Upholstery Welding in High-Pressure Environments
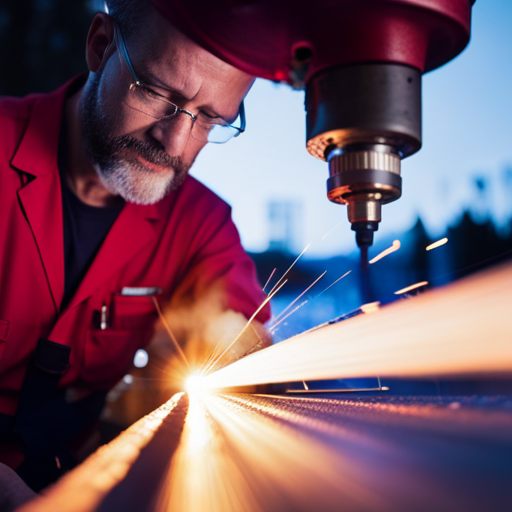
As the fabric of industrial progress is woven tighter, the demand for upholstery welding in high-pressure environments intensifies.
This article delves into the intricacies of achieving precise and durable welds in challenging conditions. From understanding the unique challenges to exploring the latest techniques and safety considerations, this comprehensive guide equips professionals with the knowledge to excel in high-pressure upholstery welding.
Join us as we unravel the complexities and unveil the future of this critical welding discipline.
Understanding High-Pressure Welding Challenges
In high-pressure welding environments, upholsterers face unique challenges that require specialized knowledge and skills to ensure successful outcomes. One of the primary challenges is the need for precision and accuracy in welding techniques, as any deviation can lead to compromised structural integrity. Solutions to this include the use of advanced welding equipment and the implementation of meticulous welding techniques to mitigate the risk of defects.
Additionally, risk management plays a crucial role in high-pressure welding, as any oversight can result in costly rework or, worse, compromised safety. Upholsterers must be well-versed in risk assessment and proactive measures to prevent potential hazards. Understanding the complexities of high-pressure welding challenges is essential for upholsterers to navigate the intricacies of the process effectively and deliver superior quality work. This comprehension allows them to implement the necessary solutions and risk management strategies to ensure the integrity of the welds.
Transitioning into the subsequent section, it is imperative to explore the materials and equipment essential for upholstery welding in high-pressure environments.
Materials and Equipment for Upholstery Welding
Upholsterers require specialized materials and equipment to meet the demands of welding in high-pressure environments with precision and quality. When selecting welding materials, it is crucial to consider their compatibility with the specific upholstery fabrics and the pressure levels the final product will be subjected to. Equally important is the equipment selection, as using the right welding machines and tools can significantly impact the quality and durability of the welds.
Here are key considerations for upholstery welding materials and equipment:
-
Welding Materials:
-
Choose flame-retardant and heat-resistant materials that can withstand high-pressure conditions.
-
Opt for welding rods or tapes that are compatible with the upholstery fabric to ensure a strong bond.
-
Consider using specialized adhesives designed for high-pressure applications to reinforce the welded seams.
-
Equipment Selection:
-
Select a welding machine with adjustable heat settings to accommodate different upholstery materials and thicknesses.
-
Use precision welding tools such as hot air welders or wedge welders for intricate and high-pressure welds.
-
Invest in quality finishing tools like trimmers and rollers to ensure smooth and durable welds.
Techniques for Welding in High-Pressure Environments
In upholstery welding, the choice of materials is crucial in high-pressure environments. By optimizing the welding process, the strength and integrity of the welds can be maintained under extreme pressure.
Additionally, implementing safety measures for welders is essential to ensure their well-being and the quality of the welds in such demanding conditions.
Material Selection Considerations
Conducting thorough research on suitable materials for welding in high-pressure environments is essential for ensuring the durability and integrity of upholstered components. When considering material selection for welding in high-pressure environments, it is crucial to take into account material compatibility and performance requirements.
This involves evaluating the ability of the material to withstand high-pressure conditions and its compatibility with other materials in the upholstered components. The following factors should be considered during material selection:
- Material compatibility with the welding process and other components
- Assessing the material’s ability to bond effectively in high-pressure conditions
- Performance requirements in high-pressure environments
- Evaluating the material’s strength, durability, and resistance to pressure-induced deformation
- Long-term reliability and maintenance considerations
- Anticipating the material’s performance over time and its maintenance needs to ensure sustained integrity.
Welding Process Optimization
Assessing the material’s compatibility with high-pressure welding techniques is crucial for ensuring the integrity and durability of upholstered components. Optimizing productivity and welding procedure improvements are essential for achieving high-quality welds in these demanding environments. To achieve this, various techniques can be employed to enhance the welding process, such as optimizing welding parameters, using advanced welding equipment, and implementing efficient workflow strategies. The table below outlines key welding process optimization techniques that can be applied to enhance productivity and improve the overall welding procedure in high-pressure environments.
Optimization Technique | Description |
---|---|
Parameter Optimization | Fine-tuning welding parameters for optimal results |
Advanced Welding Equipment | Utilizing state-of-the-art welding machinery |
Efficient Workflow Strategies | Streamlining processes for improved efficiency |
Safety Measures for Welders
To ensure the safety and efficiency of welders in high-pressure environments, it is imperative to implement comprehensive safety measures and specialized techniques tailored to the unique challenges posed by upholstery welding.
-
Safety Gear: Welders should be equipped with appropriate personal protective equipment such as flame-resistant clothing, gloves, and helmets designed to withstand high-pressure welding conditions.
-
Training Programs: Employers should provide welders with specialized training programs focused on high-pressure welding safety, including techniques for working with pressurized upholstery materials and emergency procedures.
These measures are essential to mitigate the risks associated with welding in high-pressure environments and ensure the well-being of the welding personnel.
Transitioning into the subsequent section about ‘safety considerations in high-pressure upholstery welding’, it is crucial to delve into specific safety protocols and best practices for welders operating in such demanding conditions.
Safety Considerations in High-Pressure Upholstery Welding
When it comes to upholstery welding in high-pressure environments, safety considerations are paramount. This includes ensuring the proper functioning and maintenance of welding equipment, as well as being aware of the pressure levels involved in the process.
Additionally, having a well-prepared emergency response plan in place is crucial for addressing any unforeseen incidents that may arise during upholstery welding in high-pressure environments.
Welding Equipment Safety
In high-pressure upholstery welding environments, ensuring the safety of welding equipment is paramount for preventing accidents and ensuring efficient operations.
- Safety Precautions
- Regular inspections of welding equipment to identify and address any potential safety hazards.
- Implementation of safety protocols, including the use of personal protective equipment and adherence to operational guidelines.
- Training programs for personnel to ensure they are aware of safety procedures and understand how to respond to emergencies.
Proper Equipment Maintenance is essential to uphold safety standards. This includes:
- Regular cleaning and upkeep of welding equipment to prevent malfunctions.
- Scheduled maintenance checks and timely repairs to address any issues promptly.
- Compliance with manufacturer-recommended maintenance procedures to uphold equipment integrity and safety.
Pressure Level Awareness
Maintaining awareness of pressure levels is crucial for ensuring safety in high-pressure upholstery welding environments. Pressure level monitoring is essential to prevent potential hazards such as equipment failure or rupturing of materials.
Regular checks and proper calibration of pressure monitoring devices should be conducted to ensure accurate readings. Additionally, welding parameter adjustments must be made in accordance with the monitored pressure levels to maintain the integrity of the welding process.
Operators should be trained to recognize and respond to pressure variations promptly. Clear protocols for handling pressure deviations should be established, including emergency procedures.
Adhering to these safety measures not only mitigates the risk of accidents but also contributes to the overall quality and durability of the welded upholstery products in high-pressure environments.
Emergency Response Preparations
Effective emergency response preparations are essential for ensuring safety in high-pressure upholstery welding environments. To mitigate potential risks, it is crucial to prioritize the following safety considerations:
-
Emergency Response Training: Upholstery welding professionals must undergo comprehensive emergency response training to effectively handle unforeseen situations. This includes training on using fire extinguishers, first aid, and evacuation procedures specific to high-pressure welding environments.
-
Welding Equipment Maintenance: Regular maintenance and inspection of welding equipment are vital to prevent malfunctions that could lead to emergencies. Equipment should be routinely checked for leaks, pressure irregularities, and wear and tear to ensure optimal functionality and safety.
-
Emergency Communication Protocols: Clear and concise communication protocols should be established, ensuring that all personnel are aware of emergency procedures and know how to swiftly communicate and coordinate during critical situations.
Quality Control and Inspection in Upholstery Welding
Quality control and inspection are essential for ensuring the integrity and safety of upholstery welding in high-pressure environments. Upholstery welding must adhere to stringent quality assurance measures to guarantee pressure tolerance and weld strength. Quality control processes involve meticulous defect detection to identify any imperfections that could compromise the integrity of the weld. This is crucial for maintaining the structural integrity of the upholstery in high-pressure settings.
Inspection procedures should encompass comprehensive checks to assess the weld strength, ensuring that it meets the required standards for safety and durability in high-pressure environments. Pressure tolerance is a critical factor in upholstery welding, and quality control measures must ascertain that the welded components can withstand the specified pressure levels without failure.
Moreover, quality control and inspection play a vital role in preventing potential hazards associated with faulty welding in high-pressure environments. Upholstery welding that meets rigorous quality assurance criteria is essential for ensuring the reliability and safety of the upholstered components when subjected to high-pressure conditions. Consequently, adherence to stringent quality control and inspection protocols is imperative for upholding the quality and safety standards of upholstery welding in high-pressure environments.
Future Innovations in High-Pressure Welding
Innovative approaches to high-pressure welding techniques are poised to revolutionize the future of upholstery manufacturing. The following advancements are anticipated to drive the evolution of high-pressure welding:
-
High Temperature Welding Advancements: Breakthroughs in high-temperature welding technology are anticipated to enable the joining of advanced materials, such as pressure-resistant alloys, at elevated temperatures. This will expand the possibilities for creating durable and resilient upholstery components capable of withstanding extreme conditions.
-
Pressure Resistant Materials: The development of new materials with superior pressure resistance properties is expected to enhance the integrity and longevity of welded upholstery components. These materials will enable manufacturers to produce high-pressure resistant upholstery suitable for a wide range of applications, from automotive to aerospace.
-
Automation in High-Pressure Welding: The integration of automation and robotics into high-pressure welding processes is set to streamline production, improve precision, and enhance overall efficiency. Automated systems will enable consistent and reliable welding, reducing the potential for human error and increasing productivity.
These innovations in high-pressure welding are poised to redefine the capabilities and possibilities within the upholstery manufacturing industry, setting the stage for enhanced performance and durability in the products of the future.
Frequently Asked Questions
What Are the Most Common Mistakes to Avoid When Welding Upholstery in High-Pressure Environments?
When welding upholstery, it’s crucial to avoid common mistakes and employ proper welding techniques to prevent damage and preserve materials. The use of suitable welding equipment and adherence to safety protocols are essential for successful outcomes.
How Can Upholsterers Prevent Damage to Materials During High-Pressure Welding?
To prevent damage during high-pressure welding, upholsterers should employ precise welding techniques and carefully handle materials. It’s essential to maintain control over the welding process and exercise caution to preserve the integrity of the upholstery.
Are There Any Special Certifications or Training Required for Welding Upholstery in High-Pressure Environments?
Certification requirements and specialized training are essential for welding in high-pressure environments. Upholsterers need to understand the impact of materials under pressure and adhere to strict safety measures to ensure the integrity of the welds.
What Are the Best Practices for Troubleshooting Welding Issues in High-Pressure Upholstery Welding?
When troubleshooting welding issues in high-pressure environments, it’s critical to employ effective troubleshooting techniques and adhere to strict welding equipment maintenance. Identifying and resolving issues promptly ensures the integrity and safety of the welding process.
How Do Environmental Factors, Such as Temperature and Humidity, Impact Welding in High-Pressure Upholstery Environments?
Environmental factors like temperature and humidity significantly impact welding in high-pressure upholstery environments. Moisture can affect the welding techniques, leading to potential flaws. Adapting to these factors through proper technique adjustments is crucial for successful welding outcomes.
Conclusion
In conclusion, high-pressure upholstery welding presents unique challenges that require specialized materials, equipment, and techniques.
Safety considerations and quality control are paramount in ensuring the integrity of the welds in these environments.
Despite the advancements in high-pressure welding, the future of upholstery welding may rely on innovations that prioritize safety and efficiency.
It’s ironic that while high-pressure welding demands precision and control, it also pushes for continuous improvement and innovation in the industry.
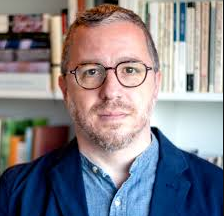
Dillon Hince, an expert in the realm of upholstery welding, brings a wealth of knowledge and experience to the craft. As the driving force behind nodpu.com, Dillon combines a passion for precision and creativity, offering unique insights into the art of seamlessly melding fabrics and materials. With a commitment to excellence, Dillon Hince is your go-to resource for innovative upholstery welding techniques, transforming ordinary pieces into extraordinary works of functional art.