstery welding.
Now, let’s transition into the subsequent section about ‘metal frame construction’.
Metal Frame Construction
When considering the construction of metal frames for upholstery welding in furniture manufacturing, it is essential to carefully select and assess the materials used. The success of upholstery welding greatly relies on the quality and suitability of the metal frame design and the materials used in its construction.
Common materials for metal frame construction include steel, aluminum, and iron, each offering distinct advantages for welding applications. Steel is known for its strength and durability, making it a popular choice for heavy-duty furniture. Aluminum, on the other hand, is valued for its lightweight properties and resistance to corrosion, ideal for outdoor furniture. Iron, while less commonly used in modern furniture manufacturing, still finds its place in creating classic and ornate metal frames.
Understanding the properties and welding characteristics of these materials is crucial in achieving high-quality upholstery welding in furniture manufacturing.
Heat-Sealing Techniques
Before applying heat-sealing techniques in upholstery welding for furniture manufacturing, it is essential to carefully select materials that exhibit optimal welding characteristics. Heat sealing technology plays a crucial role in joining upholstery materials, such as fabrics and synthetic fibers, by using heat and pressure to create strong, durable bonds.
This technique is widely used in the furniture industry for creating seamless seams, decorative elements, and functional components in upholstered furniture. The industry applications of heat sealing technology extend to automotive upholstery, medical furniture, and outdoor furniture manufacturing, where it enables the production of high-quality, long-lasting products.
Understanding the materials used in upholstery welding and their compatibility with heat-sealing techniques is fundamental to achieving superior quality and performance in furniture manufacturing.
Transitioning to the subsequent section, let’s explore the benefits of upholstery welding.
Benefits of Upholstery Welding
The implementation of upholstery welding in furniture manufacturing offers significant cost savings and improved structural integrity.
One of the key benefits of upholstery welding is the cost savings it provides. By using welding techniques to join upholstery materials, manufacturers can reduce the need for additional hardware or fasteners, ultimately lowering production costs. Additionally, welding creates durable and strong seams, enhancing the overall durability and longevity of the furniture. This results in reduced maintenance and repair expenses for both manufacturers and consumers.
Furthermore, upholstery welding contributes to the strength of the furniture by creating seamless and robust connections between materials. This ensures that the furniture can withstand the rigors of regular use, including weight and pressure, without compromising its structural integrity. As a result, furniture manufactured using upholstery welding is less prone to wear and tear, leading to longer lifespans and higher customer satisfaction.
Techniques for Upholstery Welding
Upholstery welding in furniture manufacturing involves employing a variety of techniques to join upholstery materials, contributing to the cost savings, structural integrity, and overall durability of the furniture. Two common welding techniques used in upholstery manufacturing are hot air welding and radio frequency (RF) welding.
Welding Technique | Description |
---|---|
Hot Air Welding | Involves using heated air to soften the materials, then pressing them together to form a strong bond. This technique is commonly used for joining synthetic fabrics and vinyl. |
Radio Frequency (RF) Welding | Utilizes high-frequency electromagnetic energy to generate heat in the materials, creating a strong seam. RF welding is often preferred for joining fabrics that contain thermoplastic components. |
In addition to welding techniques, seam sealing is an essential process in upholstery welding. Seam sealing involves applying a sealant to the stitched seams, preventing water and other liquids from penetrating the upholstery. This not only enhances the durability of the furniture but also ensures its resistance to stains and spills. These techniques collectively contribute to the overall quality and longevity of upholstered furniture.
Quality Standards in Upholstery Welding
When ensuring the quality of upholstery welding in furniture manufacturing, adherence to industry standards is paramount. Quality assurance in upholstery welding is essential for meeting industry requirements and ensuring the durability and safety of furniture products. Upholstery welding must comply with stringent quality standards to guarantee the structural integrity and longevity of the furniture.
Industry requirements for upholstery welding encompass factors such as weld strength, visual appearance, and material compatibility. Weld strength is crucial for withstanding the stresses and loads experienced by furniture during everyday use, while visual appearance contributes to the aesthetic appeal of the finished product. Additionally, material compatibility ensures that the welding process does not compromise the integrity of the materials being joined.
Upholstery welding must meet these quality standards to produce furniture that is not only visually appealing but also durable and safe for consumers. Achieving and maintaining these standards requires stringent quality control measures and skilled welders who are well-versed in industry best practices. Upholstery welding equipment plays a pivotal role in meeting these quality standards, as it directly influences the precision and quality of welds in furniture manufacturing.
Upholstery Welding Equipment
When it comes to upholstery welding equipment, it is essential to consider the different types of welding available. Understanding the nuances of each type of welding and their applications in furniture manufacturing is crucial for achieving high-quality and durable upholstery.
The compatibility of materials being welded is another important factor to consider. Different materials may require different welding techniques or equipment to ensure a strong and secure bond.
Additionally, the efficiency of the welding process should be taken into account. Ensuring that the welding process is efficient can significantly impact production timelines and overall manufacturing costs.
Therefore, when selecting upholstery welding equipment, it is important to consider the type of welding, material compatibility, and efficiency to achieve the best results in terms of quality, durability, and cost-effectiveness.
Types of Welding
The furniture manufacturing industry utilizes various types of welding equipment specifically designed for upholstery applications. When it comes to upholstery welding, two primary types of welding are commonly used:
-
Resistance welding: This method involves the use of electric current to generate heat and join metal pieces. It is often favored for its speed and efficiency in upholstery applications.
-
TIG welding: Also known as Tungsten Inert Gas welding, this technique provides high precision and control, making it suitable for delicate upholstery work.
Upholstery welding, like any other welding process, requires strict adherence to welding safety protocols to prevent accidents and ensure a secure working environment. Understanding the specific welding applications in furniture manufacturing is crucial for achieving high-quality upholstery welds.
Material Compatibility
How does material compatibility influence the selection of upholstery welding equipment in furniture manufacturing? Material compatibility plays a crucial role in determining the appropriate upholstery welding equipment for furniture manufacturing. Different upholstery materials such as leather, vinyl, and fabric require specific welding techniques and equipment to ensure a strong and durable bond. Material testing is essential to understand the characteristics of each upholstery material and determine the most suitable welding method. Furthermore, design considerations, such as the thickness and flexibility of the materials, also impact the selection of welding equipment. Manufacturers must carefully assess the material compatibility and design requirements to choose the right welding equipment that ensures high-quality and long-lasting upholstered furniture.
Upholstery Material | Welding Technique | Equipment Required |
---|---|---|
Leather | Hot air welding | Hot air welding gun |
Vinyl | Radio frequency welding | Radio frequency welding machine |
Fabric | Ultrasonic welding | Ultrasonic welding machine |
Welding Process Efficiency
Considering the diverse upholstery materials and their specific welding requirements, the efficiency of the welding process in furniture manufacturing is paramount in ensuring optimal bonding and product quality. Upholstery welding equipment plays a crucial role in improving productivity and reducing waste.
To enhance welding process efficiency, furniture manufacturers should consider the following:
-
Investing in Advanced Welding Equipment: Upgrading to state-of-the-art welding machinery can significantly improve efficiency by ensuring precise and consistent welds.
-
Implementing Lean Manufacturing Practices: Streamlining the welding process through lean manufacturing principles can minimize waste and maximize productivity.
-
Training and Skill Development: Providing comprehensive training for the workforce on equipment operation and welding techniques can further enhance process efficiency while reducing errors.
Future Trends in Upholstery Welding
Advancements in upholstery welding technology are expected to revolutionize the furniture manufacturing industry in the coming years. Market demand for sustainable and durable furniture has been a driving force behind technological advancements in upholstery welding. Manufacturers are increasingly embracing innovative techniques such as ultrasonic welding and laser welding to meet this demand. These methods not only ensure stronger and more aesthetically pleasing welds but also have a reduced environmental impact compared to traditional methods. Additionally, the cost effectiveness of these advanced welding technologies is becoming more evident, as they allow for efficient use of materials and reduced production time.
Looking ahead, the future trends in upholstery welding are likely to focus on further enhancing the sustainability and cost efficiency of the process. This may involve the development of even more eco-friendly welding technologies and the integration of automation for increased precision and productivity. Furthermore, the use of advanced materials, such as composites, in combination with cutting-edge welding methods is expected to open up new design possibilities and further drive the evolution of furniture manufacturing.
As the industry continues to prioritize sustainability and cost effectiveness, upholstery welding will play a crucial role in shaping its future landscape.
Frequently Asked Questions
Can Upholstery Welding Be Used on Outdoor Furniture as Well?
Yes, upholstery welding can be used on outdoor furniture. Depending on the welding techniques and materials used, it can provide outdoor durability and weather resistance. Careful consideration of material compatibility is essential for ensuring longevity in outdoor settings.
Are There Any Environmental Concerns or Regulations Related to Upholstery Welding?
Environmental impact and regulatory compliance are critical aspects of upholstery welding. It’s important to address any potential environmental concerns and ensure compliance with regulations to mitigate any adverse effects on the environment.
What Are the Typical Maintenance and Repair Requirements for Furniture That Has Undergone Upholstery Welding?
Maintenance and repair requirements for furniture that has undergone upholstery welding involve regular cleaning, inspection for wear and tear, and addressing any issues promptly to ensure durability. Repair costs can vary based on the extent of damage.
Are There Any Limitations to the Types of Materials That Can Be Used in Upholstery Welding?
Limitations on material compatibility in upholstery welding depend on the desired outcome and the application. Factors such as outdoor furniture, weather resistance, and the welding technique used can influence the choice of materials.
How Does Upholstery Welding Compare to Traditional Upholstery Techniques in Terms of Cost and Durability?
When examining upholstery techniques, cost comparison and durability analysis are crucial factors. Upholstery welding offers potential cost savings and durability benefits compared to traditional methods, making it an appealing option for furniture manufacturing.
Conclusion
In conclusion, upholstery welding is a crucial process in furniture manufacturing, ensuring durability and strength in upholstered furniture.
The use of advanced materials and techniques, along with adherence to quality standards, leads to high-quality and long-lasting products.
The future trends in upholstery welding are expected to revolutionize the industry, making it even more efficient and innovative.
The impact of upholstery welding on the furniture manufacturing industry is as significant as a tidal wave reshaping the landscape.
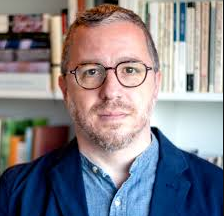
Dillon Hince, an expert in the realm of upholstery welding, brings a wealth of knowledge and experience to the craft. As the driving force behind nodpu.com, Dillon combines a passion for precision and creativity, offering unique insights into the art of seamlessly melding fabrics and materials. With a commitment to excellence, Dillon Hince is your go-to resource for innovative upholstery welding techniques, transforming ordinary pieces into extraordinary works of functional art.